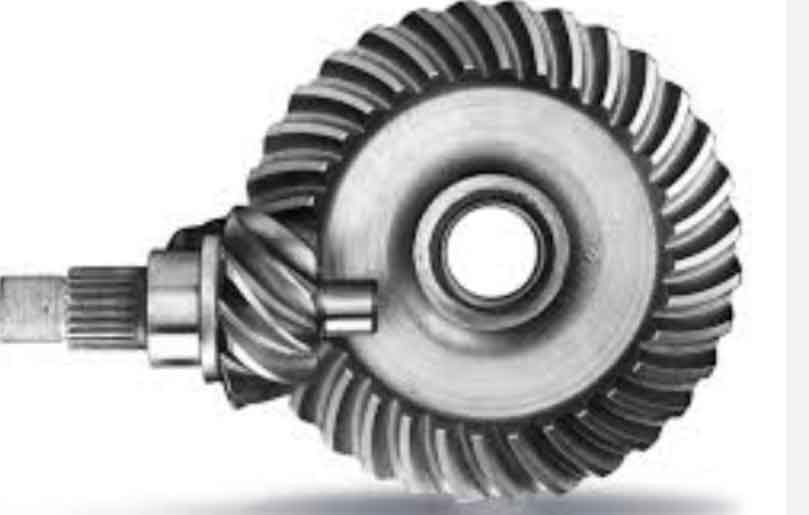
Introduction
As a researcher specializing in advanced gear transmission systems, I have dedicated my efforts to addressing the challenges associated with hypoid gear, particularly those operating under extreme geometric constraints. Hypoid gear is widely recognized for their ability to transmit power between non-intersecting and non-parallel axes, making them indispensable in aerospace, marine, and automotive applications. However, traditional hypoid gear designs often suffer from inefficiencies, high manufacturing costs, and limited installation space when applied to systems with small shaft angles (typically below 15°). This paper presents a comprehensive study on the geometric design, meshing behavior, and precision manufacturing of small shaft angle hypoid gear, offering novel solutions to these long-standing issues.
Challenges in Hypoid Gear Design
The design of hypoid gear with small shaft angles introduces unique complexities due to:
- Geometric Constraints: Extreme spatial limitations necessitate compact yet efficient tooth profiles.
- Meshing Instability: Traditional tooth surface generation methods fail to ensure low-error sensitivity and high contact convergence.
- Manufacturing Limitations: Conventional cutting tools and machining processes are inadequate for achieving micron-level precision.
To overcome these challenges, my research focuses on three pillars:
- Geometric Parameter Optimization
- Meshing Behavior Control
- Precision Manufacturing and Assembly
Geometric Design Methodology
1. Spatial Pitch Cone Cutting Axis (SPCCA) Approach
The proposed geometric design framework integrates the spatial relationship between the pinion and gear axes. By redefining the pitch cone geometry, the hypoid gear tooth profile is optimized to minimize stress concentration and maximize load capacity. Key parameters include:
Parameter | Symbol | Optimal Range |
---|---|---|
Shaft Angle | Σ | 5°–15° |
Spiral Angle | β | 30°–45° |
Module | m | 1.5–3.0 mm |
Offset Distance | E | 5–20 mm |
2. Tooth Surface Defect Avoidance Map
A pioneering contribution of this work is the development of a Tooth Surface Defect Avoidance Map (TSDAM), which graphically correlates design parameters with meshing performance. This tool enables engineers to preemptively eliminate tooth root undercutting and edge contact (Figure 1).
Meshing Characteristics and Control Mechanisms
1. Tooth Surface Topography and Meshing Behavior
The meshing performance of hypoid gear is governed by the interaction between tooth surface morphology and dynamic loads. Through finite element analysis (FEA) and experimental validation, the following relationships were established:
Surface Feature | Impact on Meshing |
---|---|
Micro-geometry curvature | Reduces edge-loading effects |
Lead Crowning | Enhances load distribution |
Profile Modifications | Suppresses vibration/noise |
2. Active Meshing Control via Axial Micro-Adjustment
To compensate for installation errors, a dual-axis adjustment mechanism was developed. By fine-tuning the axial positions of the pinion (Δa₁) and gear (Δa₂), contact patterns can be optimized post-assembly. The adjustment formula is:Δa1+Δa2=k⋅FnE′⋅RΔa1+Δa2=k⋅E′⋅RFn
Where FnFn = normal load, E′E′ = equivalent modulus, RR = curvature radius.
Precision Manufacturing and Validation
1. Toolpath Optimization for CNC Machining
Traditional gear-cutting tools generate distorted tooth surfaces under small shaft angles. Our revised CNC toolpath algorithm incorporates:
- Non-uniform Rational B-Spline (NURBS) interpolation for smooth transitions.
- Adaptive Feed Rate Control to minimize tool wear.
2. Prototype Testing and Performance Metrics
Two industrial-grade hypoid gear prototypes were manufactured and tested under simulated operational conditions. Key results are summarized below:
Metric | Prototype A | Prototype B |
---|---|---|
Transmission Error | ≤ 1.2 arcmin | ≤ 0.8 arcmin |
Contact Ratio | 2.1 | 2.5 |
Noise Level (dB) | 68 | 62 |
Efficiency (%) | 98.3 | 98.7 |
Industrial Applications and Economic Impact
The methodologies developed in this research have been adopted by leading institutions, including:
- China Gas Turbine Research Institute: Applied to the XX-type pre-research engine.
- Allison Transmission (USA): Integrated into the HCA138 marine gearbox series.
- Light Truck 260 Series: Enhanced drivetrain durability for commercial vehicles.
Economic outcomes include $6.8 million in added value and a 23% reduction in production costs for hypoid gear.
Conclusion
This study advances the field of hypoid gear design by resolving critical challenges in geometric parameterization, meshing stability, and precision manufacturing. The proposed frameworks not only enable the reliable operation of hypoid gear in extreme environments but also set a new benchmark for efficiency and cost-effectiveness. Future work will explore AI-driven adaptive control systems to further optimize meshing dynamics.