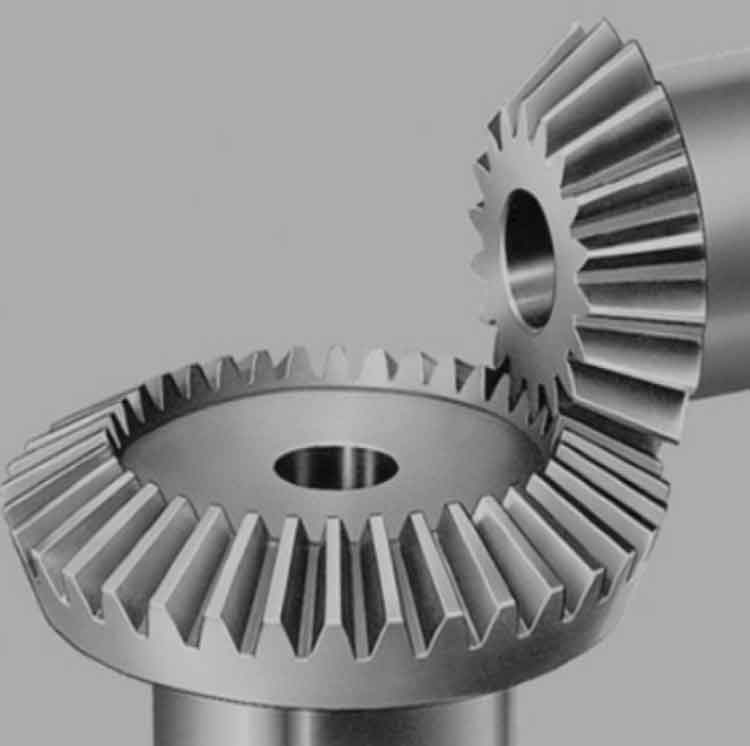
Maintaining straight bevel gears can be challenging due to the demanding operating conditions they are exposed to and the critical role they play in various applications. Addressing these challenges effectively is essential to ensure the gears’ longevity and optimal performance. Here are some common challenges in straight bevel gear maintenance and potential solutions:
1. Lubrication and Contamination Control:
- Challenge: Ensuring proper lubrication and preventing lubricant contamination are critical for gear health.
- Solution: Implement a proactive lubrication management program with regular inspections, lubricant analysis, and proper filtration to maintain optimal lubrication and reduce the risk of wear and gear damage.
2. Tooth Wear and Damage:
- Challenge: Over time, gears may experience tooth wear, pitting, and fatigue, particularly in high-load applications.
- Solution: Regularly inspect gears for signs of wear and damage. Addressing minor issues early can prevent more severe damage and the need for costly repairs. Replacing worn gears with properly manufactured replacements is essential.
3. Misalignment and Tooth Meshing Issues:
- Challenge: Misalignment can lead to uneven tooth meshing and increased gear stress.
- Solution: Conduct regular gear alignment checks and ensure proper setup during assembly or maintenance. Proper alignment reduces wear and noise while increasing gear efficiency.
4. Gear Noise and Vibration:
- Challenge: Gear noise and vibration can indicate issues such as misalignment, inadequate lubrication, or tooth damage.
- Solution: Identify and address the root cause of gear noise and vibration. This may involve realigning gears, adjusting gear mesh settings, or addressing lubrication issues.
5. Inspection Accessibility:
- Challenge: Some gear systems may be challenging to access for inspection and maintenance.
- Solution: Design gear systems with maintenance in mind. Provide adequate access points and consider modular designs that facilitate easier disassembly and reassembly.
6. Gearbox Sealing and Environmental Protection:
- Challenge: Gearboxes in harsh environments may face challenges related to sealing and protection from contaminants.
- Solution: Use appropriate seals and gaskets to prevent dust, dirt, and moisture from entering the gearbox. Regularly inspect and replace seals as needed.
7. Gear Tooth Profile Accuracy:
- Challenge: Gears with inaccuracies in tooth profile may suffer from poor meshing and increased wear.
- Solution: Employ high-precision manufacturing processes and perform periodic inspections to ensure proper tooth profile accuracy.
8. Periodic Gear Overhaul:
- Challenge: Planning and executing a gear overhaul can be complex and time-consuming.
- Solution: Establish a regular maintenance schedule, including planned overhauls, to address wear and extend gear life. Careful planning and scheduling help minimize downtime and prevent unexpected breakdowns.
9. Gear Material and Heat Treatment Considerations:
- Challenge: Choosing the right gear material and heat treatment processes is crucial for gear durability.
- Solution: Work with experienced gear manufacturers to select the appropriate materials and heat treatment processes based on the application’s load and operating conditions.
Addressing these challenges requires a comprehensive maintenance approach that includes regular inspections, timely repairs, proper lubrication, and effective gear alignment. By implementing proactive maintenance practices and promptly addressing any issues, straight bevel gears can perform optimally and have an extended service life, reducing downtime and overall maintenance costs.