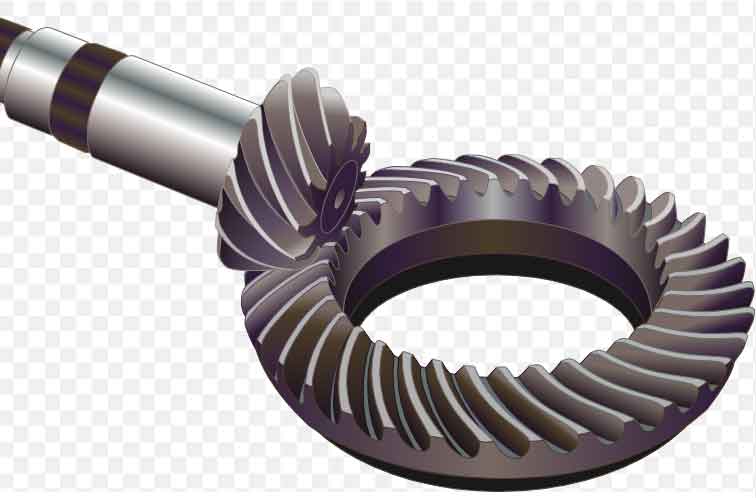
Advancements in spiral bevel gear technology have led to significant improvements in reliability and load-carrying capacity, making them even more suitable for demanding applications. Several key advancements have contributed to these enhancements:
1. Improved Materials and Heat Treatment:
- Advancements in metallurgy have led to the development of high-performance materials specifically designed for spiral bevel gears. These materials offer superior strength, hardness, and wear resistance, enabling the gears to handle higher loads and operate under more challenging conditions. Advanced heat treatment processes, such as carburizing and nitriding, further enhance the material properties, ensuring improved gear durability and reliability.
2. Precision Manufacturing Techniques:
- Modern manufacturing techniques, including computer numerical control (CNC) machining, gear grinding, and gear honing, allow for higher precision in producing spiral bevel gears. The use of these advanced techniques ensures accurate tooth profiles and better gear meshing, reducing friction and wear and increasing the gears’ load-carrying capacity.
3. Gear Design Optimization:
- Advanced gear design software enables engineers to optimize the spiral bevel gear’s tooth profile, tooth contact pattern, and microgeometry. The optimized design ensures better load distribution and minimizes stress concentrations, leading to improved gear reliability and load capacity.
4. Microgeometry Modifications:
- Microgeometry modifications, such as tooth crowning and lead corrections, are applied to enhance the tooth contact pattern. These modifications distribute the load more evenly along the tooth surface, reducing edge contact and improving gear performance under heavy loads.
5. Advanced Lubrication and Cooling Systems:
- Innovations in lubrication and cooling systems contribute to the reliability of spiral bevel gears. Effective lubrication reduces friction and wear, while efficient cooling prevents overheating, maintaining the gear’s performance and load capacity.
6. Finite Element Analysis (FEA) and Simulation:
- FEA and simulation techniques have become more sophisticated, allowing for more accurate modeling and analysis of spiral bevel gears’ performance under various loads and conditions. This enables engineers to optimize gear designs and predict their behavior, ensuring enhanced reliability.
7. Surface Coatings and Treatments:
- Specialized surface coatings and treatments, such as diamond-like carbon (DLC) coatings, improve the gear’s surface hardness and reduce friction. These coatings enhance wear resistance, extend gear life, and increase the gears’ load capacity.
8. Gearbox Design Integration:
- Advancements in gearbox design and integration have led to more efficient and compact gearboxes. By optimizing the entire gearbox system, engineers can ensure that the spiral bevel gears work in harmony with other components, further improving reliability and load-carrying capacity.
9. Material Inspection and Quality Control:
- Advancements in non-destructive testing and quality control technologies allow for more accurate inspection of gear materials and manufacturing processes. This ensures that only gears meeting strict quality standards are used, enhancing reliability and performance.
These advancements in spiral bevel gear technology have resulted in gears with improved reliability, higher load capacity, and longer service life. As a result, spiral bevel gears are now utilized in a wide range of critical applications, including aerospace, automotive, robotics, and industrial machinery, where high precision, durability, and load-carrying capabilities are essential.