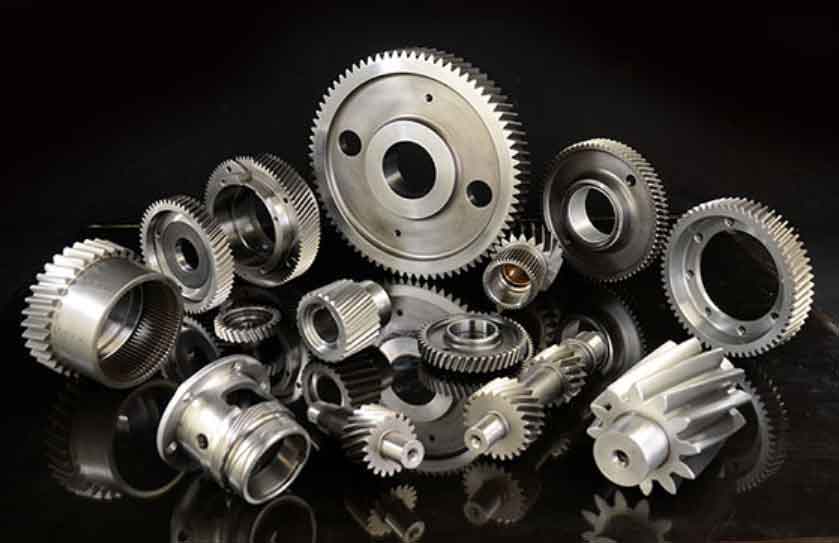
Advancements in helical gear technology have significantly improved the reliability and load-carrying capacity of gear systems. Engineers and manufacturers have continuously worked on enhancing various aspects of helical gears to meet the demands of modern applications. Here are some key advancements that have contributed to improved reliability and load capacity:
- Computer-Aided Design (CAD): The use of sophisticated CAD software allows for more precise and optimized gear designs. Engineers can now model and analyze complex gear geometries, tooth profiles, and contact patterns, leading to improved load distribution and reduced stress concentrations.
- Finite Element Analysis (FEA): FEA has revolutionized gear design by providing a deeper understanding of gear behavior under different loads and operating conditions. This simulation technique helps identify potential weak points and optimize gear designs for higher load capacity and reliability.
- Materials and Heat Treatment: Advancements in metallurgy have resulted in the development of high-strength and wear-resistant materials specifically tailored for helical gears. Additionally, advanced heat treatment processes, such as carburizing and nitriding, improve the gear’s surface hardness and overall strength.
- Precision Manufacturing: Manufacturing processes have become more precise and repeatable, ensuring consistent and accurate gear tooth profiles. CNC machining, grinding, and honing technologies allow for tight tolerances and high-quality gear production.
- Tooth Surface Finishing: Advanced gear tooth finishing techniques, such as superfinishing and polishing, enhance the surface quality and reduce friction between mating gears, leading to smoother meshing and lower wear.
- Gear Coatings and Lubricants: Specialized coatings and lubricants have been developed to reduce friction, wear, and heat generation in helical gear systems. These advancements contribute to improved reliability and longer service life.
- Noise and Vibration Reduction: Innovative designs and modifications, such as helix angle optimization and profile shifting, have helped in reducing gear noise and vibration during operation.
- Optimized Gear Geometry: Engineers have refined helical gear geometry to improve tooth contact, load distribution, and bending strength. Modified profiles, such as the “crowned” tooth profile, help minimize edge loading and enhance gear performance.
- Multi-stage Gearboxes: Helical gears are often used in multi-stage gearboxes, allowing for higher gear reduction ratios without compromising load capacity. This setup is particularly beneficial in heavy machinery and automotive applications.
- Integrated Gear Design and System Analysis: Modern gear technology considers the entire gear system’s dynamics, including bearings, shafts, and housing. Integrated design and analysis help optimize the overall system for improved reliability and load capacity.
These advancements in helical gear technology have made them a preferred choice in various industries, including automotive, aerospace, machinery, and robotics. With increased reliability, load-carrying capacity, and efficiency, helical gears continue to play a vital role in modern engineering applications.