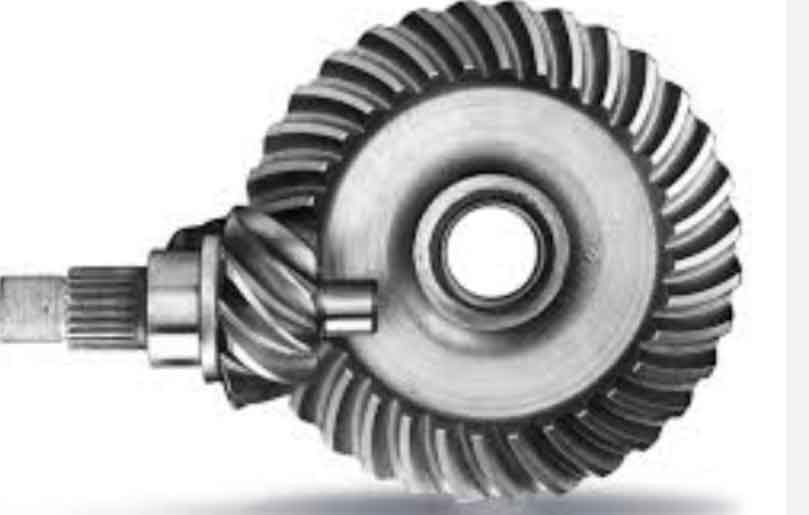
The process of implementing hypoid gears in modern machinery involves several stages, from conceptualization to final application. Engineers carefully design, manufacture, and integrate hypoid gears into the machinery to ensure optimal performance and reliability. Let’s explore the key steps involved in implementing hypoid gears in modern machinery:
1. Requirement Analysis:
The first step is to conduct a thorough requirement analysis. Engineers assess the machinery’s performance needs, torque requirements, speed ratios, space constraints, noise considerations, and other relevant factors to determine if hypoid gears are the ideal choice for the application.
2. Gear Design:
Once hypoid gears are selected as the preferred solution, the gear design process begins. Engineers create the gear geometry, determine the hypoid axis angle, optimize the tooth profile, and calculate the gear ratio based on the machinery’s requirements.
3. CAD Modeling and Simulation:
Computer-aided design (CAD) software is used to create 3D models of the hypoid gears and their mating components. Simulation tools help analyze the gear meshing, contact pattern, and load distribution to verify that the gears meet the performance criteria.
4. Material Selection and Heat Treatment:
Engineers carefully choose the appropriate materials for the hypoid gears based on the application’s demands, considering factors such as strength, wear resistance, and heat dissipation. Proper heat treatment is applied to enhance the gears’ durability and hardness.
5. Manufacturing:
The precise manufacturing of hypoid gears is critical for their performance. Advanced manufacturing techniques, such as CNC machining and gear grinding, ensure accurate tooth profiles and tight tolerances.
6. Quality Control:
During the manufacturing process, strict quality control measures are implemented to ensure that the gears meet the specified requirements. Gear tooth profiles, surface finish, and dimensional accuracy are carefully inspected.
7. Gear Assembly:
The hypoid gears are assembled into gearboxes or gear systems. Proper alignment and backlash adjustment are performed to optimize gear performance and minimize noise.
8. Lubrication:
Adequate lubrication is essential for the smooth operation and durability of hypoid gears. Engineers select the appropriate lubricant based on the application’s operating conditions.
9. Testing and Validation:
Once the machinery is assembled, it undergoes rigorous testing and validation to ensure that the hypoid gears perform as expected. This includes running the machinery under various load and operating conditions.
10. Integration and Field Application:
After successful testing, the machinery with hypoid gears is integrated into the specific application or industrial system. Engineers monitor the gears’ performance in real-world conditions to validate their long-term reliability and efficiency.
11. Maintenance and Service:
Regular maintenance and servicing are performed to ensure the continued smooth operation and longevity of the hypoid gears. Proper maintenance practices help prevent premature wear and extend the gears’ lifespan.
Throughout the implementation process, collaboration among mechanical engineers, design teams, manufacturing experts, and field operators is crucial to achieve optimal performance and long-lasting application of hypoid gears in modern machinery. This systematic approach ensures that the gears deliver the desired efficiency, durability, and reliability, meeting the requirements of the machinery and providing valuable solutions to various industrial applications.