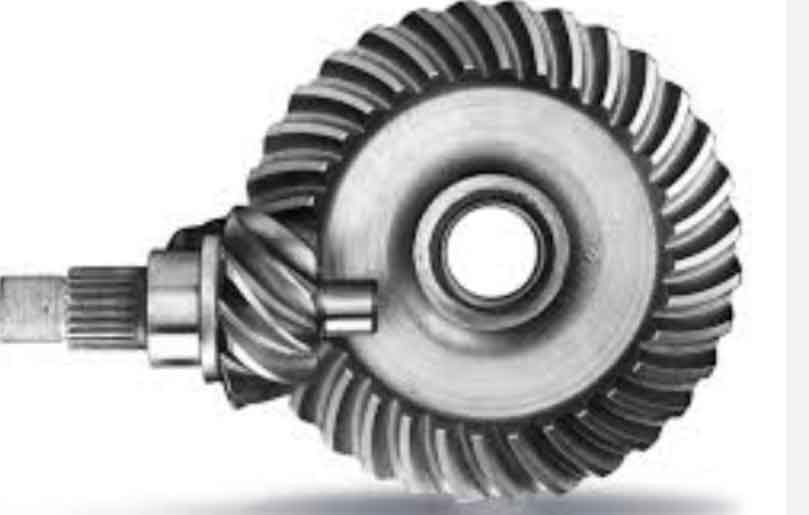
As with any field of engineering and technology, research and development in hypoid gear technology continue to progress, driving future advancements. Several areas of research hold promise for enhancing the performance, efficiency, and application range of hypoid gears. Here’s a look into some potential advancements in hypoid gear research:
1. Smart Gear Design and Optimization:
- Advancements in computational methods, such as artificial intelligence (AI) and machine learning, may lead to smarter gear design and optimization processes. AI algorithms could be used to automatically analyze gear performance data, identify design improvements, and optimize gear parameters for specific applications, leading to more efficient and tailored gear designs.
2. Nanostructured Materials and Coatings:
- Research into nanostructured materials and advanced coatings could lead to the development of hypoid gears with enhanced properties, such as increased hardness, reduced friction, and improved wear resistance. Nanostructured materials offer unique mechanical properties that can significantly improve gear performance.
3. Lightweight Gear Materials:
- Lightweight gear materials, such as advanced composites or high-strength alloys, could reduce the overall weight of hypoid gear systems. This would be particularly beneficial in applications where weight reduction is essential, such as in the automotive and aerospace industries.
4. Energy Efficiency and Noise Reduction:
- Research may focus on further reducing energy losses and noise in hypoid gear systems. This could involve the investigation of new tooth profiles, lubrication techniques, and surface treatments to minimize friction and vibration during gear operation.
5. Integrated Sensing and Condition Monitoring:
- Research could explore the integration of sensors within hypoid gear systems for real-time condition monitoring. By monitoring gear health, researchers could develop predictive maintenance strategies and prevent failures, leading to increased reliability and operational efficiency.
6. Advanced Manufacturing Techniques:
- Continued research into additive manufacturing (3D printing) methods for hypoid gears could result in faster prototyping, more complex gear geometries, and reduced material waste. Additionally, advancements in high-precision machining and grinding technologies may further improve gear manufacturing accuracy.
7. Adaptive Gear Technology:
- Research might focus on developing adaptive gear technology, where gear parameters can adjust or optimize during operation based on varying load conditions. This could lead to more versatile and efficient gear systems that adapt to changing requirements.
8. Sustainable and Green Gear Manufacturing:
- With a growing emphasis on sustainability, researchers may explore environmentally friendly manufacturing techniques for hypoid gears. This could include the use of eco-friendly lubricants, energy-efficient production methods, and recycling approaches for gear materials.
9. Hypoid Gear Tribology:
- Tribology, the study of friction, wear, and lubrication, could be further investigated for hypoid gears to understand and optimize the interaction between gear surfaces and lubricants. This research could lead to improved gear efficiency and durability.
These potential advancements in hypoid gear research hold promise for revolutionizing various industries that rely on efficient power transmission. As research continues to push the boundaries of gear technology, the future of hypoid gears looks bright, with innovations that address contemporary engineering challenges and contribute to a more sustainable and efficient future.