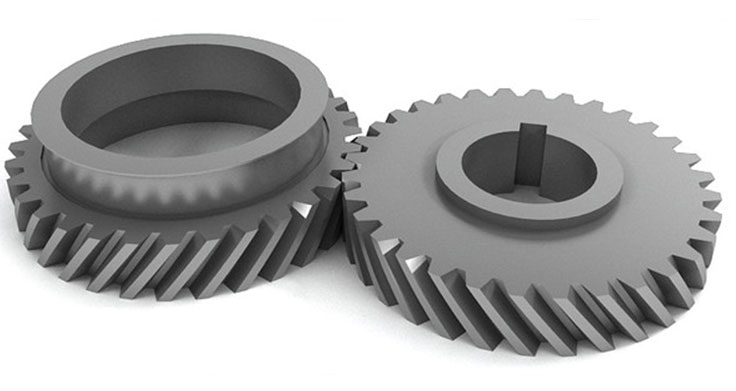
Helical gears are known for their ability to provide quiet power transmission compared to other types of gears, such as spur gears. This is mainly attributed to their unique design and tooth engagement characteristics, which help in reducing noise and vibration. Here’s how helical gears achieve quiet power transmission:
1. Helical Tooth Engagement:
- Helical gears have inclined teeth that are cut at an angle to the gear axis, forming a helix shape. When the helical gears rotate and mesh, the helical teeth come into contact gradually, rather than suddenly as in straight-cut spur gears. This gradual engagement reduces the impact and shock loads on the gear teeth, leading to lower noise levels during gear meshing.
2. Smoother Tooth Contact:
- The helical shape of the gear teeth provides a larger contact area during meshing, distributing the load across more teeth simultaneously. This results in smoother tooth contact and reduced tooth deflection, which contributes to quieter operation.
3. Load Distribution:
- Helical gears distribute the transmitted load across multiple teeth, resulting in reduced pressure and stress on individual teeth. This load distribution helps in minimizing gear wear and tooth deformation, contributing to lower noise levels over time.
4. Reduced Backlash:
- The inclined tooth design of helical gears reduces backlash compared to spur gears. Backlash is the play or lost motion between gear teeth when direction changes occur. Lower backlash results in smoother gear operation and reduces noise and vibration during gear reversals.
5. Misalignment Compensation:
- Helical gears can tolerate a certain degree of misalignment between shafts due to their helix angle. This ability to accommodate misalignment helps in reducing noise and wear that may occur in cases of slight shaft misalignments.
6. Contact Ratio:
- Helical gears have a higher tooth contact ratio compared to spur gears, which means more teeth are in contact at any given moment during rotation. This higher contact ratio helps in distributing the load evenly, reducing localized stress concentration and vibration.
7. Lubrication:
- Proper lubrication of helical gears is essential for reducing friction and wear, which can contribute to noise generation. Adequate lubrication forms a thin film between the gear teeth, reducing metal-to-metal contact and minimizing noise.
8. Gear Pairing:
- Helical gears are often used in pairs with opposite helix directions to balance axial thrust. This pairing helps in maintaining gear alignment, preventing excessive axial loads, and minimizing noise caused by axial forces.
The gradual tooth engagement, smoother tooth contact, load distribution, and reduced backlash in helical gears contribute to quieter power transmission. These characteristics make helical gears particularly suitable for applications that require low noise levels and smooth gear operation, such as in automotive transmissions, industrial machinery, and other precision mechanical systems.