Advancements in spiral bevel gear technology have led to significant improvements in reliability and load capacity. Here are some key advancements that have contributed to enhancing the performance of spiral bevel gears:
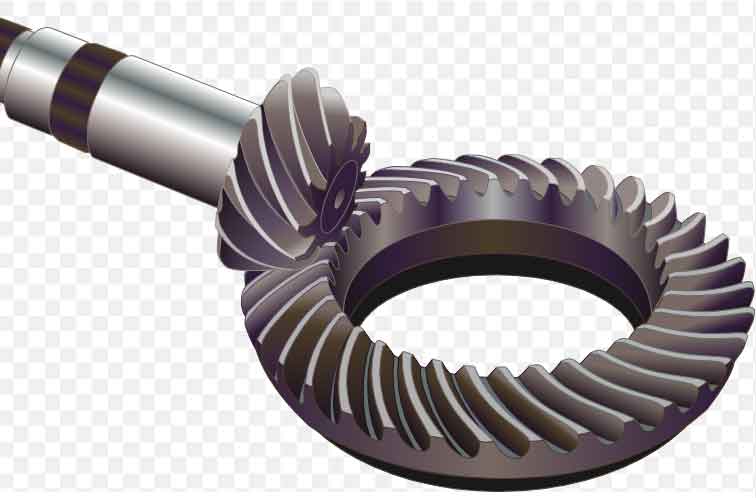
1. Improved Gear Design:
Advanced computer-aided design (CAD) and simulation tools allow engineers to optimize the gear design for specific applications. This includes precise control over tooth geometry, surface finish, and contact patterns, resulting in gears that can handle higher loads and transmit power more efficiently.
2. Enhanced Manufacturing Techniques:
Manufacturing processes, such as CNC machining and 5-axis milling, have become more sophisticated, allowing for tighter tolerances and better control over the gear’s shape and surface quality. This results in gears with improved tooth accuracy and reduced noise and vibration during operation.
3. Material Advancements:
The use of high-strength materials and specialized alloys has improved the load-carrying capacity and durability of spiral bevel gears. Advanced heat treatment processes, such as carburizing and nitriding, further enhance the gear’s surface hardness and wear resistance.
4. Surface Coatings and Treatments:
Innovative surface treatments, such as shot peening and superfinishing, can improve the gear’s resistance to fatigue and reduce wear. Additionally, specialized coatings can provide better lubrication and reduce friction, leading to increased efficiency and reduced heat generation.
5. Contact Analysis and Optimization:
Advanced computer simulations and finite element analysis (FEA) techniques allow engineers to perform in-depth contact analysis of spiral bevel gears under various loads and operating conditions. This enables optimization of tooth contact patterns and load distribution, ensuring uniform loading across the gear teeth.
6. 3D Printing and Additive Manufacturing:
The advent of 3D printing and additive manufacturing technologies has opened up new possibilities for producing complex spiral bevel gears with customized geometries. This flexibility enables the design of gears tailored to specific applications, thereby improving load capacity and reliability.
7. Gear Geometry Modifications:
Techniques like lead crowning and profile crowning help distribute loads more evenly and reduce stress concentrations, enhancing the gear’s load-carrying capacity and reducing the risk of failure.
8. Noise and Vibration Reduction:
Advancements in gear design, tooth contact analysis, and surface treatments have also contributed to reducing noise and vibration levels, leading to quieter and smoother gear operation.
9. Non-Destructive Testing (NDT) Techniques:
Non-destructive testing methods, such as magnetic particle inspection and ultrasound, are employed to detect potential defects or flaws in the gears, ensuring higher reliability and safety.
10. Digitalization and Industry 4.0:
The integration of digitalization and industry 4.0 technologies in gear manufacturing processes allows for real-time monitoring, predictive maintenance, and data-driven optimization. This leads to improved gear performance and increased overall equipment efficiency.
These advancements in spiral bevel gear technology have significantly improved the reliability, load capacity, and overall performance of these gears, making them suitable for a wide range of critical applications in various industries. As research and development continue, we can expect even more innovations that further enhance the capabilities of spiral bevel gears.