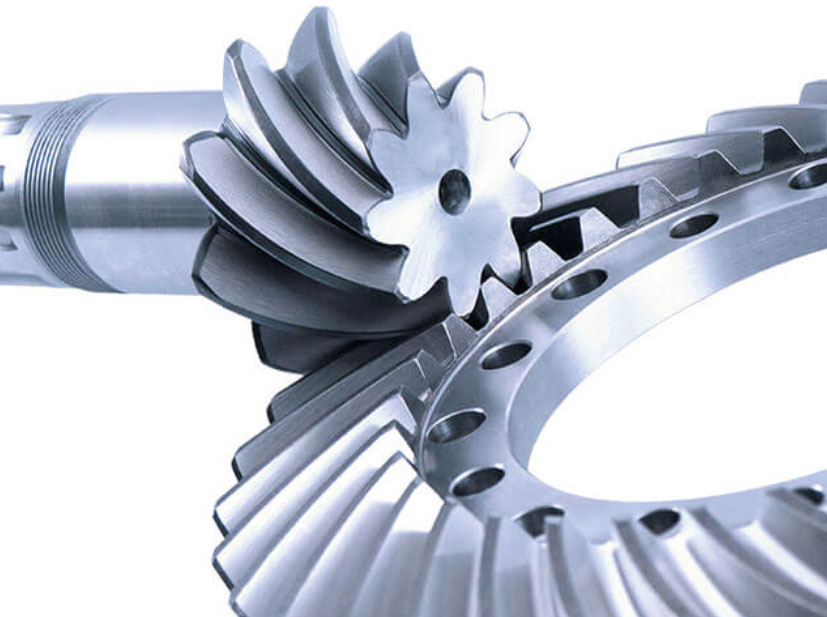
Addressing thermal effects in spiral bevel gear systems is crucial to ensure the gears’ reliable performance and prevent premature failure due to thermal-induced stresses. Thermal effects can arise from various factors, such as power transmission, friction, and ambient temperature changes. Here are some strategies to address thermal effects in spiral bevel gear systems:
1. Material Selection:
- Choose materials with good thermal conductivity and low coefficient of thermal expansion for the gear components.
- Materials with these properties can dissipate heat more effectively and minimize the risk of thermal distortions.
2. Heat Treatment:
- Implement appropriate heat treatment processes to enhance the gear’s material properties, such as hardness and toughness.
- Proper heat treatment can help the gear withstand thermal stresses during operation.
3. Lubrication and Cooling:
- Use high-quality lubricants that can withstand high temperatures and provide effective cooling to the gears.
- Proper lubrication and cooling help dissipate heat generated during gear operation.
4. Surface Treatments:
- Apply surface treatments, such as shot peening or nitriding, to increase the gear’s surface hardness and resistance to thermal wear.
- Surface treatments can also improve the gear’s ability to handle temperature fluctuations.
5. Thermal Analysis and Simulation:
- Conduct thermal analysis and simulation to understand how temperature changes affect the gear system.
- This analysis helps identify potential hotspots and areas susceptible to thermal stresses.
6. Proper Gear Design:
- Optimize gear design, considering factors such as thermal expansion, to ensure that the gear maintains proper meshing and contact during temperature variations.
- Carefully consider the gear’s tolerance for thermal growth to prevent excessive clearances and backlash changes.
7. Thermal Insulation:
- Use thermal insulation measures to minimize heat transfer from adjacent components or external sources.
- Thermal insulation helps maintain a more stable operating temperature for the gear system.
8. Material Coefficients:
- Consider the coefficient of thermal expansion for all gear components to ensure compatible expansion rates and prevent excessive interference.
9. Cooling Systems:
- Implement cooling systems, such as cooling fins or oil circulation, in gearboxes to dissipate heat more effectively.
- Efficient cooling helps stabilize the gear’s operating temperature.
10. Monitoring and Maintenance:
- Regularly monitor gear temperatures and performance to detect any abnormal thermal effects.
- Implement a proactive maintenance strategy to address potential thermal-related issues before they escalate.
Addressing thermal effects in spiral bevel gear systems requires a holistic approach that considers material properties, gear design, lubrication, cooling, and thermal analysis. By adopting appropriate measures, engineers can ensure the gears’ smooth and reliable operation, even in environments with varying temperatures and thermal stresses.