Advancements in spiral bevel gear technology have led to improvements in performance, efficiency, and reliability. Here are some notable innovations in this field:
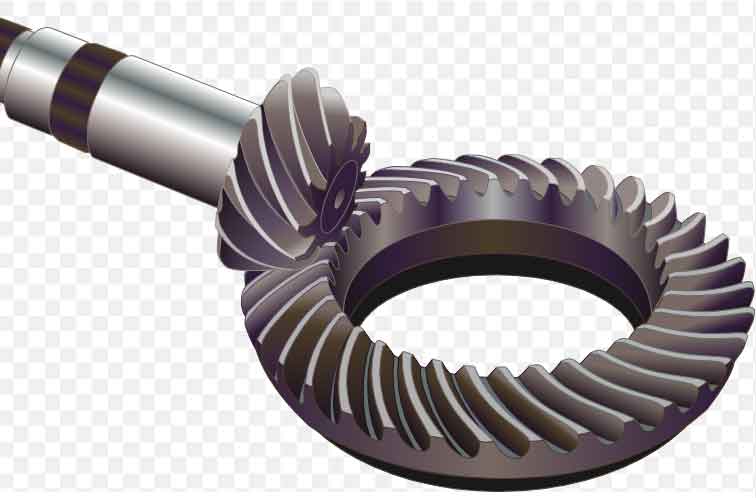
3D Printing/Additive Manufacturing:
The emergence of 3D printing and additive manufacturing techniques has opened up new possibilities for gear production. Complex spiral bevel gears with optimized tooth profiles and customized designs can now be manufactured using additive manufacturing methods, allowing for faster prototyping, reduced lead times, and improved design flexibility.
Advanced Simulation and Analysis Tools:
Computational methods, such as finite element analysis (FEA) and computational fluid dynamics (CFD), have become more sophisticated, enabling engineers to simulate gear behavior more accurately. These tools help optimize gear designs, predict performance under various operating conditions, and identify potential failure points, leading to more reliable and efficient spiral bevel gears.
Surface Coatings and Treatments:
Innovative surface coatings and treatments have been developed to enhance the performance and durability of spiral bevel gears. These include advanced heat treatments, such as ion nitriding or carbonitriding, to increase surface hardness and wear resistance. Additionally, specialized coatings, like diamond-like carbon (DLC) or low-friction coatings, can minimize friction, reduce wear, and improve gear efficiency.
Improved Tooth Profile Optimization:
Advanced algorithms and optimization techniques are now employed to design tooth profiles that minimize noise, vibrations, and stress concentrations. By optimizing the tooth geometry, including pressure angle, tooth thickness, and profile modifications, engineers can achieve smoother gear meshing, lower noise levels, and improved load distribution.
Enhanced Manufacturing Techniques:
Manufacturing processes for spiral bevel gears have been refined to achieve higher precision and quality. Computer-controlled machining, such as CNC milling and grinding, ensures tighter tolerances and improved surface finishes. Additionally, advanced gear inspection methods, such as coordinate measuring machines (CMM) and gear checking machines, allow for more accurate measurement and verification of gear geometries.
Material Advancements:
The development of new materials has expanded the possibilities for spiral bevel gear applications. High-strength alloys, such as carburizing steels, alloy steels, and powder metallurgy materials, offer improved mechanical properties and wear resistance. Non-metallic materials, like composites or ceramics, are also being explored for specific applications that require lightweight and high-performance gears.
Smart Monitoring and Condition-based Maintenance:
With the advent of the Internet of Things (IoT) and Industry 4.0 technologies, gears can be equipped with sensors to monitor operating conditions and performance in real-time. This enables condition-based maintenance, where maintenance activities are scheduled based on actual gear health and usage data, resulting in optimized maintenance practices and increased gear reliability.
These advancements in spiral bevel gear technology contribute to improved gear performance, efficiency, and reliability in various industries. They address challenges such as noise reduction, wear prevention, and optimization of gear design, paving the way for more advanced and high-performing mechanical systems.