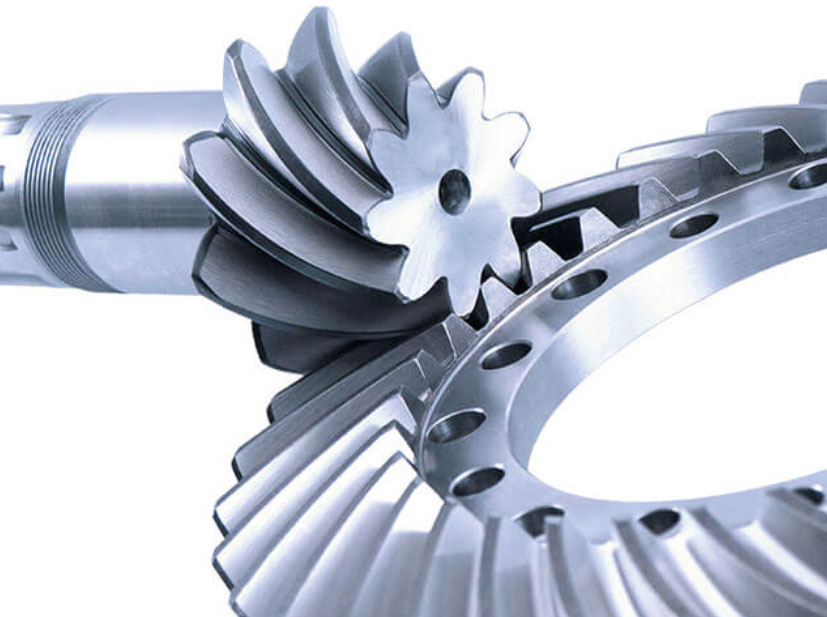
Customizing spiral bevel gears for specific industry requirements is a common practice to ensure that the gears meet the unique demands of various applications. Each industry may have different performance, size, material, and efficiency requirements, and customizing spiral bevel gears allows engineers to tailor the gears to match those specific needs. Here are the key steps and considerations involved in customizing spiral bevel gears for specific industry requirements:
1. Understanding Industry Needs:
- The first step in customization is to gain a comprehensive understanding of the industry’s requirements and the gear’s intended application. This includes identifying the required torque, speed, size, operating environment, noise constraints, and other relevant factors.
2. Gear Design and Geometry:
- Based on the industry requirements, the gear’s design and geometry are tailored to optimize its performance. The gear ratio, number of teeth, helix angle, and tooth form may be adjusted to suit the specific application.
3. Material Selection:
- The choice of gear material is critical, as different industries may require specific properties, such as high strength, wear resistance, corrosion resistance, or heat resistance. Customizing the gear material ensures it can withstand the operating conditions and loads encountered in the industry.
4. Manufacturing Method:
- Customizing spiral bevel gears often involves selecting the most appropriate manufacturing method. Advanced CNC gear cutting and grinding methods are commonly used for precise customization to meet tight tolerances and gear accuracy.
5. Heat Treatment:
- Heat treatment processes, such as carburizing and quenching, may be customized to achieve the desired gear hardness and durability.
6. Noise Reduction and Vibration Damping:
- Industries with noise and vibration constraints, such as aerospace or marine applications, may require specific tooth profile modifications or damping features to reduce noise and vibrations.
7. Gear Coatings and Surface Treatments:
- Customized gear coatings or surface treatments may be applied to enhance gear performance, such as reducing friction, improving wear resistance, or providing corrosion protection.
8. Quality Control and Testing:
- Rigorous quality control measures and testing protocols are implemented to ensure that the customized gears meet the industry’s standards and specifications.
9. Compliance and Certification:
- Industries with specific regulatory requirements, such as aerospace or medical industries, may require the gears to comply with specific standards and undergo certification processes.
10. Collaboration with Gear Manufacturers:
- Working closely with experienced gear manufacturers is crucial for successful customization. Their expertise and knowledge of gear design, manufacturing processes, and industry-specific requirements can help ensure the gears’ optimal performance.
Customizing spiral bevel gears for specific industry requirements allows for the creation of tailored solutions that can significantly improve efficiency, reliability, and performance in various applications. By considering the industry’s unique needs and collaborating with skilled gear manufacturers, engineers can develop customized spiral bevel gears that deliver superior performance and meet the demands of specific industries.