Material science plays a pivotal role in the evolution of hypoid gear manufacturing, significantly impacting the performance, durability, and efficiency of these critical components. Hypoid gear, with their unique geometry and high-contact stresses, demand advanced materials and manufacturing techniques to meet the stringent requirements of modern applications. This article delves into the advancements in material science that have revolutionized hypoid gear manufacturing.
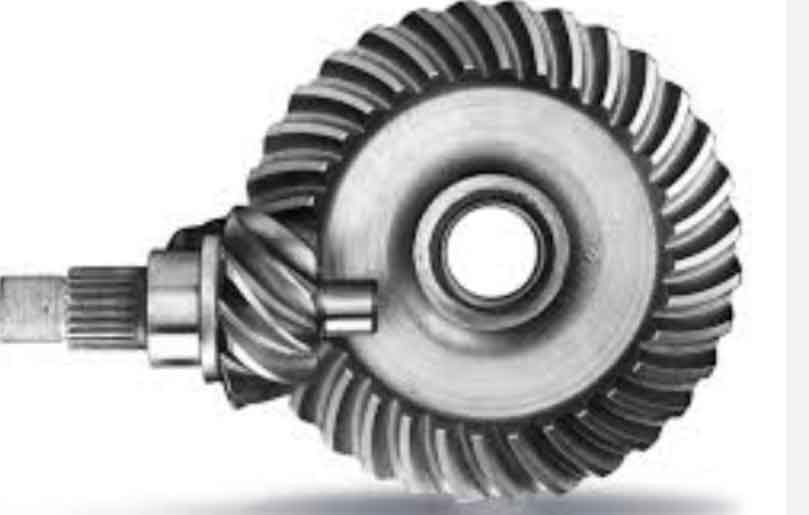
Introduction
Hypoid gear is extensively used in automotive differentials, industrial machinery, and aerospace applications due to their ability to handle high torque and provide smooth transmission of power. The evolution of hypoid gear manufacturing has been driven by the need for enhanced performance, reduced wear, and increased reliability. Material science has been at the forefront of this evolution, enabling the development of new materials, coatings, and manufacturing processes.
Key Material Innovations in Hypoid Gear Manufacturing
- High-Strength Steels:
- Advanced high-strength steels (AHSS) and ultra-high-strength steels (UHSS) offer superior mechanical properties, including high tensile strength and toughness.
- These materials allow for the manufacturing of lighter and more compact hypoid gear without compromising performance.
- Case-Hardening Steels:
- Steels such as 18CrNiMo7-6 and 20MnCr5 are commonly used for hypoid gear due to their excellent hardenability and wear resistance.
- Case hardening techniques, such as carburizing and nitriding, enhance surface hardness while maintaining a tough core.
- Composite Materials:
- The use of composite materials, such as carbon-fiber-reinforced polymers (CFRPs), is emerging in hypoid gear manufacturing.
- These materials provide high strength-to-weight ratios and exceptional fatigue resistance.
- Advanced Coatings:
- Coatings like diamond-like carbon (DLC) and tungsten carbide (WC) are applied to hypoid gear surfaces to reduce friction and wear.
- These coatings significantly extend the service life of hypoid gear in demanding applications.
Manufacturing Techniques Enhanced by Material Science
1. Additive Manufacturing (3D Printing)
Additive manufacturing allows for the production of complex hypoid gear geometries with high precision. Using metal powders and advanced polymers, 3D printing can create hypoid gear with optimized internal structures, reducing weight and improving performance.
2. Powder Metallurgy
Powder metallurgy involves the consolidation of metal powders into a solid form through pressing and sintering. This technique enables the production of hypoid gear with fine microstructures and uniform material properties, enhancing strength and wear resistance.
3. Surface Engineering
Surface engineering techniques, such as laser surface treatment and ion implantation, improve the surface properties of hypoid gear. These methods enhance hardness, reduce friction, and increase resistance to wear and corrosion.
Comparative Analysis of Materials for Hypoid Gear
Material Type | Advantages | Disadvantages |
---|---|---|
High-Strength Steels | High tensile strength, durability | Higher cost, complex processing |
Case-Hardening Steels | Excellent wear resistance, tough core | Requires precise heat treatment |
Composite Materials | Lightweight, high fatigue resistance | Higher material cost, limited applications |
Advanced Coatings | Reduced friction, extended service life | Additional manufacturing step, cost |
List of Critical Factors in Material Selection
- Load-Bearing Capacity: Ability to withstand high stresses and loads.
- Wear Resistance: Resistance to abrasion and surface degradation.
- Thermal Stability: Performance at elevated temperatures without degradation.
- Corrosion Resistance: Ability to resist chemical attack and oxidation.
- Manufacturability: Ease of processing and forming into complex shapes.
Future Directions in Hypoid Gear Material Science
- Nanomaterials:
- The incorporation of nanomaterials can lead to hypoid gear with superior strength and reduced weight.
- Research is ongoing into nanocomposites and nanocoatings for hypoid gear.
- Smart Materials:
- Smart materials that can adapt to changing operational conditions are being explored.
- These materials can potentially alter their properties in response to load, temperature, and other factors.
- Sustainable Materials:
- The focus on sustainability is driving the development of eco-friendly materials.
- Bio-based polymers and recyclable composites are gaining traction in hypoid gear manufacturing.
Conclusion
The evolution of hypoid gear manufacturing is intrinsically linked to advancements in material science. High-strength steels, composite materials, advanced coatings, and innovative manufacturing techniques have collectively enhanced the performance and reliability of hypoid gear. As research continues, the integration of nanomaterials, smart materials, and sustainable options will further revolutionize the field, ensuring that hypoid gear remain at the forefront of mechanical transmission technology.