The tooth surface error pre correction technology can make the machined tooth surface height approach the theoretical design tooth surface, but the first designed tooth surface is often not the optimal tooth surface, so it is particularly important to study how to obtain the optimal mating tooth surface and its corresponding processing method. Active tooth surface design technology can enable designers to design tooth surface topology according to the required meshing performance, so it is a very effective way to obtain the optimal mating tooth surface. This technology is based on the strength and dynamic performance objectives of gear meshing. First, determine the best contact mark (including contact trace, mark position and size) and transmission error curve (including shape and amplitude) of the mating tooth surface, and then design the tooth surface and its processing method that can accurately meet the above conditions, because the optimal tooth surface that cannot be processed has no practical significance, Therefore, the final result is the optimal mating tooth surface and the corresponding processing parameters. The active design technology of tooth surface breaks through the limitations of traditional gear design, enables designers to design the shape of tooth surface according to the functional requirements of gear transmission, and provides a new way to actively control the meshing performance of tooth surface.
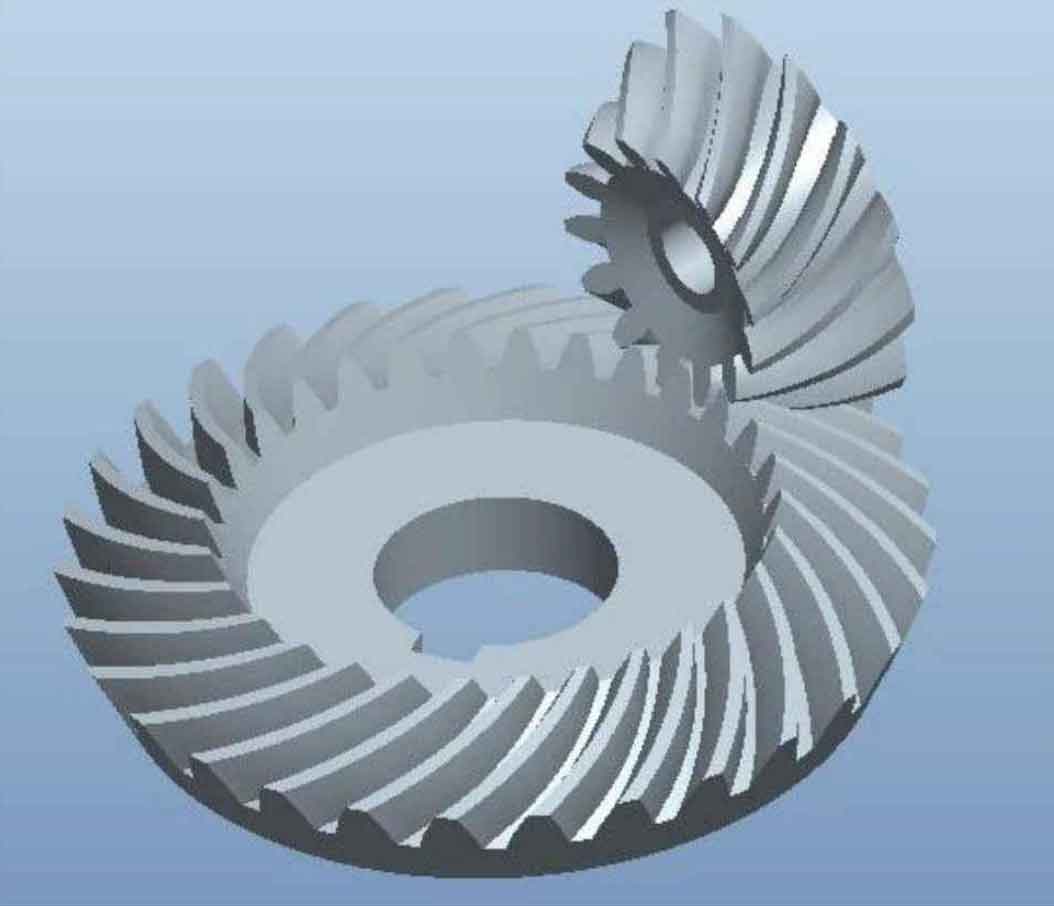
Based on the theoretical tooth surface, the cycloid hypoid gear tooth surface active design method is used to actively control the meshing performance of the tooth surface in the design stage. The main ideas are as follows: first, the theoretical tooth surface of the big wheel is developed into a small wheel auxiliary tooth surface that contacts the line according to the preset transmission error function and meets the preset transmission error curve, Then, the auxiliary tooth surface of the small wheel is modified along the direction of each meshing line according to the three parabolic curves determined by the preset contact marks, and the target tooth surface of the small wheel that meets the preset meshing performance is obtained; Then, an optimization model is established to minimize the square sum of the normal errors between the theoretical tooth surface on both sides and the target tooth surface, and the SQP algorithm is used to solve the model to obtain the adjustment of machining parameters. Finally, the deviation between the TCA results and the preset meshing performance of the two-sided tooth surfaces after the processing parameters are adjusted is compared, and how to selectively ensure the meshing performance of the two-sided tooth surfaces processed by the double-sided method is discussed.
Using the theoretical tooth surface of the big wheel to develop the auxiliary tooth surface of the small wheel in contact with its line, the auxiliary tooth surface of the small wheel is modified along the direction of each meshing line, and the target tooth surface of the small wheel meeting the preset meshing performance is obtained; The least square optimization model of the normal deviation sum between the small gear tooth surface and the target tooth surface is established, and the SQP method is used to solve the small gear tooth surface and its machining parameter adjustment that is highly close to the target tooth surface; By changing the weight coefficient, we can selectively ensure the approximation degree of the tooth surface on one side, and then ensure the meshing performance of that side. For example, for trucks equipped with retarders, the weight coefficient of the reverse side should be appropriately increased in the design to avoid premature failure of the reverse side; This design method enables designers to design the tooth surface shape according to the performance requirements of gear transmission. After promotion, it is also applicable to other gears processed by double-sided method. The active design method of tooth surface in this chapter is based on the theoretical tooth surface, which is an effective way to actively control the meshing performance of gears in the design stage. However, considering the inevitable machining error and the tooth surface deviation caused by heat treatment deformation, this method needs to modify the pinion tooth surface many times in practical application, so that the trial production cycle is too long. Therefore, an active design method based on the actual tooth surface is proposed to solve this problem.