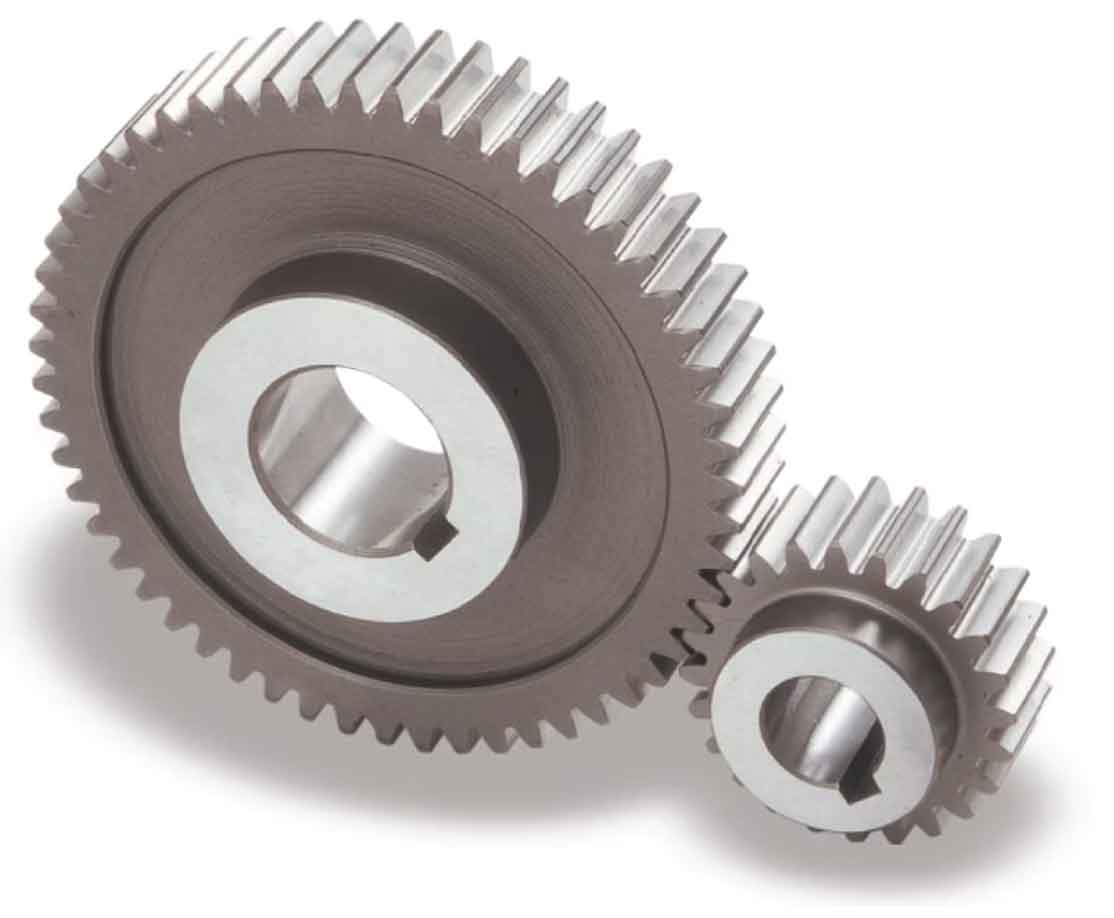
Advancements in spur gear manufacturing have significantly contributed to improving precision and quality in gear production. Here are some key advancements that have played a crucial role:
- Computer-Aided Design (CAD): CAD software has revolutionized gear design by allowing engineers to create precise and complex gear geometries. CAD systems enable designers to optimize gear performance, minimize noise and vibration, and ensure proper meshing and load distribution.
- Computer-Aided Manufacturing (CAM): CAM software complements CAD by converting the gear design into machine instructions. CAM systems generate tool paths and optimize machining strategies, resulting in more accurate and efficient production processes.
- High-Precision Machining: Modern machining techniques, such as CNC (Computer Numerical Control) machining, have greatly improved the precision of gear manufacturing. CNC machines can accurately control cutting tools, resulting in consistent gear dimensions, tooth profiles, and surface finishes.
- Advanced Gear Cutting Methods: Traditional gear cutting methods, such as hobbing and shaping, have been enhanced with improved tool materials and coatings. Additionally, newer techniques like precision grinding, electrochemical machining (ECM), and laser cutting have emerged, offering higher precision and surface quality.
- Metrology and Inspection: Advancements in metrology tools and inspection techniques have contributed to higher quality gears. Coordinate measuring machines (CMMs), optical measurement systems, and non-destructive testing methods enable comprehensive analysis of gear geometry, tooth profile, and surface integrity.
- Materials and Heat Treatment: The development of advanced materials, including high-strength alloys and powdered metals, has increased the durability and load-carrying capacity of gears. Furthermore, advancements in heat treatment processes, such as carburizing, nitriding, and induction hardening, ensure precise control of gear hardness and case depth.
- Simulation and Modeling: Computer simulations and virtual prototyping have become invaluable tools in gear manufacturing. Finite element analysis (FEA) and computational fluid dynamics (CFD) simulations allow engineers to optimize gear designs, predict performance, and identify potential issues before physical production.
- Automation and Robotics: Automation has improved gear manufacturing efficiency, accuracy, and repeatability. Robots are employed for tasks like loading and unloading workpieces, tool changing, and gear inspection. Automated systems reduce human error, increase production rates, and ensure consistent quality.
- Continuous Improvement in Gear Design Standards: Standards organizations continually refine and update gear design standards, such as AGMA (American Gear Manufacturers Association) and ISO (International Organization for Standardization). These standards provide guidelines for gear geometry, tolerances, and manufacturing processes, promoting precision and quality across the industry.
These advancements in spur gear manufacturing have led to increased precision, improved quality control, enhanced efficiency, and higher performance in gear applications across various industries.