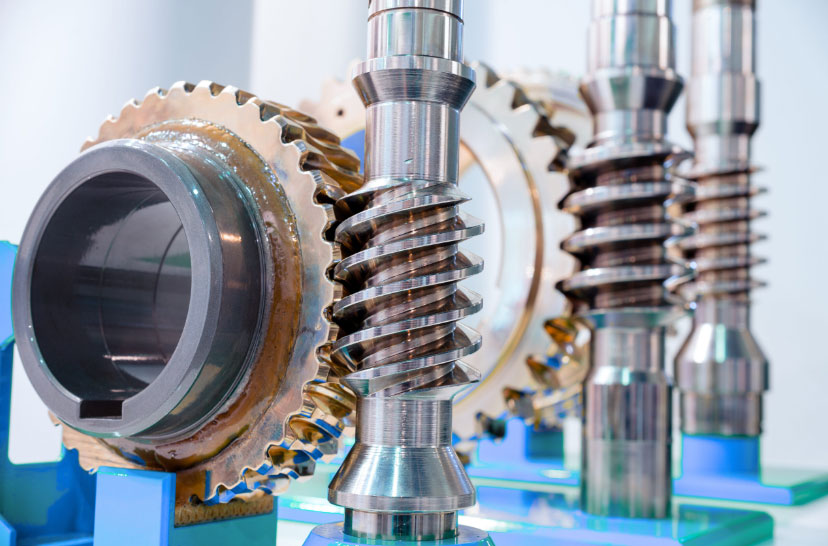
Proper lubrication is essential for ensuring the longevity and efficiency of custom worm gears. Lubrication reduces friction, wear, and heat generation, thereby extending the gear’s lifespan and improving overall system efficiency. Here are some best practices for custom worm gear lubrication to maximize longevity and efficiency:
1. Lubricant Selection:
Choose the right lubricant based on the gear’s material, operating conditions, and load capacity. Synthetic lubricants are commonly used for their high film strength and resistance to breakdown under high temperatures.
2. Viscosity Grade:
Select the appropriate viscosity grade of the lubricant to ensure it flows smoothly and creates a sufficient lubricating film between the gear teeth. Too high or too low viscosity can negatively impact gear performance.
3. Regular Lubrication Checks:
Regularly inspect and replenish the lubricant to maintain the proper lubrication levels. Check for any signs of contamination, degradation, or leakage that may affect gear performance.
4. Lubrication Intervals:
Establish a lubrication schedule based on the gear’s operating conditions and manufacturer’s recommendations. Some gears may require more frequent lubrication in demanding applications.
5. Lubrication Method:
Consider the best lubrication method for the gear system. Drip lubrication, oil bath, or forced lubrication systems may be used based on the gear’s size, speed, and operating environment.
6. Lubricant Contamination Control:
Implement measures to prevent lubricant contamination by dirt, debris, or water. Proper sealing and filtering systems can help maintain the lubricant’s cleanliness.
7. Temperature Considerations:
Take into account the operating temperature range when selecting the lubricant. Some gears may operate at higher temperatures, requiring lubricants with excellent thermal stability.
8. Pre-Running Lubrication:
Before running the gear under full load, consider applying a pre-running lubrication cycle to ensure uniform distribution of the lubricant on all gear surfaces.
9. Consistent Lubricant Type:
Avoid mixing different types of lubricants unless recommended by the manufacturer. Mixing lubricants may result in reduced performance and gear wear.
10. Monitoring and Condition-Based Maintenance:
Implement monitoring systems to assess the lubricant’s condition and gear performance. Condition-based maintenance can help identify potential issues before they escalate.
11. Training and Maintenance Procedures:
Ensure personnel involved in gear maintenance are well-trained in lubrication best practices and adhere to proper maintenance procedures.
12. Environmental Considerations:
Take into account any environmental regulations or considerations when selecting lubricants, especially for applications that may involve exposure to water or other contaminants.
By following these best practices for custom worm gear lubrication, you can extend the gear’s lifespan, improve overall system efficiency, and reduce the risk of gear failure. Proper lubrication is crucial in ensuring the reliable and efficient performance of custom worm gears, especially in critical applications where precision motion control is essential.