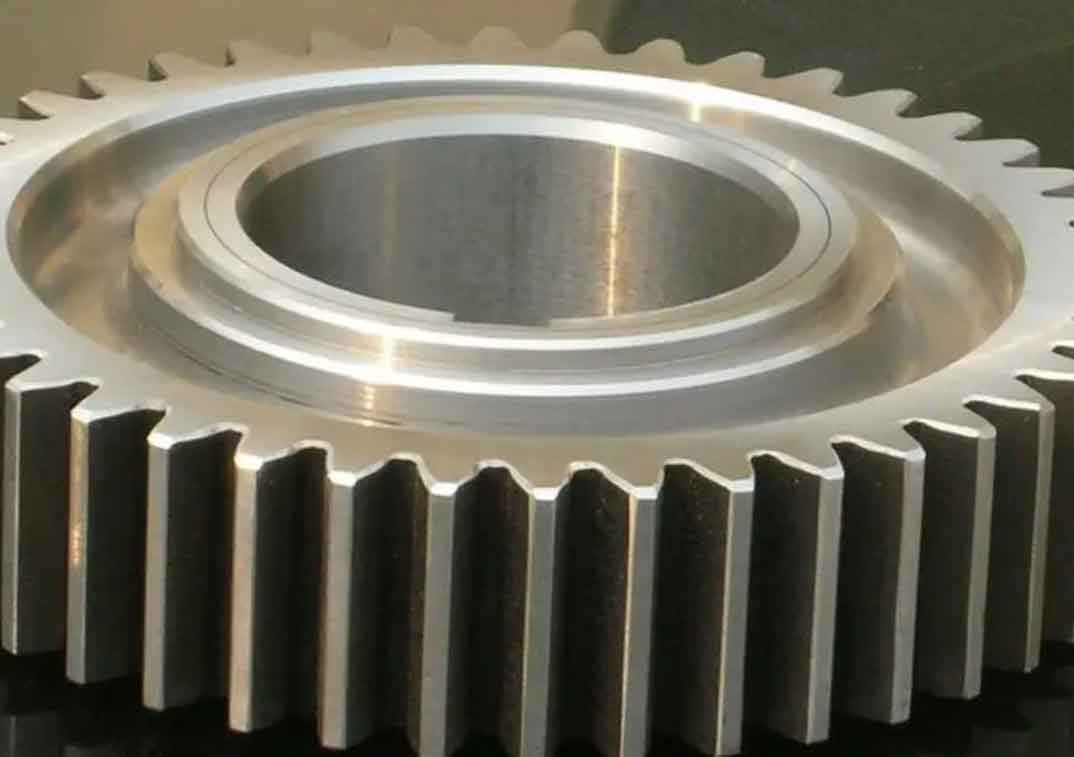
Optimizing spur gear performance in high-torque applications involves addressing several critical aspects of gear design, material selection, and operational management to ensure durability, efficiency, and longevity. Here’s a detailed look at strategies and considerations for achieving this:
1. Material Selection
- High-Performance Alloys: For high-torque applications, selecting the right material is crucial. High-strength steel alloys like AISI 4340 or AISI 8620, which can be heat-treated for additional strength and wear resistance, are commonly used. These materials withstand the stresses and strains in high-torque environments better than standard steels.
- Advanced Treatments: Use surface hardening treatments like carburizing, nitriding, or induction hardening to enhance surface strength and fatigue life without compromising the toughness of spur gear core.
2. Gear Geometry Optimization
- Tooth Profile Modifications: Customize the involute tooth profile to distribute the load more evenly across the tooth face. Modifications like profile shifting (adding or subtracting material from the standard involute profile) can increase the root thickness, reducing stress concentrations and the risk of tooth breakage.
- Increased Face Width: Wider spur gear faces distribute loads over a larger surface area, reducing the pressure per unit area and minimizing wear.
- Addendum and Dedendum Adjustments: Adjusting these parameters can optimize the tooth height to ensure better engagement and load distribution, enhancing spur gear’s ability to handle high torque.
3. Advanced Manufacturing Techniques
- Precision Machining: Utilize high-precision CNC machining to ensure that spur gears meet exact specifications, which is vital for maintaining the alignment and engagement necessary for high-torque applications.
- Gear Grinding: Finish spur gears with grinding instead of cutting to achieve a smoother and more accurate tooth surface. This reduces friction, heat build-up, and wear under high-torque conditions.
4. Lubrication Systems
- Enhanced Lubrication: High-torque spur gears require robust lubrication to reduce friction and wear. Use high-viscosity oils or extreme pressure (EP) additives to form a protective film that can withstand the high contact stresses.
- Cooling Measures: Implement active cooling systems, such as oil circulation systems that not only lubricate but also remove excess heat from spur gear surfaces.
5. Dynamic Load Analysis and Testing
- Finite Element Analysis (FEA): Use FEA to simulate gear performance under actual operating conditions. This analysis helps in predicting how spur gear will behave under high torque and identifying potential failure points.
- Prototyping and Testing: Manufacture prototype gears and subject them to controlled testing conditions to validate the design and material choices. Adjustments can be made based on test results before final production.
6. Monitoring and Maintenance
- Condition Monitoring: Implement sensors to monitor spur gear temperature, vibration, and noise, indicators of wear or impending failure. This real-time data helps in scheduling maintenance before catastrophic failures occur.
- Regular Inspections: Conduct periodic inspections and replace spur gear or components that show signs of excessive wear or damage to prevent unexpected downtimes.
7. Application-Specific Customizations
- Composite Materials: In some high-torque applications, especially where weight is a concern, composite materials like carbon fiber-reinforced polymers may be used for spur gear. These materials offer high strength-to-weight ratios and good fatigue resistance.
- Hybrid Designs: Consider using hybrid gears that combine different materials, such as a steel core with a wear-resistant coating, to optimize performance and durability.
By carefully considering these factors, engineers can significantly enhance the performance of spur gears in high-torque applications. The key is to balance the design, material properties, and operational conditions to meet the specific demands of the application while ensuring reliability and efficiency.