Introduction
Helical gears are integral components in many high-stress applications, including electric vehicles, industrial machinery, and aerospace systems. The performance and longevity of these gears are often challenged by the harsh conditions they operate under. Understanding the wear mechanisms of helical gears in high-stress environments is crucial for improving their design, maintenance, and overall performance. This article explores the various wear mechanisms that affect helical gears and discusses strategies to mitigate wear in demanding applications.
Understanding Helical Gears
Helical gears are characterized by teeth that are cut at an angle to the axis of rotation. This design allows for smoother and quieter operation compared to spur gears due to the gradual engagement of the teeth.
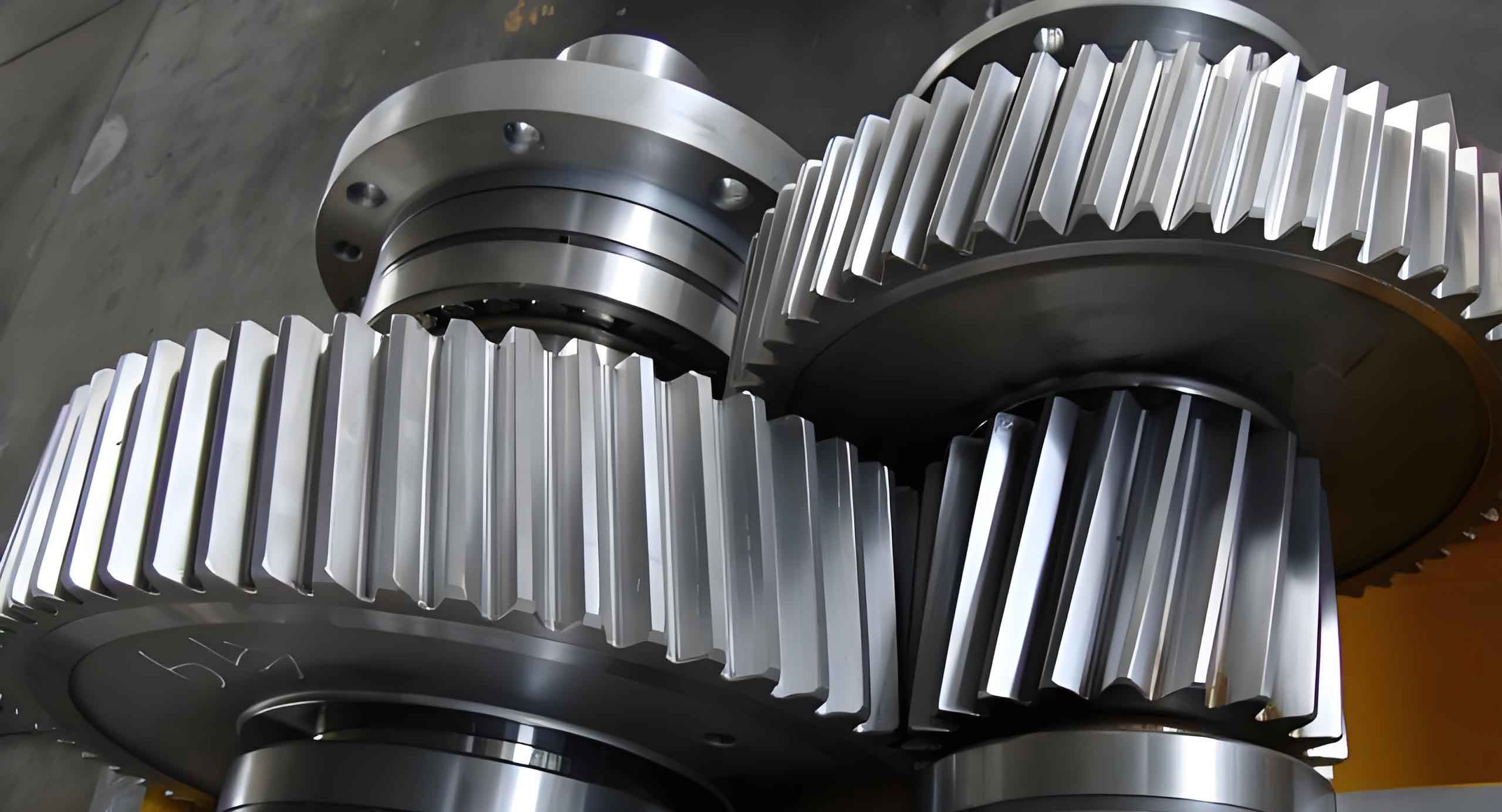
Key Features of Helical Gears:
- Angled Teeth: Typically cut at angles between 15° and 30°.
- Smooth Operation: Reduced noise and vibration due to gradual tooth engagement.
- Load Distribution: Even distribution of load across the teeth.
- High Load Capacity: Increased contact area allows for handling higher loads.
Importance of Studying Wear Mechanisms
Wear is the progressive loss of material from the surface of a gear due to mechanical action. In high-stress environments, understanding the wear mechanisms of helical gears is essential to prevent gear failure, reduce maintenance costs, and extend the lifespan of machinery.
Objectives of Wear Analysis:
- Identify Wear Patterns: Understand how and where wear occurs on helical gears.
- Determine Causes: Identify the factors that contribute to wear.
- Develop Mitigation Strategies: Implement design and maintenance practices to reduce wear.
- Improve Gear Performance: Enhance the reliability and efficiency of helical gears.
Types of Wear Mechanisms in Helical Gears
Several wear mechanisms can affect helical gears, particularly in high-stress environments. Each mechanism has distinct characteristics and causes, requiring specific approaches for mitigation.
Common Wear Mechanisms:
- Abrasive Wear:
- Cause: Occurs when hard particles or asperities slide across the gear surface, removing material.
- Characteristics: Surface scratches and grooves.
- Mitigation: Use of proper filtration systems, high-quality lubricants, and surface coatings.
- Adhesive Wear:
- Cause: Arises when two surfaces come into direct contact under load, causing material transfer between them.
- Characteristics: Scuffing and material build-up.
- Mitigation: Ensuring adequate lubrication, using materials with good compatibility, and optimizing surface finishes.
- Fatigue Wear:
- Cause: Results from cyclic loading leading to the initiation and propagation of cracks.
- Characteristics: Pitting and spalling.
- Mitigation: Designing for optimal load distribution, heat treatment to improve surface hardness, and regular inspection for early detection of cracks.
- Corrosive Wear:
- Cause: Occurs due to chemical reactions between the gear material and environmental contaminants.
- Characteristics: Surface pitting and material degradation.
- Mitigation: Using corrosion-resistant materials, protective coatings, and controlling the operating environment.
Table: Wear Mechanisms in Helical Gears and Mitigation Strategies
Wear Mechanism | Cause | Characteristics | Mitigation Strategies |
---|---|---|---|
Abrasive Wear | Hard particles or asperities | Surface scratches and grooves | Proper filtration, high-quality lubricants, coatings |
Adhesive Wear | Direct surface contact under load | Scuffing and material build-up | Adequate lubrication, compatible materials, surface finish optimization |
Fatigue Wear | Cyclic loading | Pitting and spalling | Optimal load distribution, heat treatment, regular inspection |
Corrosive Wear | Chemical reactions with contaminants | Surface pitting and degradation | Corrosion-resistant materials, protective coatings, environmental control |
Factors Influencing Wear in Helical Gears
Several factors influence the wear mechanisms of helical gears in high-stress environments. Understanding these factors is crucial for designing and maintaining gears to minimize wear.
Key Factors:
- Load:
- Impact: High loads increase the stress on gear teeth, accelerating wear.
- Mitigation: Optimize gear design for load distribution and use materials with high load-carrying capacity.
- Lubrication:
- Impact: Inadequate lubrication leads to increased friction and wear.
- Mitigation: Use high-quality lubricants and ensure proper lubrication practices.
- Material Properties:
- Impact: The hardness, toughness, and chemical composition of gear materials affect wear resistance.
- Mitigation: Select materials with appropriate properties for the operating conditions.
- Operating Environment:
- Impact: Contaminants, temperature, and humidity can accelerate wear.
- Mitigation: Control environmental conditions and use protective measures such as seals and coatings.
List: Strategies to Mitigate Wear in Helical Gears
- Optimize Gear Design: Ensure proper load distribution and tooth profile.
- Use High-Quality Materials: Select materials with high wear resistance.
- Implement Effective Lubrication: Use appropriate lubricants and ensure regular maintenance.
- Control Operating Environment: Minimize exposure to contaminants and control temperature and humidity.
- Regular Inspection and Maintenance: Detect and address wear issues early.
Case Studies of Helical Gear Wear in High-Stress Environments
Electric Vehicles:
In electric vehicles, helical gears are used in transmission systems where they are subjected to high torque and varying loads. Abrasive and adhesive wear are common issues due to the high stresses and frequent start-stop cycles. Using advanced lubricants and high-strength materials, along with regular maintenance, has proven effective in mitigating wear.
Industrial Machinery:
In heavy-duty industrial machinery, helical gears operate under continuous high loads and harsh conditions. Fatigue wear is a significant concern due to cyclic loading. Heat treatment processes, such as carburizing and induction hardening, are employed to enhance surface hardness and reduce fatigue wear.
Conclusion
Understanding the wear mechanisms of helical gears in high-stress environments is essential for improving their performance and extending their lifespan. By identifying the causes and characteristics of different wear mechanisms, and implementing appropriate mitigation strategies, the reliability and efficiency of helical gears can be significantly enhanced. This knowledge is crucial for applications such as electric vehicles and industrial machinery, where the performance of helical gears directly impacts the overall system. Continued research and development in materials, lubrication, and gear design will further advance the durability and performance of helical gears in demanding environments.