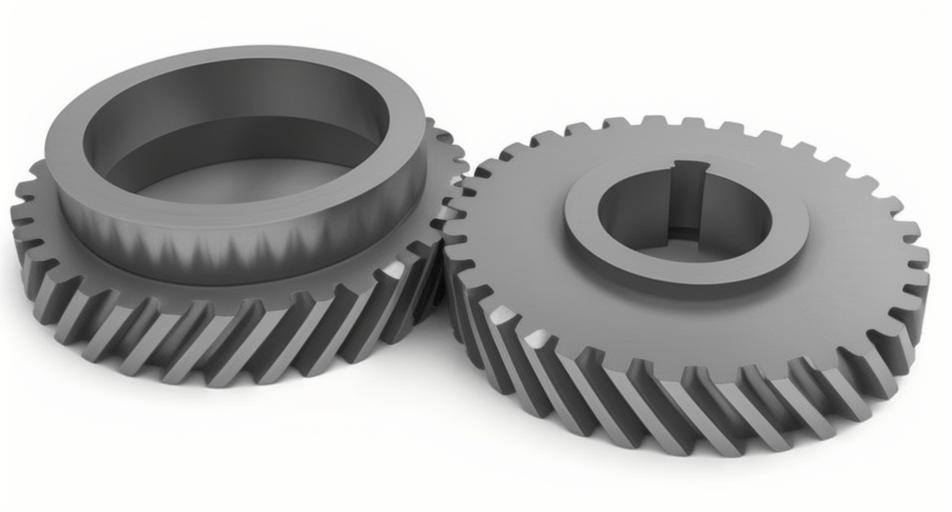
1. CNC (Computer Numerical Control) Machining
- Process: Utilizes computer-controlled machines to precisely cut and shape helical gear. CNC lathes and milling machines can achieve high precision and consistency.
- Advantages:
- High accuracy and repeatability.
- Capability to produce complex geometries.
- Flexibility in manufacturing small to large batches.
- Applications: Ideal for high-precision helical gear in aerospace, automotive, and robotics.
2. Gear Hobbing
- Process: Uses a hobbing machine where a hob (a specialized cutting tool) progressively cuts helical gear teeth as the gear blank and hob rotate in a coordinated manner.
- Advantages:
- Efficient for producing helical gear with high precision.
- Suitable for medium to large-scale production.
- Can achieve fine surface finishes.
- Applications: Common in automotive transmission and industrial machinery.
3. Gear Grinding
- Process: Involves the use of abrasive wheels to finish helical gear teeth to a high degree of precision after the initial cutting process. Methods include form grinding and generating grinding.
- Advantages:
- Achieves very high precision and fine surface finishes.
- Reduces helical gear noise and improves performance.
- Suitable for hardened and tough materials.
- Applications: Critical for aerospace, precision instrumentation, and high-performance automotive applications.
4. Gear Shaping
- Process: Uses a reciprocating cutting tool that moves back and forth to cut helical gear teeth progressively. The tool and workpiece rotate in unison to generate the helical teeth.
- Advantages:
- Capable of producing internal gears and gears with intricate shapes.
- High precision and control over helical gear geometry.
- Applications: Useful in manufacturing internal gears and complex gear profiles in machinery and automotive systems.
5. Additive Manufacturing (3D Printing)
- Process: Layer-by-layer fabrication of helical gear using materials like metal powders or high-strength polymers. Techniques include Selective Laser Melting (SLM) and Electron Beam Melting (EBM).
- Advantages:
- Enables the creation of complex geometries and lightweight designs.
- Reduces material waste and allows for rapid prototyping.
- Customizable for small batch production and unique applications.
- Applications: Emerging in aerospace, medical devices, and custom helical gear applications.
6. Precision Casting and Investment Casting
- Process: Involves creating a wax model of helical gear, coating it with a ceramic shell, and then casting molten metal into the shell to form the gear.
- Advantages:
- Can produce complex and detailed helical gear shapes with high precision.
- Suitable for producing helical gear from various alloys.
- Good for medium to large-scale production.
- Applications: Used in aerospace, automotive, and heavy machinery.
7. Powder Metallurgy
- Process: Involves pressing metal powders into a mold and then sintering them to create a solid gear. This process can include secondary machining and finishing for higher precision.
- Advantages:
- Capable of producing high-strength helical gear with complex shapes.
- Minimizes material waste and offers high production efficiency.
- Good for mass production of small to medium-sized helical gear.
- Applications: Common in automotive parts, small machinery, and consumer electronics.
Advanced Inspection and Quality Control Techniques
- Coordinate Measuring Machines (CMM)
- Used for precise measurement of helical gear dimensions and profiles.
- Ensures adherence to tight tolerances and specifications.
- Gear Metrology
- Involves the use of specialized helical gear measuring instruments to check tooth geometry, pitch, and surface finish.
- Ensures high accuracy and quality of the finished helical gear.
- Non-Destructive Testing (NDT)
- Techniques such as ultrasonic testing and X-ray inspection to detect internal flaws and ensure material integrity without damaging helical gear.
- Critical for high-stress applications in aerospace and automotive sectors.
Conclusion
Advanced manufacturing techniques for high-precision helical gear leverage the latest in machining technology, additive manufacturing, and inspection methods to achieve exceptional accuracy and quality. These techniques are crucial for applications requiring high performance, reliability, and durability, such as in aerospace, automotive, and industrial machinery. The choice of technique depends on factors like production volume, material, complexity, and specific application requirements.