Wear detection in spur gear systems is crucial for preventing unexpected failures and ensuring reliable operation. Advanced wear detection methods utilize a combination of technologies to monitor the condition of gears in real-time, providing early warnings of potential issues. Here are some of the most effective advanced wear detection methods:
1. Vibration Analysis
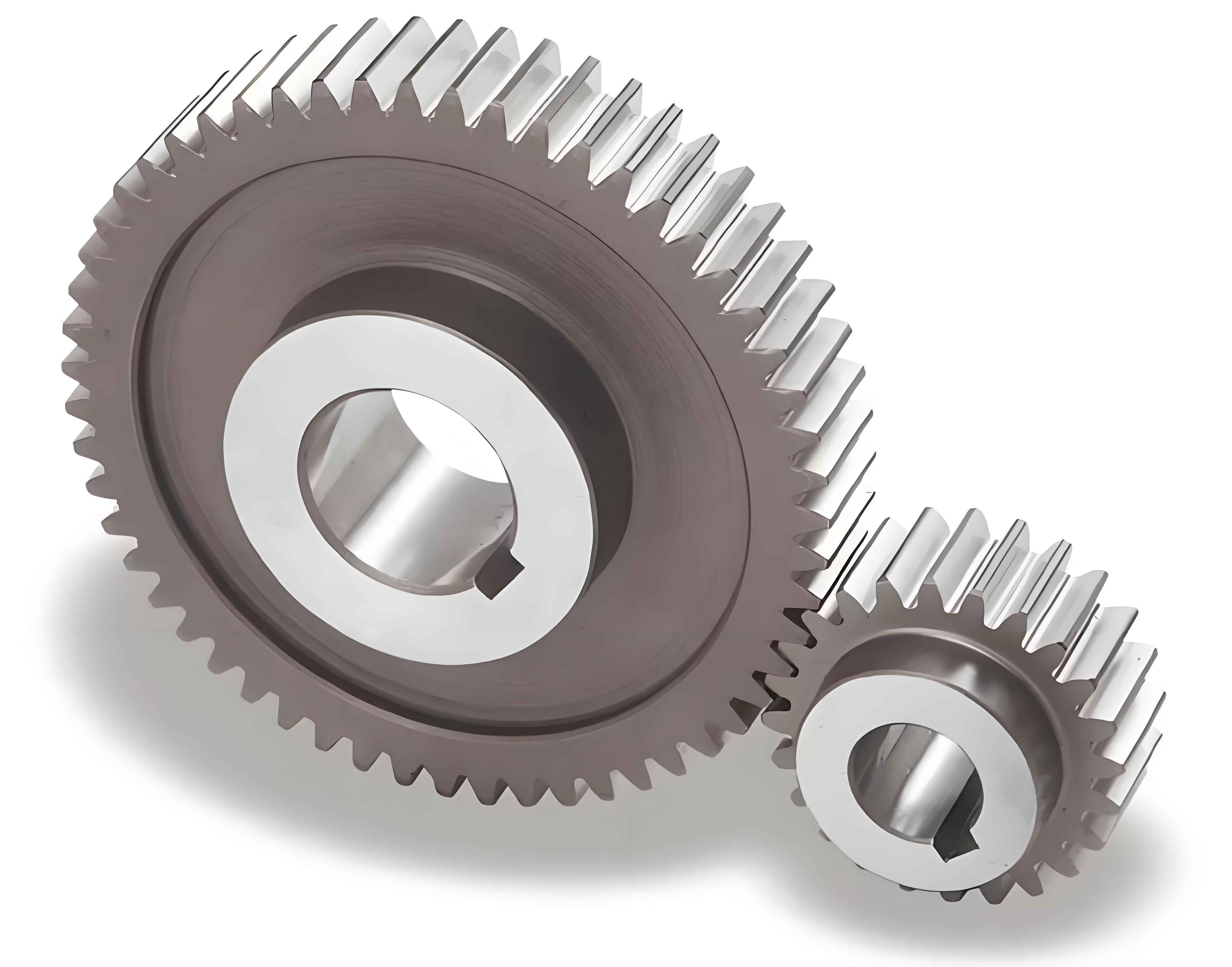
- Overview: Measures the vibrations produced by the spur gear system to detect changes in frequency and amplitude that indicate wear or damage.
- Techniques:
- Time-Domain Analysis: Monitors the amplitude of vibrations over time to identify sudden changes that may indicate wear.
- Frequency-Domain Analysis: Analyzes the frequency spectrum of vibrations to detect characteristic frequencies associated with specific spur gear faults.
- Envelope Analysis: Extracts and analyzes the high-frequency components of the vibration signal to detect early-stage gear faults.
- Benefits:
- Early detection of spur gear wear and faults.
- Can identify specific types of spur gear defects (e.g., pitting, spalling).
- Non-invasive and can be performed during normal operation.
2. Acoustic Emission (AE) Monitoring
- Overview: Detects the high-frequency stress waves emitted by the material as it undergoes deformation or crack propagation.
- Techniques:
- Sensor Placement: AE sensors are strategically placed on the gearbox or spur gear housing to detect emitted waves.
- Signal Processing: Analyzes the AE signals to identify the onset of wear or damage.
- Benefits:
- High sensitivity to the initiation of wear and cracks.
- Can detect very early stages of damage.
- Suitable for continuous monitoring.
3. Oil Analysis
- Overview: Involves analyzing the lubricant for the presence of wear particles and other contaminants that indicate spur gear wear.
- Techniques:
- Spectroscopic Analysis: Measures the concentration of metal particles in the oil to identify wear rates and sources.
- Particle Counting: Counts and sizes particles in the oil to monitor wear progression.
- Ferrous Density Analysis: Detects ferrous particles in the oil to monitor the wear of steel components.
- Benefits:
- Provides detailed information about the type and extent of wear.
- Can identify specific sources of wear particles.
- Non-invasive and can be performed without stopping the spur gear system.
4. Thermography
- Overview: Uses infrared cameras to measure the temperature distribution on the spur gear surface.
- Techniques:
- Infrared Imaging: Captures thermal images of the spur gear system to identify hotspots that indicate excessive friction or wear.
- Temperature Analysis: Analyzes temperature variations over time to detect changes in thermal patterns associated with wear.
- Benefits:
- Non-contact and non-invasive.
- Can detect localized areas of excessive heat due to wear or misalignment.
- Suitable for continuous monitoring.
5. Ultrasound Inspection
- Overview: Uses high-frequency sound waves to detect surface and subsurface defects in the spur gear.
- Techniques:
- Pulse-Echo Method: Sends ultrasonic pulses into the spur gear and measures the echoes returned from defects.
- Through-Transmission Method: Measures the attenuation of ultrasonic waves passing through the spur gear to detect internal defects.
- Benefits:
- High resolution for detecting small defects.
- Can detect both surface and subsurface wear.
- Non-invasive and can be used during maintenance periods.
6. Laser Surface Scanning
- Overview: Uses laser beams to scan the surface of the spur gear and detect wear and surface roughness.
- Techniques:
- 3D Laser Scanning: Creates a high-resolution 3D model of the spur gear surface to detect wear patterns and measure wear depth.
- Surface Profilometry: Measures the surface roughness and texture to monitor wear progression.
- Benefits:
- High precision and accuracy in measuring wear.
- Provides detailed surface characterization.
- Suitable for periodic inspections.
Summary of Advanced Wear Detection Methods
Method | Techniques and Tools | Key Benefits |
---|---|---|
Vibration Analysis | Time-domain, frequency-domain, envelope analysis | Early detection, specific fault identification, non-invasive |
Acoustic Emission | Sensor placement, signal processing | High sensitivity, early-stage detection, continuous monitoring |
Oil Analysis | Spectroscopic analysis, particle counting, ferrous density | Detailed wear information, source identification, non-invasive |
Thermography | Infrared imaging, temperature analysis | Non-contact, detects hotspots, continuous monitoring |
Ultrasound Inspection | Pulse-echo, through-transmission | High resolution, surface and subsurface defect detection, non-invasive |
Laser Surface Scanning | 3D laser scanning, surface profilometry | High precision, detailed surface characterization, periodic inspections |
Conclusion
Advanced wear detection methods for spur gear systems leverage cutting-edge technologies to provide early warnings of wear and potential failures. By implementing a combination of these methods, operators can achieve comprehensive monitoring of gear health, reduce downtime, and extend the lifespan of spur gear systems. Each method offers unique benefits and is selected based on the specific requirements of the spur gear system and operational environment.