Gear transmission is widely used in power transmission due to its high transmission efficiency and precise transmission ratio. Compared with helical gears, bevel gears, and worm gears, spur gears have a simpler structure and are easier to process, making them more widely used in all types of gear transmissions. However, when the coincidence degree interval is designed as 1 < 8 < 2, it means that the number of tooth pairs participating in the meshing process changes constantly (from single-pair meshing to double-pair meshing and then back to single-pair meshing), leading to the time-varying meshing stiffness and easily causing impact, vibration, and noise problems in the system.
In addition, tooth profile errors and center distance errors caused by deviations from the expected machining and assembly accuracy can seriously affect the smoothness of gear transmission. Improving the machining accuracy of gears by one level often requires a significant amount of resources. In some gear transmission systems with low precision requirements, it is often not feasible to reduce the vibration and noise of the system by improving the machining accuracy. How to achieve vibration reduction and noise reduction without changing the original system is a common goal for researchers and manufacturers. Increasing the damping of the system can often achieve more with less effort.
According to whether external energy input is required, the methods of vibration and noise control are divided into active control and passive control. Common active control methods include magnetorheological fluid, electrorheological fluid, vibration motors, etc. Active control methods have the advantages of good control effect and wide frequency bandwidth, but their additional systems are complex, resulting in high costs and reduced system reliability, which limits their wide promotion and use. Passive control methods do not require external energy input and rely on the characteristics of the damper/material itself to convert the mechanical energy of vibration into thermal energy for consumption. Due to their simplicity and low cost, they are widely used.
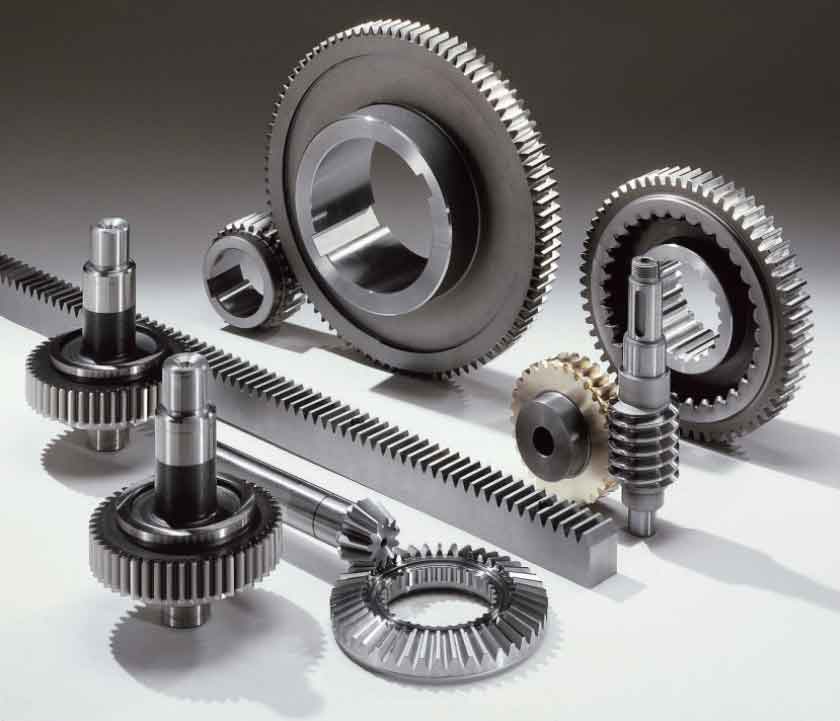
In recent years, viscoelastic materials with strong damping characteristics have attracted the attention of scholars in the field of vibration and noise reduction. Due to their unique hysteresis characteristics (the deformation of molecular chains requires the consumption of some energy), they have achieved good control effects when applied in the noise control of mechanical systems. For example, Fan Rongping et al. used three kinds of viscoelastic damping materials to coat the interior shell of the carriage to reduce the interior noise of railway vehicles during driving and compared the results before and after noise reduction using the psychological acoustic measurement method. Mao Kunpeng et al. coated four kinds of viscoelastic damping materials on the spoke plate of the wheels to reduce the noise generated by the wheel-rail contact during the high-speed train’s operation and verified the noise reduction ability of the viscoelastic damping materials through experiments. With the goal of reducing the mechanical noise of the submarine during navigation, Zeng Zhaoyang et al. analyzed the noise reduction effect of different thicknesses of viscoelastic materials based on the finite element method and proposed an optimization function for the parameters of the constrained damping layer, providing guidance for further application. Due to the ease of use and high cost-effectiveness of viscoelastic materials, they also have good application prospects in different transportation tools such as automobiles and airplanes.
Based on previous studies, this paper selects polymer materials with strong damping characteristics, acrylic ester and polyurethane, and coats them on both sides of the end face of the spur gear to compare the noise reduction effects at different frequencies (coating material types, coating thicknesses), providing guidance for their further application.
Noise Reduction Mechanism of Viscoelastic Materials
The molecular chains of viscoelastic materials are in a curled state when there is no external force acting on them. When there is energy input from the outside, the curled molecular chains stretch, thereby consuming energy. The internal molecular chains of viscoelastic materials are intertwined, and there is a considerable binding force between the molecular chains. To cause the displacement between the molecules, a large amount of energy needs to be consumed.
Viscoelastic materials have an obvious elastic hysteresis phenomenon (as shown in the hysteresis curve of viscoelastic materials in Figure 1). The reason for the hysteresis phenomenon can be attributed to the fact that the process of stretching the intertwined molecular chains after being subjected to force requires a certain time buffer, and the same is true for the elastic recovery process after losing the force. This indicates that viscoelastic materials have good anti-vibration performance and energy consumption ability.
From a microscopic perspective, compared with viscoelastic materials, ordinary elastic materials have no characteristics of molecular chain changes. The result of force-induced deformation will lead to a change in the distance between the lattice, called lattice slip. That is, within the elastic range, the deformation of elastic materials hardly consumes energy. Assuming that the sound radiation energy propagates along the z-direction in the viscoelastic material, at z = 0, the amplitude of the noise is A0, and at z, the amplitude will decay to A0e -βz, and the sound radiation frequency is f. Taking a unit volume of viscoelastic material with a density of ρ, as shown in Figure 2, the energy flowing into this unit volume of viscoelastic material per unit time is P = 1/2 ρV(fA0e -βz)² = 1/2 ρf²A0²e -2βzδz, where V is the unit volume.
It can be deduced from Figure 2 that the energy flowing out per unit time is P’ = 1/2 ρf²A0²e -2β(z + δ0)δz. The energy absorbed by the polymer material per unit time can be calculated as ΔP = P – P’ = 1/2 ρf²A0²e -2βzδz(1 – e -2βz). When δz → 0, 1 – e -2βδz → 2βδz, then ΔP = βρ(fA0δze -βz)². The loss coefficient is κ = ΔP / P = 2βδ, where β is the attenuation coefficient of the material, which is generally 1/2 of the material’s damping coefficient. From equation (4), it can be seen that the attenuation of sound radiation in the polymer material is proportional to the attenuation coefficient and the material thickness.
Spur Gear Shaft System Test Bench
Test Bench Description
According to the literature [16], the noise of the gear system mainly comes from the axial conduction and radiation. Therefore, a spur gear test bench is built, and two viscoelastic materials are evenly coated on the end face of the spur gear for comparative analysis. The parameters of the spur gear used in the test are shown in Table 1. The test bench is shown in Figure 3.
During the test, different viscoelastic materials are evenly coated on the end face of the main (driven) gear to compare and verify the vibration reduction effects of different materials under different working conditions. The test bench and the test system consist of a 1.5 kW DC motor, a Pulse Width Modulation (PWM) speed regulation module, a photoelastic sensor, a vibration acquisition module, a noise acquisition module, and other equipment.
The PWM speed regulation module is used to control the speed of the DC motor, the vibration acquisition module is connected to the photoelastic sensor to monitor the speed of the main shaft in real-time, and the noise acquisition module is equipped with a microphone to collect the noise generated by the gear meshing in real-time.
Results and Discussion
Polyurethane and acrylic ester are evenly coated on the end face of the spur gear as much as possible, and the test is conducted after the materials solidify and harden. Since the spur gear selected for the test is a pair of gears with tooth surface wear (non-uniform wear) faults, when the meshing speed is above 1000 r/min, the noise is too loud (> 100 dB(A)), and the test cannot be conducted. Therefore, the test speeds are selected as 120 r/min, 240 r/min, 360 r/min, 480 r/min, 600 r/min, and 720 r/min. It is found from the analysis of the test results that when the pair of spur gears meshes at a speed of 720 r/min or below, the noise does not exceed 70 dB(A). According to GB 12348 – 2008, when the environmental noise is above 70 dB(A), it will interfere with the conversation, cause restlessness, mental inattention, affect work efficiency, and even lead to accidents. Based on the above two points, this paper selects 720 r/min (rotational frequency fr = 12 Hz, meshing frequency fm = 360 Hz) as the test speed to carry out the noise reduction test under different material types and different material thicknesses. To verify the long-lasting and uniform noise reduction ability of the two viscoelastic materials, the test data after long-term operation is collected for analysis. Due to the large amount of data collected, this paper intercepts the test data for a stable 3-second duration for comparison, as shown in Figure 4.
By comparing with the test data without any coated materials, it can be found that both materials can effectively absorb a part of the noise. Compared with the polyurethane coated with a thickness of 0.4 mm, the acrylic ester coated with a thickness of 1.93 mm has a significant sound absorption effect. At the same time, the test results in Figure 4(b) show good consistency with the theoretical derivation in Section 1, that is, as the material thickness increases, the energy consumed also increases.
The comparison of data in the time domain proves that the two materials have a stable noise reduction ability. To further study the sensitivity of the materials to frequency, the test data is subjected to Fast Fourier Transform to convert the test data to the frequency domain for comparative analysis, and the test results are compared as shown in Figure 5. It can be seen from Figures 5(a) and 5(b) that when the thickness of the coated material is small, the absorption ability for low-frequency noise (20 – 200 Hz) (long-wave noise) is poor. This can be explained by the characteristics of sound wave propagation in the air, that is, long-wave noise has the characteristics of strong penetration and slow decay rate. Therefore, when the material thickness is insufficient, the sound wave can easily penetrate the material and propagate to the outside. And at some frequencies in the low-frequency band, the sound pressure value does not decrease but increases. Combined with its frequency characteristics and the uneven phenomenon on the surface after the material solidifies, it can be analyzed that this uneven phenomenon directly leads to an increase in the imbalance amount, resulting in an increase in the sound pressure amplitude at the multiple frequencies of the rotational frequency on the spectrum. Since the curing time of polyurethane is longer (> 24 h, 25 °C), while the curing time of acrylic ester is shorter (3 – 4 h, 25 °C), acrylic ester is continued to be coated on the end face of the spur gear and the surface flatness is maintained as much as possible for further testing, and the results are shown in Figures 5(c) and 5(d). By comparing the test results of the acrylic ester material with a coating thickness of 0.93 mm and 1.93 mm, it can be found that the increase in material thickness has a significant inhibitory effect on the noise in the low-frequency band.
According to the mechanism of noise generation during the operation of gears, in the meshing process of lightly loaded spur gears, the main noise sources come from the rotational frequency, the multiple frequencies of the rotational frequency, the meshing frequency, and the multiple frequencies of the meshing frequency. These frequencies are usually also the frequencies that researchers engaged in gear vibration and noise research pay more attention to. Therefore, the frequencies of 72 Hz (6fr), 84 Hz (7fr), 156 Hz (13fr), 180 Hz (15fr or 0.5fm), 360 Hz (fm), 720 Hz (2fm), 1440 Hz (120fr, 4fm), and 1668 Hz (139fr) are selected for sound pressure value comparison, and the sound pressure amplitudes at these frequencies are also relatively large in the spectrum. The results are shown in Figure 6. Combining Figures 5 and 6, it can be inferred that there is a relatively obvious imbalance phenomenon in the original system, which leads to an increase in the sound pressure amplitude at the multiple frequencies of the rotational frequency. Analyzing the reason for this phenomenon, it has a great relationship with the spur gear used in the test (a pair of fault gears with non-uniformly worn tooth surfaces). By comparing and analyzing the sound pressure value results at the frequencies of 180 Hz, 360 Hz, and 720 Hz, it can be concluded that the absorption ability of noise increases with the increase of the coating thickness of the material, which shows good consistency with the theoretical derivation. At the frequency of 1440 Hz, a similar rule is not shown, which is caused by the frequency modulation of the multiple frequencies of the rotational frequency and the multiple frequencies of the meshing frequency.
In summary, the materials selected in the test can effectively absorb the noise at the frequencies of the rotational frequency, the multiple frequencies of the rotational frequency, the meshing frequency, and the multiple frequencies of the meshing frequency. To make the research results easier to understand, accept, and disseminate, the test results are converted into sound pressure levels, and the sound pressure level data is weighted and averaged for comparison, and the results are shown in Figure 7.
By analyzing Figure 7, it can be inferred that when the coating thickness is small, the noise reduction ability of polyurethane is more stable, and the noise reduction ability of acrylic ester is about twice that of polyurethane. And as the coating thickness of acrylic ester increases, the stability and amplitude of its noise reduction also increase. By comparing the test results of the thickness of 0.93 mm and 1.93 mm, it can be known that when the coating thickness of acrylic ester increases to a certain value, further increasing the thickness has a smaller impact on the noise reduction amplitude. The reason for this phenomenon may be the insufficient bonding strength between the acrylic ester and the end face of the spur gear, resulting in the inability of the noise energy to be effectively absorbed by the material [10]49.
Conclusions
To reduce the radiation and conduction noise of the end face of the spur gear, a spur gear test bench is built, and two polymer materials (polyurethane and acrylic ester) are coated on the end face of the spur gear. The test results of different coating materials and thicknesses are compared, and the following conclusions are drawn:
- Both materials can effectively absorb a part of the noise. When the coating thickness is small, the inhibitory effect on the noise in the medium and high-frequency bands (200 – 2500 Hz) is more obvious. By comparing the test results of the polyurethane coated with a thickness of 0.4 mm and the acrylic ester coated with a thickness of 1.93 mm, it is found that the sound absorption ability of the latter is significantly enhanced, which shows good consistency with the theoretical derivation results.
- When the selected materials reach a certain thickness, they can effectively absorb the noise from the common frequencies in the spur gear shaft system, including the rotational frequency, the multiple frequencies of the rotational frequency, the meshing frequency, and the multiple frequencies of the meshing frequency.
- When the coating thickness is small, the noise reduction ability of polyurethane is more stable, and the noise reduction ability of acrylic ester is about twice that of polyurethane. By comparing the test results of the thickness of 0.93 mm and 1.93 mm, it can be known that when the coating thickness of acrylic ester increases to a certain value, further increasing the thickness has a smaller impact on the noise reduction amplitude. This phenomenon may be caused by the insufficient bonding strength between the acrylic ester and the end face of the spur gear.