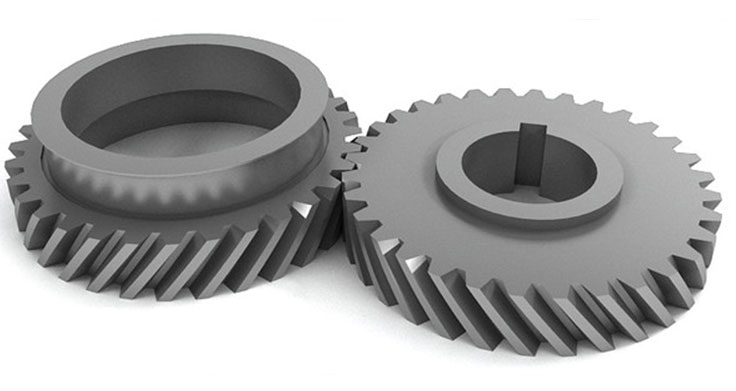
The load-bearing capacity of helical gears is a key factor that contributes to their widespread use in various industrial applications, especially those involving heavy loads and high torque requirements. Helical gears offer several design features that enhance their load-carrying capabilities, making them suitable for demanding mechanical systems. Here’s how helical gears achieve their strength and load-bearing capacity:
1. Helical Tooth Profile:
The helical shape of the gear teeth allows for gradual and continuous contact between meshing gears. This feature spreads the load over multiple teeth along the contact line, distributing the forces more evenly and reducing stress concentrations. As a result, helical gears can handle higher loads compared to spur gears with the same dimensions.
2. Larger Contact Area:
The helical gear’s helix angle increases the effective contact area between meshing gears. A larger contact area means that the load is distributed over more tooth surface, resulting in increased load-carrying capacity and improved torque transmission.
3. Multiple Tooth Contact:
Unlike spur gears, which typically have only two teeth in contact at any given moment, helical gears have several teeth in simultaneous contact. This multi-tooth engagement further enhances load distribution and contributes to the gear’s ability to handle heavy loads.
4. Axial Thrust Absorption:
Helical gears generate an axial thrust force along the gear’s axis due to the helix angle. By pairing helical gears with opposite helix angles (double helical gears or herringbone gears), the axial thrust forces can be canceled out, allowing for better load balancing and minimizing the need for additional thrust bearings.
5. Material Selection and Heat Treatment:
The choice of materials and appropriate heat treatment processes further impact the load-carrying capacity of helical gears. High-quality materials and heat treatment improve the gears’ hardness, strength, and durability, enabling them to withstand higher loads without deformation or failure.
6. Gear Design Optimization:
Careful design considerations, such as selecting suitable helix angles, pressure angles, module or diametral pitch, and gear widths, help optimize the gear’s load-carrying capacity. The gear design process ensures that the gears can handle the intended application’s specific load and torque requirements.
7. Lubrication and Surface Finish:
Proper lubrication is essential for reducing friction and wear in helical gears during operation. Adequate lubrication ensures smooth gear engagement and helps maintain the gear’s load-carrying capacity. Additionally, surface finishing processes like grinding or honing can improve the gear’s strength and wear resistance.
The helical tooth profile, larger contact area, multi-tooth engagement, axial thrust absorption, material selection, heat treatment, design optimization, and lubrication all contribute to the robust load-bearing capacity of helical gears. Their ability to handle high loads and transmit substantial torque makes helical gears an integral part of heavy machinery, industrial drives, automotive transmissions, and other applications requiring reliable power transmission under challenging conditions.