Spur gear is fundamental components in various mechanical systems, including automotive, aerospace, and industrial machinery. The performance and longevity of these spur gear is significantly influenced by the materials from which they are made. Recent advancements in material science have led to the development of new materials and treatments that enhance the durability and performance of spur gear. This article delves into these advancements, highlighting their impact on gear technology.
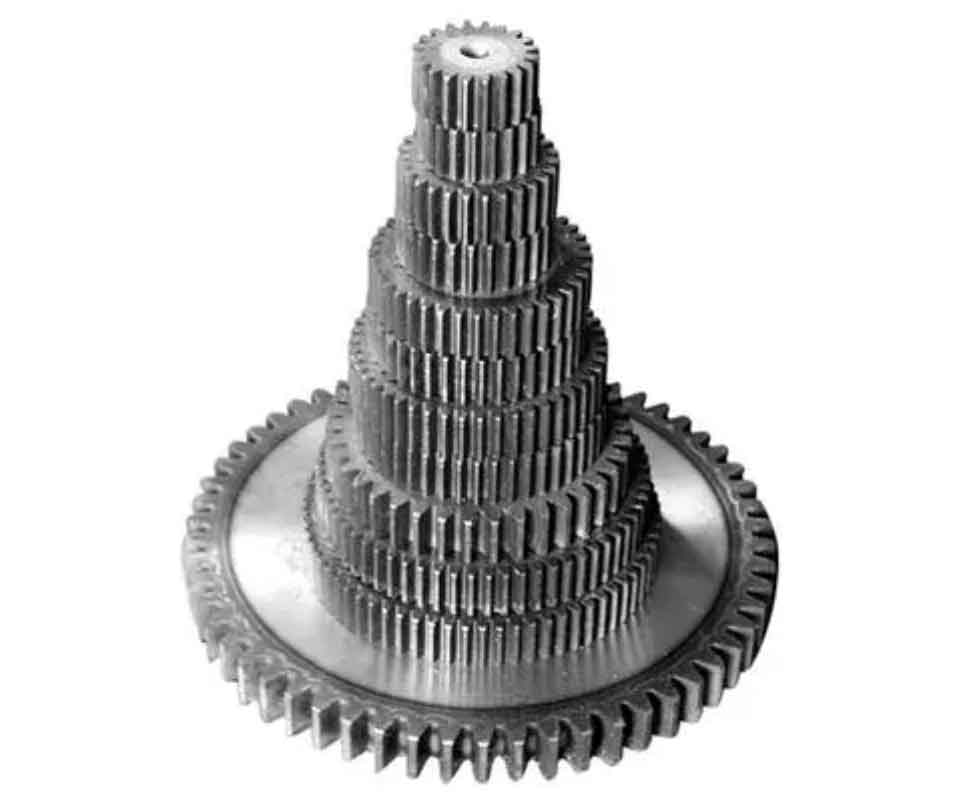
1. Introduction
Spur gear, with their straight teeth and parallel axis, are widely used for their simplicity and efficiency in transmitting power. The need for spur gear that can withstand higher loads, operate under more extreme conditions, and have longer lifespans has driven significant research and development in material science. This article explores these advancements and their applications in enhancing spur gear durability and performance.
2. Advanced Materials for Spur Gear
2.1 High-Strength Alloy Steels
Alloy steels have been the backbone of spur gear manufacturing due to their excellent mechanical properties. Recent developments in high-strength alloy steels have focused on improving their fatigue resistance, hardness, and wear resistance. These steels are often subjected to heat treatments such as carburizing, nitriding, and induction hardening to enhance their surface properties.
Benefits of High-Strength Alloy Steels:
- Increased fatigue strength
- Enhanced surface hardness
- Improved wear resistance
2.2 Powder Metallurgy (PM) Materials
Powder metallurgy involves the compaction of metal powders followed by sintering to form solid components. Advances in PM technology have led to the development of materials with superior properties tailored for specific applications. PM materials can be engineered to have high density, uniform microstructure, and excellent mechanical properties.
Advantages of Powder Metallurgy Materials:
- Uniform material properties
- High material utilization
- Ability to produce complex shapes
2.3 Advanced Composites
Composite materials, made from two or more constituent materials with significantly different physical or chemical properties, offer a balance of high strength and low weight. Recent advancements in fiber-reinforced composites have shown promise for spur gear applications, particularly in reducing weight while maintaining or enhancing strength.
Key Features of Advanced Composites:
- High strength-to-weight ratio
- Excellent fatigue resistance
- Customizable properties
2.4 Nanomaterials
Nanomaterials, characterized by their ultra-fine grain size, exhibit unique mechanical properties that make them suitable for high-performance gear applications. The incorporation of nanoparticles into spur gear materials can enhance hardness, wear resistance, and thermal stability.
Benefits of Nanomaterials:
- Enhanced mechanical properties
- Improved thermal stability
- Superior wear resistance
3. Surface Treatments and Coatings
3.1 Diamond-Like Carbon (DLC) Coatings
DLC coatings are applied to spur gear surfaces to reduce friction, wear, and corrosion. These coatings have a high hardness and low coefficient of friction, which significantly improves spur gear performance and longevity.
Advantages of DLC Coatings:
- Reduced friction
- Enhanced wear resistance
- Improved corrosion resistance
3.2 Shot Peening
Shot peening is a surface treatment process that involves bombarding spur gear surface with small spherical media. This process induces compressive stresses on the surface, which enhance fatigue resistance and reduce the likelihood of crack initiation.
Benefits of Shot Peening:
- Increased fatigue strength
- Improved resistance to crack initiation
- Enhanced surface hardness
3.3 Laser Surface Hardening
Laser surface hardening is a technique that uses laser beams to heat spur gear surface rapidly. This process results in a hardened surface layer with improved wear resistance and fatigue strength, without affecting the core properties of spur gear.
Key Features of Laser Surface Hardening:
- Precise control over hardened layer depth
- Minimal distortion
- Enhanced wear resistance
4. Comparative Analysis of Materials and Treatments
Material/Treatment | Hardness | Fatigue Strength | Wear Resistance | Weight | Cost Efficiency |
---|---|---|---|---|---|
High-Strength Alloy Steels | High | High | High | High | Moderate |
Powder Metallurgy Materials | Medium | High | High | Medium | High |
Advanced Composites | Medium | Medium | Medium | Low | High |
Nanomaterials | Very High | Very High | Very High | Low | High |
DLC Coatings | Very High | High | Very High | N/A | High |
Shot Peening | N/A | Very High | High | N/A | Moderate |
Laser Surface Hardening | High | High | High | N/A | Moderate |
5. Future Trends
The future of spur gear materials and treatments is poised for exciting developments, driven by the need for higher performance and sustainability. Key trends include:
- Smart Materials: Development of materials that can adapt to changing operating conditions, such as self-lubricating materials.
- Green Manufacturing: Emphasis on environmentally friendly manufacturing processes and materials, including biodegradable composites and coatings.
- Additive Manufacturing: Advancements in 3D printing of advanced materials for creating high-performance gear components with complex geometries.
6. Conclusion
Advancements in material science have significantly contributed to the enhancement of spur gear durability and performance. High-strength alloy steels, powder metallurgy materials, advanced composites, and nanomaterials each offer unique benefits that can be tailored to specific applications. Additionally, surface treatments and coatings such as DLC, shot peening, and laser surface hardening further enhance gear performance. As technology continues to evolve, these advancements will play a crucial role in the development of more efficient, durable, and high-performing spur gear for various applications.