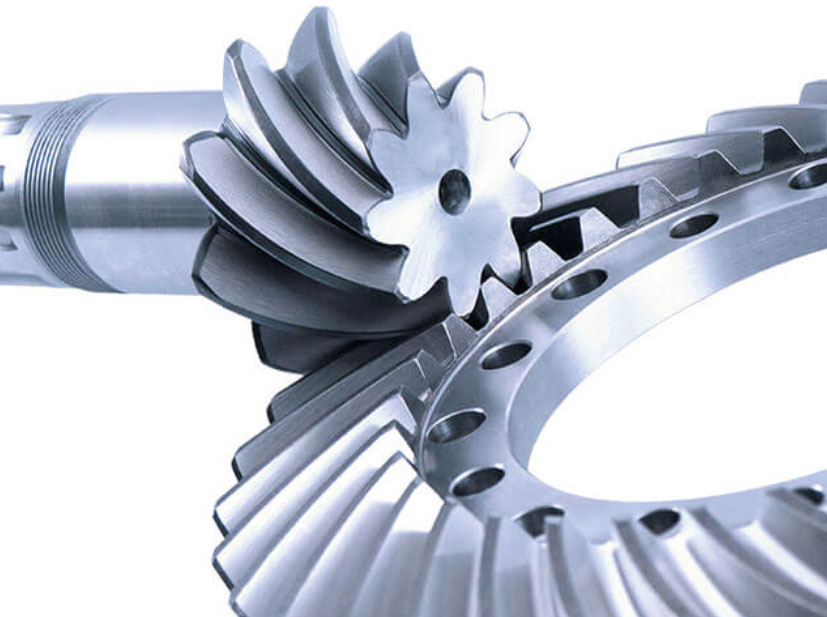
Heat treatment and material selection are critical aspects in the manufacturing of high-performance spiral bevel gears. These processes play a significant role in determining the gears’ mechanical properties, wear resistance, and durability, all of which are crucial for their optimal performance in demanding applications. Here’s a closer look at heat treatment and material selection for high-performance spiral bevel gears:
Heat Treatment for Spiral Bevel Gears:
Heat treatment involves controlled heating and cooling processes applied to the gears to achieve specific material properties. The most common heat treatment processes for spiral bevel gears include:
1. Carburizing:
- Carburizing is a surface-hardening process where the gear is heated in a carbon-rich atmosphere to diffuse carbon into the gear’s surface. This increases the surface hardness, wear resistance, and fatigue strength while maintaining a tough core to handle heavy loads.
2. Quenching:
- Quenching is a rapid cooling process that follows carburizing to lock in the hardened surface layer. This creates a hardness gradient, with the core remaining relatively softer than the surface. The hardness and wear resistance achieved through quenching further enhance the gear’s performance.
3. Tempering:
- Tempering is a heat treatment process applied after quenching to reduce the brittleness caused by the rapid cooling. It helps achieve a balance between hardness and toughness, providing the gear with the necessary strength to withstand dynamic loads.
Material Selection for Spiral Bevel Gears:
Material selection is equally important for high-performance spiral bevel gears. The choice of material should consider the specific requirements of the gear’s application, including load, speed, temperature, and corrosive environment. Common materials used for high-performance spiral bevel gears include:
1. AISI 8620 and 9310 Alloy Steels:
- These alloy steels are popular choices for spiral bevel gears due to their excellent combination of strength, toughness, and wear resistance. They are often used for gears subjected to high loads and impact.
2. AISI 4340 Alloy Steel:
- AISI 4340 offers high strength, toughness, and fatigue resistance, making it suitable for gears operating under heavy loads and in harsh environments.
3. AISI 9310 Ni-Cr-Mo Alloy Steel:
- AISI 9310 provides superior hardenability and impact resistance, making it suitable for high-performance gears with stringent toughness requirements.
4. Austenitic Stainless Steels:
- Austenitic stainless steels offer good corrosion resistance, making them suitable for gears in marine and corrosive environments.
5. Powder Metallurgy Steels:
- Powder metallurgy steels offer controlled alloy compositions and high-density, resulting in uniform properties and reduced risk of inclusions. They are used in gears where high precision and consistency are critical.
It is essential to consider both the heat treatment processes and material selection in combination to achieve the desired properties for high-performance spiral bevel gears. Proper heat treatment enhances the material’s mechanical properties, while selecting the right material ensures the gear can withstand the specific operating conditions and loads, leading to high-performance and reliable gear solutions.