Abstract
This paper focuses on reducing the churning resistance of hypoid gears in automobile rear axles. By utilizing the Volume of Fluid (VOF) two-phase flow model and the standard k-ε turbulence model, a three-dimensional numerical model of the automobile rear axle was established. The mechanism of churning power loss in hypoid gears was analyzed. A method to reduce churning resistance was proposed, which involves removing the bolt structure and adding baffle plates on both sides of the hypoid gear. Fluent simulations were conducted to analyze the churning resistance before and after the improvement, and the results were compared with empirical formulas and verified through experiments.
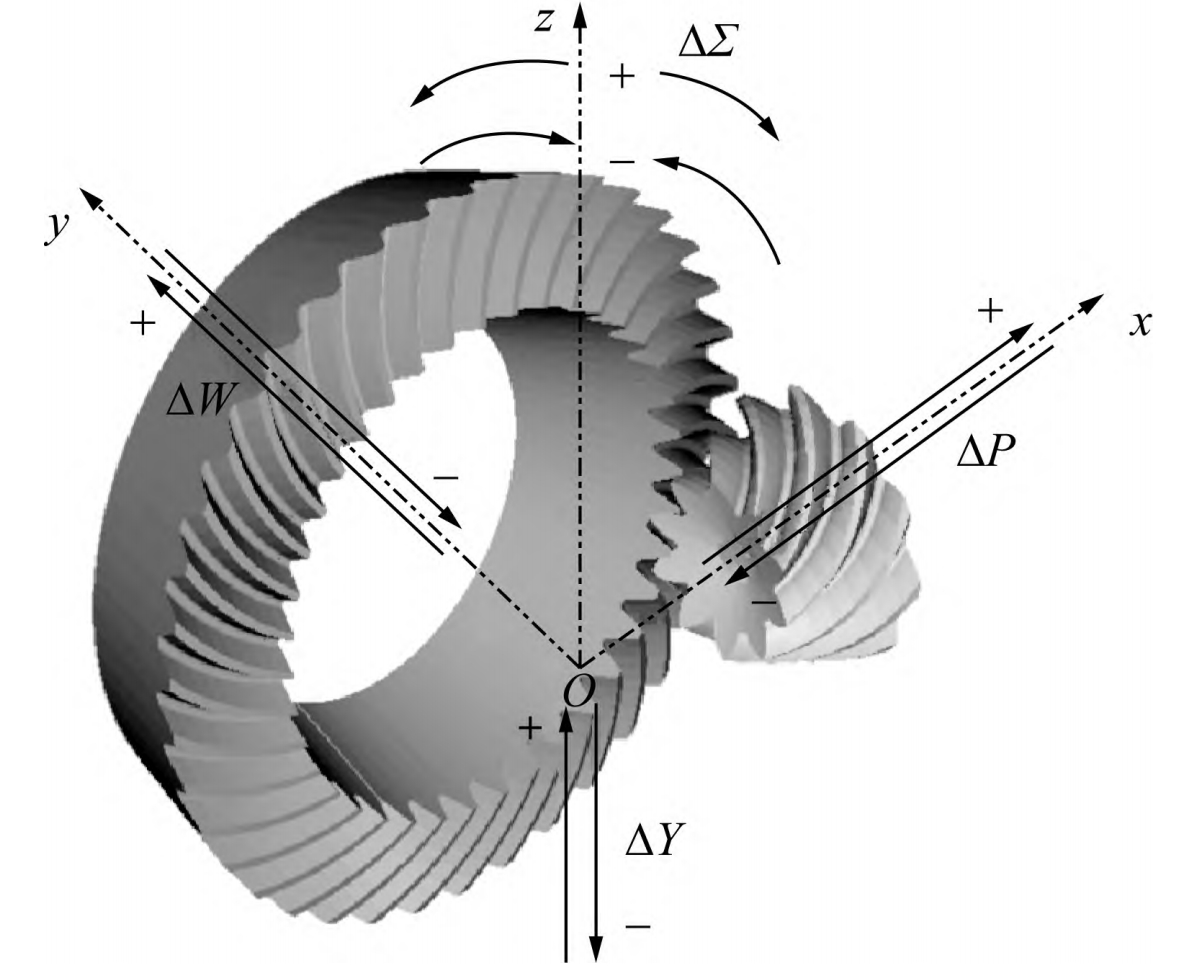
1. Introduction
The rapid development of the economy and society has provided material guarantees for people to pursue a higher quality of life, resulting in a continuous increase in global car ownership. While cars bring convenience to people’s lives, they also pose tremendous pressure on environmental protection and energy utilization. Therefore, research on improving the mechanical transmission efficiency of automotive transmission systems, reducing fuel consumption, and lowering harmful emissions has significant engineering and environmental value.
In rear-wheel-drive vehicles, the driveshaft and rear axle system are commonly used to transmit power and motion. A company found through bench testing that the driveshaft system has high transmission efficiency, while the automobile rear axle, as the core component of the rear-wheel-drive vehicle’s power transmission system, has relatively low transmission efficiency, directly affecting the overall efficiency of the transmission system and ultimately impacting vehicle fuel economy.
2. Literature Review
Previous studies have mainly focused on simpler structures such as cylindrical gears, with limited research on the flow field distribution and churning power loss of more complex hypoid gears in rear axles. The following table summarizes some key studies on churning loss.
Author | Year | Focus | Method |
---|---|---|---|
Kaeman | 1921 | Fluid power loss concept | Theoretical |
Boness | 1989 | Churning losses of disks and gears | Empirical formula |
Terekhov | 1991 | Heat calculation of gear reducers | Experimental |
Kahraman | 2015 | Spin power losses of planetary gear set | Experimental |
Liu Ning | 2014 | Thermal characteristics of power split device | Numerical simulation |
3. CFD Model Establishment
In this paper, computational fluid dynamics (CFD) is used to theoretically analyze the churning mechanism and resistance of hypoid gears in automobile rear axles before and after optimization. The following table lists the parameters of the lubricating oil and air used in the simulation.
Parameter | Lubricating Oil | Air |
---|---|---|
Temperature (°C) | 50 | 50 |
Density (kg/m³) | 839.8 | 1.225 |
Dynamic Viscosity (kg/(m·s)) | 0.48 | 1.7894×10⁻⁵ |
The fluid domain model for CFD analysis.
4. Analysis of Churning Resistance Formation Mechanism and Structural Improvement
4.1 Churning Resistance Formation Mechanism Analysis
The churning resistance formation mechanism of hypoid gears was analyzed at a rotational speed of 887 r/min.
4.2 Structural Improvement
The bolt structure was found to contribute significantly to churning resistance. Therefore, a bolt-free structure using laser welding was proposed for improvement. The models before and after improvement.
Baffle plates were also added to further optimize the churning power loss on the tooth and flange surfaces of the hypoid gear. The baffle plate structure.
5. Comparative Analysis
5.1 Numerical Results
The following table shows the churning resistance torque of the hypoid gear before and after improvement.
Rotational Speed (r/min) | Calculated Value [15] (N·m) | Simulation Value (N·m) | Reduction Rate (%) |
---|---|---|---|
133 | 0.253 | 0.195 (Before), 0.187 (After) | 26.1 |
284 | 0.426 | 0.412 (Before), 0.293 (After) | 31.2 |
443 | 0.578 | 0.605 (Before), 0.417 (After) | 27.9 |
621 | 0.729 | 0.756 (Before), 0.506 (After) | 30.6 |
887 | 0.931 | 0.898 (Before), 0.632 (After) | 32.1 |
1065 | 1.055 | 1.064 (Before), 0.712 (After) | 32.5 |
5.2 Flow Field Characteristics Analysis
The pressure and velocity distributions before and after improvement at a rotational speed of 887 r/min.
6. Conclusion
This paper studied the churning loss mechanism of hypoid gears in an automobile rear axle based on CFD technology and proposed a method for structural improvement to reduce resistance. The following conclusions were drawn:
- Conclusion 1: Besides the tooth surface structure of the hypoid gear, auxiliary structures such as bolts in the rear axle also contribute significantly to churning resistance and increase rapidly with rotational speed.
- Conclusion 2: Removing the bolt structure and adding baffle plates can significantly reduce the maximum dynamic pressure on the hypoid gear, with the reduction amplitude increasing sharply with rotational speed, up to 54%. At the same time, the maximum fluid velocity decreases by up to about 6%. The improved structure can significantly reduce the churning resistance torque of the hypoid gear within a wide range of rotational speeds, with the most significant reduction of 35.9% at higher speeds.
- Conclusion 3: The empirical formula proposed in previous research provides good estimates for the churning resistance torque of the original hypoid gear structure but has lower accuracy when calculating the churning resistance torque of the improved structure with bolt removal and baffle plates added.