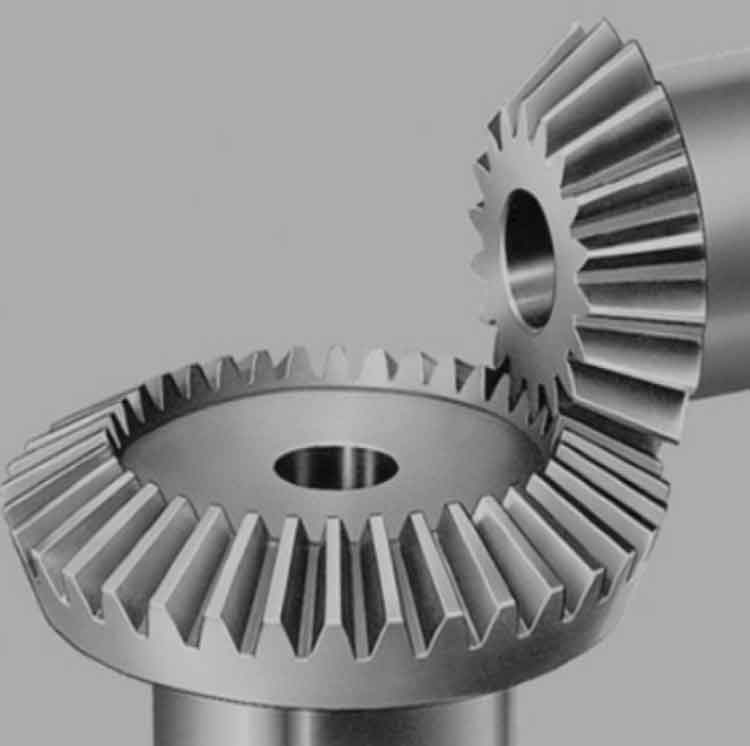
Advancements in straight bevel gear cutting technology have led to more precise and efficient manufacturing processes, resulting in higher-quality gears with improved performance characteristics. These advancements have been driven by developments in machining techniques, cutting tools, and computer-aided manufacturing (CAM) software. Here are some notable advancements in straight bevel gear cutting technology:
1. CNC Gear Cutting Machines:
- Computer Numerical Control (CNC) gear cutting machines have revolutionized gear manufacturing.
- CNC machines offer higher accuracy, repeatability, and flexibility in gear cutting, allowing for complex gear designs and tight tolerances.
2. Multi-Axis Machining:
- Multi-axis machining centers can perform simultaneous cutting operations on multiple surfaces of the gear blank.
- This capability allows for more efficient gear cutting and reduces setup times.
3. Five-Axis Machining:
- Five-axis machining allows for the cutting tool to move along five axes, offering greater flexibility in gear manufacturing.
- This technology is particularly beneficial for producing spiral bevel gears and complex gear shapes.
4. High-Speed Cutting (HSC) Technology:
- HSC technology enables faster cutting speeds, reducing cycle times and increasing productivity.
- It also helps to minimize tool wear and improve surface finish.
5. High-Precision Grinding:
- Grinding processes have become more precise, allowing for improved gear tooth surface finish and reduced tooth profile deviations.
- This results in quieter and more efficient gear operation.
6. Advanced Cutting Tools:
- The development of high-performance cutting tools, such as carbide and ceramic tools, has improved the efficiency and tool life in gear cutting.
- Coated cutting tools with improved wear resistance contribute to longer tool life and reduced production costs.
7. Dry Cutting Technology:
- Dry cutting, or minimal lubrication cutting, is becoming more popular due to environmental considerations and reduced lubricant usage.
- Advanced coatings on cutting tools facilitate dry cutting while maintaining tool life and productivity.
8. Simulation and CAM Software:
- CAM software allows for comprehensive simulation and optimization of the gear cutting process.
- Virtual simulations help identify potential issues and optimize cutting parameters before physical machining, reducing scrap and setup times.
9. In-Process Measurement and Control:
- Real-time in-process measurement and control systems provide feedback during gear cutting, ensuring accuracy and detecting any deviations promptly.
10. Automation and Robotics:
- Automation and robotics are increasingly integrated into gear cutting processes to improve productivity and reduce manual intervention.
These advancements in straight bevel gear cutting technology have not only improved the manufacturing process but also resulted in gears with higher precision, better surface finish, and enhanced overall performance. Manufacturers can now produce straight bevel gears more efficiently, meeting the increasing demands of various industries while maintaining high quality and cost-effectiveness.