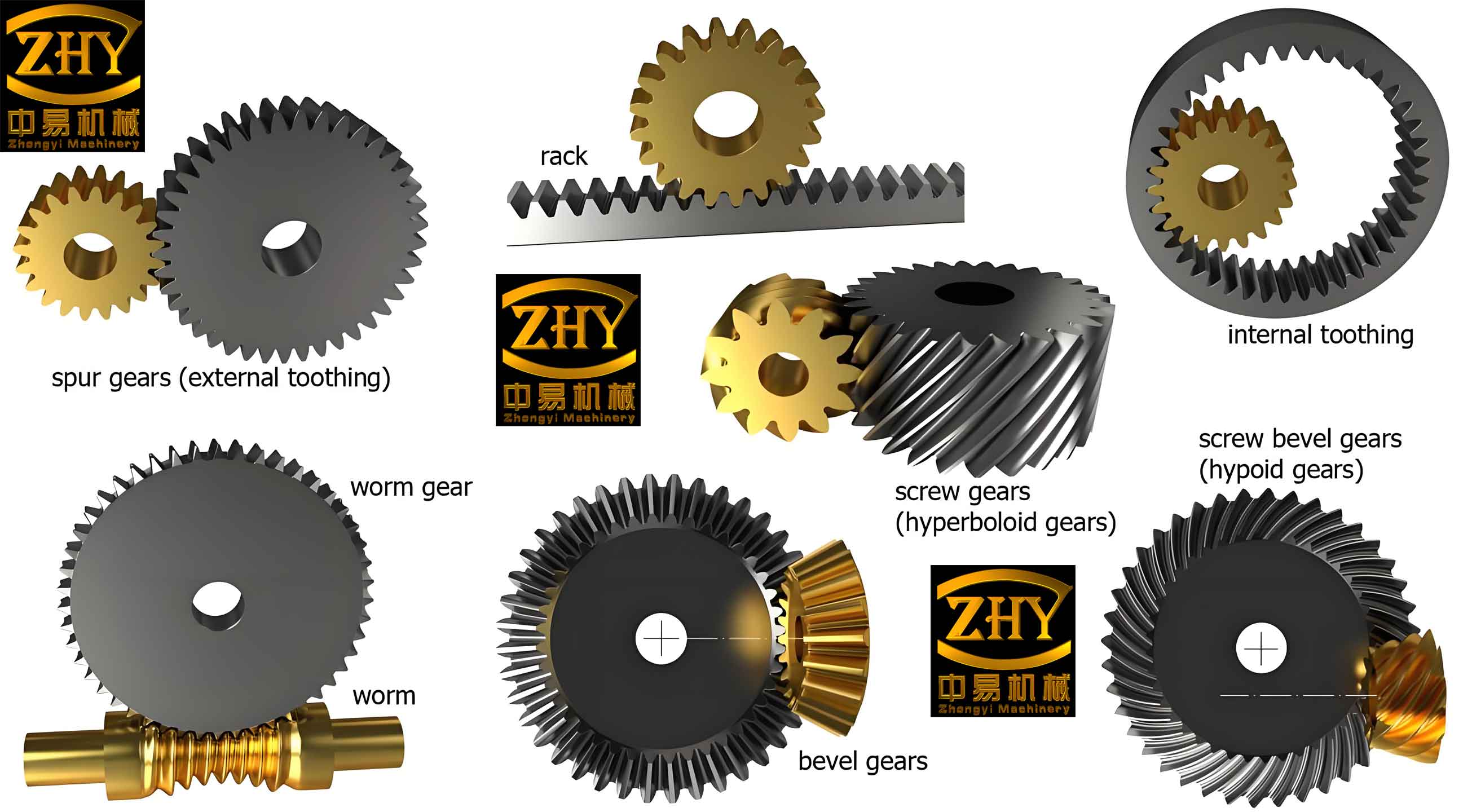
Introduction
The demand for high-performance screw gear has increased significantly across various industries, including automotive, aerospace, and industrial machinery. Advanced manufacturing techniques are essential to meet the stringent requirements for precision, durability, and efficiency. This article explores various advanced manufacturing techniques used in the production of high-performance screw gear, including CNC machining, additive manufacturing, heat treatment, and surface finishing.
Advanced Manufacturing Techniques
CNC Machining
Computer Numerical Control (CNC) machining is a highly precise manufacturing process that uses computerized controls to operate machinery. In screw gear production, CNC machining ensures tight tolerances and high surface finish quality.
Benefits
- High precision and accuracy.
- Consistent quality and repeatability.
- Ability to produce complex geometries.
Additive Manufacturing
Additive manufacturing, also known as 3D printing, is a process of creating objects by adding material layer by layer. This technique is particularly useful for producing complex and customized screw gear.
Benefits
- Rapid prototyping and production.
- Reduced material waste.
- Capability to produce intricate designs.
Heat Treatment
Heat treatment processes, such as carburizing, quenching, and tempering, are used to enhance the mechanical properties of screw gear. These processes improve hardness, strength, and wear resistance.
Benefits
- Increased hardness and durability.
- Enhanced wear resistance.
- Improved fatigue strength.
Surface Finishing
Surface finishing techniques, such as grinding, honing, and coating, are crucial for achieving the desired surface quality and performance characteristics of screw gear.
Benefits
- Improved surface smoothness.
- Reduced friction and wear.
- Enhanced corrosion resistance.
Table 1: Advanced Manufacturing Techniques
Technique | Description | Key Benefits |
---|---|---|
CNC Machining | Computer-controlled precision machining | High precision, consistent quality |
Additive Manufacturing | Layer-by-layer material addition | Rapid prototyping, complex geometries |
Heat Treatment | Processes to enhance mechanical properties | Increased hardness, wear resistance |
Surface Finishing | Techniques to improve surface quality | Smoothness, reduced friction, corrosion resistance |
Transformative Impact on Screw Gear Production
Precision and Accuracy
The integration of advanced manufacturing techniques ensures high precision and accuracy in screw gear production. CNC machining and additive manufacturing allow for the creation of screw gear with tight tolerances and complex geometries, meeting the exact specifications required for high-performance applications.
Enhanced Mechanical Properties
Heat treatment processes significantly enhance the mechanical properties of screw gear. By improving hardness, strength, and wear resistance, these techniques extend the lifespan and reliability of the screw gear, making them suitable for demanding environments.
Customization and Flexibility
Additive manufacturing offers unprecedented customization and flexibility in screw gear design. Manufacturers can quickly produce custom gear tailored to specific applications, reducing lead times and allowing for rapid response to market demands.
Improved Surface Quality
Advanced surface finishing techniques ensure that screw gear achieve the desired surface smoothness and quality. These techniques reduce friction and wear, enhance performance, and increase the longevity of the screw gear.
Table 2: Transformative Impacts of Advanced Manufacturing Techniques
Impact | Description | Benefits |
---|---|---|
Precision and Accuracy | High precision and tight tolerances | Superior performance, reduced defects |
Enhanced Mechanical Properties | Improved hardness, strength, and wear resistance | Increased durability and reliability |
Customization | Ability to produce custom and complex designs | Flexibility, reduced lead times |
Improved Surface Quality | Enhanced smoothness and reduced friction | Better performance, longer lifespan |
Case Studies
Case Study 1: Aerospace Gear Manufacturer
An aerospace gear manufacturer implemented CNC machining and advanced heat treatment processes to produce high-performance screw gear. The result was a 30% increase in gear strength and a significant reduction in wear, enhancing the reliability of the screw gear in critical aerospace applications.
Case Study 2: Automotive Gear Supplier
An automotive gear supplier adopted additive manufacturing and surface finishing techniques to produce customized screw gear for high-performance vehicles. This approach led to a 20% reduction in production time and a 15% improvement in screw gear performance, meeting the stringent demands of the automotive industry.
Case Study 3: Industrial Machinery Company
An industrial machinery company utilized advanced CNC machining and surface finishing techniques to improve the precision and surface quality of their screw gear. The implementation resulted in a 25% increase in screw gear efficiency and a 10% reduction in maintenance costs, boosting overall operational efficiency.
Table 3: Case Study Results
Case Study | Technologies Implemented | Key Improvements |
---|---|---|
Aerospace Gear Manufacturer | CNC machining, heat treatment | Increased strength, reduced wear |
Automotive Gear Supplier | Additive manufacturing, surface finishing | Reduced production time, improved performance |
Industrial Machinery Company | CNC machining, surface finishing | Increased efficiency, reduced maintenance costs |
Future Trends in Screw Gear Manufacturing
Digital Twins
Digital twins are virtual replicas of physical systems used for simulation and analysis. In screw gear production, digital twins can simulate manufacturing processes, predict outcomes, and optimize operations, further enhancing efficiency and quality.
Advanced Data Analytics
Advanced data analytics, combined with machine learning and AI, will continue to drive improvements in screw gear manufacturing. These technologies will enable more precise control over production processes and better prediction of maintenance needs.
Collaborative Robotics (Cobots)
Collaborative robots, or cobots, work alongside human operators, combining the precision of automation with human creativity and problem-solving skills. Cobots will enhance flexibility and efficiency in screw gear production.
Table 4: Future Trends in Screw Gear Manufacturing
Trend | Description | Potential Benefits |
---|---|---|
Digital Twins | Virtual replicas for simulation and optimization | Enhanced process control, quality |
Advanced Data Analytics | AI-driven insights for process improvements | Precise control, predictive maintenance |
Collaborative Robotics | Cobots working alongside humans | Increased flexibility, efficiency |
Conclusion
Advanced manufacturing techniques are transforming the production of high-performance screw gear by enhancing precision, improving mechanical properties, enabling customization, and improving surface quality. The integration of CNC machining, additive manufacturing, heat treatment, and surface finishing techniques is driving significant advancements in gear manufacturing processes. Future trends such as digital twins, advanced data analytics, and collaborative robotics promise to further revolutionize the industry, leading to even greater improvements in performance and productivity.