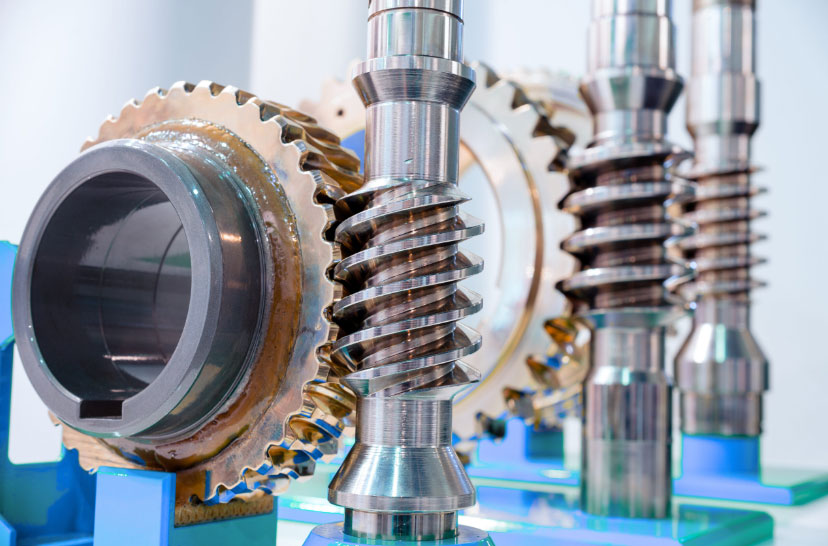
Custom worm gears play an important role in electric vehicles (EVs) by providing precise motion control and efficient power transmission. However, EVs present unique challenges that require tailored solutions in worm gear design. Here are some of the key challenges and considerations when using custom worm gears in electric vehicles:
1. Efficiency and Range Optimization:
EVs require high efficiency in power transmission to maximize their range and battery life. Custom worm gears need to be designed with low friction, minimal backlash, and precise tooth engagement to reduce energy losses during gear meshing.
2. Weight and Space Constraints:
Weight and space are critical considerations in EV design. Custom worm gears should be lightweight and compact to minimize overall vehicle weight and allow for more efficient use of space.
3. High Torque Transmission:
Electric vehicles demand high torque transmission from the electric motor to the wheels. Custom worm gears must be capable of handling the required torque while maintaining efficiency and precision.
4. Noise and Vibration Reduction:
EVs are expected to operate quietly and smoothly. Custom worm gears with low noise and vibration characteristics are essential to enhance passenger comfort and reduce noise pollution.
5. Temperature and Lubrication:
EVs generate heat during operation, and the gear system must withstand elevated temperatures. Custom worm gears should be designed with suitable materials and lubrication systems to handle the thermal challenges.
6. Regenerative Braking:
Custom worm gears can be designed to support regenerative braking systems, where the motor acts as a generator to recover energy during braking. The gear system must facilitate smooth transitions between power delivery and energy recovery.
7. Durability and Longevity:
EVs are expected to have a long operational life. Custom worm gears should undergo rigorous testing and be made from durable materials to ensure reliability and longevity in the demanding automotive environment.
8. Manufacturing Precision:
Custom worm gears for EVs require high manufacturing precision to achieve low backlash and smooth tooth engagement, crucial for accurate motion control and efficient power transmission.
9. Gear Materials:
The choice of materials is critical in achieving the desired balance between strength, weight, and durability. Advanced materials, such as composites or alloys, can be considered to meet specific performance requirements.
10. Integration with Electric Drivetrains:
Custom worm gears must be seamlessly integrated into the overall electric drivetrain, taking into account the motor, gearbox, and other components to optimize system performance.
Addressing these challenges and considerations allows engineers to design custom worm gears that meet the unique requirements of electric vehicles. By providing precise motion control, high efficiency, and reliable power transmission, custom worm gears contribute to the overall performance and sustainability of electric vehicles, promoting their widespread adoption in the automotive industry.