Abstract:
This paper presents a novel gear grinding method aimed at achieving tooth profile modification, enhancing the efficiency and precision of gear manufacturing. By employing an inclined cubic boron carbide grinding disc, the proposed method enables full-tooth-width grinding and tooth profile modification. Vericut machining simulation verifies the effectiveness of this approach, demonstrating that the contact interval is primarily concentrated in the middle of the tooth surface, thereby reducing meshing eccentric load and improving gear transmission stability. Furthermore, a drum shape control adjustment model is established based on the geometric relationship between the grinding trajectory and the gear pitch circle cutting plane, ensuring accurate and stable tooth modification.
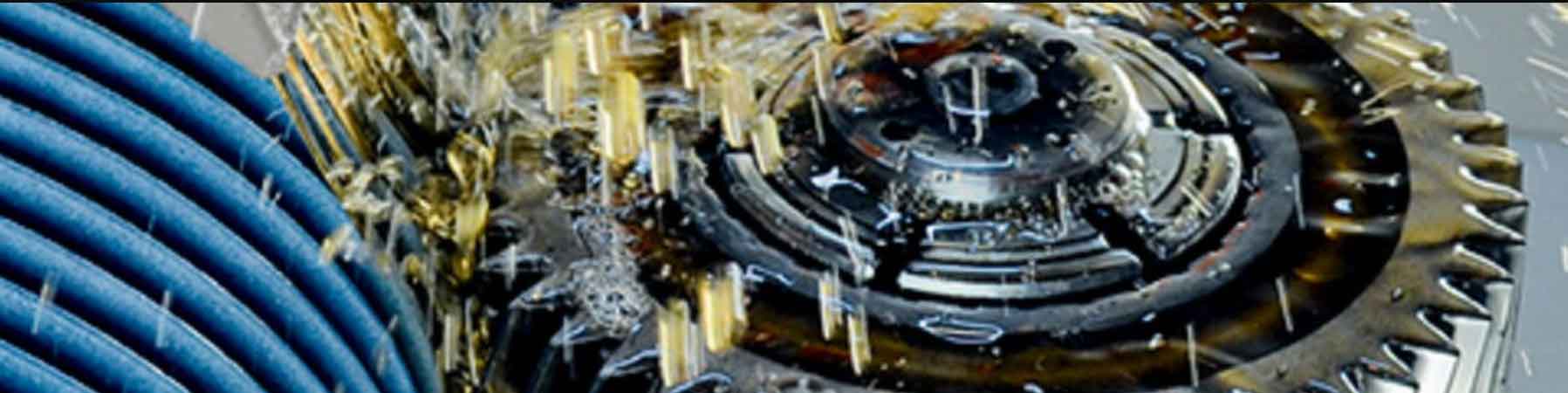
1. Introduction
Cylindrical gears are among the most widely used power transmission mechanisms. However, due to manufacturing and installation errors, as well as elastic deformations, uneven load distribution along the tooth width often occurs, leading to issues such as meshing eccentric load, meshing impact, and noise. These issues can significantly impact the performance and lifespan of gears. Tooth profile modification, particularly the creation of crowned teeth, can effectively address these challenges by distributing the stress uniformly during gear meshing, reducing eccentric loads, and promoting even wear.
This paper focuses on developing an efficient gear grinding method for tooth profile modification. By utilizing an inclined cubic boron carbide grinding disc, we aim to achieve full-tooth-width grinding and precise tooth profile modification. The proposed method is validated through Vericut machining simulation, and the resulting gear is analyzed for its meshing characteristics.
2. Literature Review
Previous studies have explored various approaches for tooth profile modification. Han J et al. proposed using high-order polynomial forms for topological modification on machine tools. Wang Shaojie et al. introduced a multi-axis linkage method for tooth profile modification using a honing wheel. Yu T et al. utilized a diamond dressing wheel with the same tooth surface as the target gear for modification. Jiang Jinke et al. proposed a method involving a conical grinding wheel for axial stroke point contact grinding of gear shapers and topological modification of helical gears. Yang Hui et al. established a mathematical model for tooth profile modification in form grinding based on spatial meshing principles and verified its correctness through experiments on helical crowned gears.
While these methods have shown promise, gear grinding for tooth profile modification often involves complex motions and is challenging to achieve with high precision. This paper aims to address these limitations by proposing a novel grinding method that combines simplicity and precision.
3. Principle of Gear Grinding with Inclined Grinding Disc
3.1. Principle of Conventional Disk Grinding
Traditional gear grinding methods often employ a butterfly-shaped grinding wheel for generating grinding of tooth surfaces. the gear blank undergoes a generating motion (V = ω·r) while the grinding wheel rotates at an angular velocity ωT, forming a grinding plane that grinds the tooth surface. However, this method involves intermittent grinding along the tooth width, resulting in low efficiency and potential precision issues.
3.2. Proposed Method with Inclined Grinding Disc
To overcome the limitations of conventional methods, we propose using an inclined cubic boron carbide grinding disc for full-tooth-width grinding. As illustrated, the grinding disc is installed at an angle θ, and its radius R can be adjusted according to the desired tooth profile modification. By ensuring that the centerline of the gear tooth width is aligned with the center of the grinding disc, symmetric crowned teeth can be produced.
When θ > α (where α is the gear pressure angle), the grinding trajectory forms a conical surface, resulting in micro-crowned teeth and achieving tooth profile modification. Conversely, when θ = α, the grinding trajectory becomes a plane, and tooth profile modification is not achieved.
4. Grinding Device and Simulation
4.1. Grinding Device Model
It consists of a large-diameter grinding disc mounted on a rotary table and a longitudinal slide rail for generating grinding motion. For grinding the left tooth surface, the grinding disc is symmetrically positioned.
4.1.1 Components of the Grinding Device
The key components of the grinding device are:
- Large-diameter Grinding Disc: Made with sintered cubic boron carbide, the disc is mounted on a rotary table and tilted at an angle θ for tooth profile modification. The disc radius R is designed to ensure effective grinding across the entire tooth width.
- Rotary Table: Provides rotational motion to the grinding disc, allowing it to form the desired conical grinding surface.
- Longitudinal Slide Rail: Enables the grinding disc to move axially along the tooth width during the grinding process, ensuring full tooth width grinding.
- Gear Blank: The workpiece, which undergoes tooth profile modification and full tooth width grinding.
- Fixture: Holds the gear blank securely in place during the grinding process.
4.1.2 Operation Principle
To perform the grinding operation, the following steps are followed:
- Positioning and Alignment: The gear blank is positioned and securely clamped onto the fixture. The grinding disc is mounted on the rotary table and tilted at the desired angle θ. The longitudinal slide rail is adjusted to ensure that the disc center is aligned with the midline of the gear tooth width.
- Grinding Motion: The rotary table rotates the grinding disc at a constant angular velocity ωC, forming a conical grinding surface. Simultaneously, the longitudinal slide rail moves the disc axially along the tooth width, enabling full tooth width grinding.
- Generating Motion: The gear blank undergoes generating motion, where it rotates (ωD) and translates (Vxc) to ensure that the grinding disc engages and grinds the tooth surface as a continuous helical path is traced along the tooth profile.
- Adjusting the Drum Shape: The drum shape (or crowning quantity) is controlled by adjusting the tilt angle θ of the grinding disc. As the angle θ changes, the conical grinding surface varies, resulting in different drum shapes on the gear teeth.
4.1.3 Parameter Summary (Table 1)
The parameters summarized in Table 1 are crucial for accurately modeling and operating the grinding device:
Parameter | Description | Value |
---|---|---|
Tooth Number (Z) | Number of teeth on the gear blank | 36 |
Modulus (m) | Module size of the gear | 5 |
Pressure Angle (α) | Pressure angle of the tooth profile | 20° |
Tooth Width (B) | Width of the tooth | 30 mm |
Addendum Coefficient (h*a) | Ratio of the addendum height to the module | 1 |
Clearance Coefficient (C*) | Ratio of the clearance to the module | 0.25 |
Grinding Disc Radius (RT) | Radius of the grinding disc | 500 mm |
Grinding Disc Tilt Angle (θ) | Tilt angle of the grinding disc for tooth profile modification | 20.3° |
By utilizing these parameters and the described components, the proposed grinding device effectively achieves tooth profile modification and full tooth width grinding, enhancing the performance of the cylindrical gear. The following details further elaborate on the operation and advantages of the grinding device model:
4.1.4 Operation Mechanism
The proposed grinding device utilizes a large-diameter grinding disc with cubic boron carbide sintered on its surface. The grinding disc is mounted on a rotary bot, which enables precise positioning and rotation during the grinding process. The grinding motion is achieved by two primary movements:
- Rotational Motion: The grinding disc rotates at a high speed to generate the cutting force and form the required grinding surface.
- Translational Motion: The grinding disc moves axially along the tooth width of the gear blank, ensuring that the entire tooth width is grinded uniformly. This is achieved by a combination of the rotary bot and longitudinal slides.
The angle θ of the grinding disc installation is critical in controlling the tooth profile modification. As explained earlier, when θ is greater than the gear pressure angle α, the grinding trajectory forms a conical surface, leading to the formation of a crowned tooth profile. Conversely, when θ equals α, the grinding trajectory becomes a plane, resulting in a straight tooth profile without modification.
4.1.5 Advantages
The proposed grinding device model offers several advantages over conventional grinding methods:
- Efficient Full Tooth Width Grinding: By using a large-diameter grinding disc and ensuring its axial movement along the tooth width, the proposed method achieves full tooth width grinding in a single pass, significantly improving the grinding efficiency.
- Precision Tooth Profile Modification: The installation angle θ of the grinding disc controls the amount of tooth profile modification, ensuring accuracy and repeatability. This eliminates the need for complex additional motions of the grinding wheel along the gear, simplifying the process and reducing errors.
- Improved Gear Performance: The crowned tooth profile created by the grinding process results in more uniform stress distribution during meshing, reducing meshing partial loads, vibrations, and noise. It also improves the wear resistance and service life of the gear.
- Versatility: The device can be adjusted to grind gears with different tooth profiles and modifications by simply changing the installation angle θ of the grinding disc. This makes the device highly versatile and suitable for various industrial applications.
- Cost-Effective: The use of cubic boron carbide on the grinding disc enhances its wear resistance, reducing the need for frequent dressing or replacement. This translates to lower maintenance costs and increased productivity.
In summary, the proposed grinding device model, with its unique design and operation mechanism, effectively achieves tooth profile modification and full tooth width grinding, significantly enhancing.