Advancements in straight bevel gear manufacturing have significantly improved precision and quality in recent years. These advancements can be attributed to several factors, including technological innovations, improved machining techniques, and enhanced quality control measures. Let’s explore some of the key developments in this field:
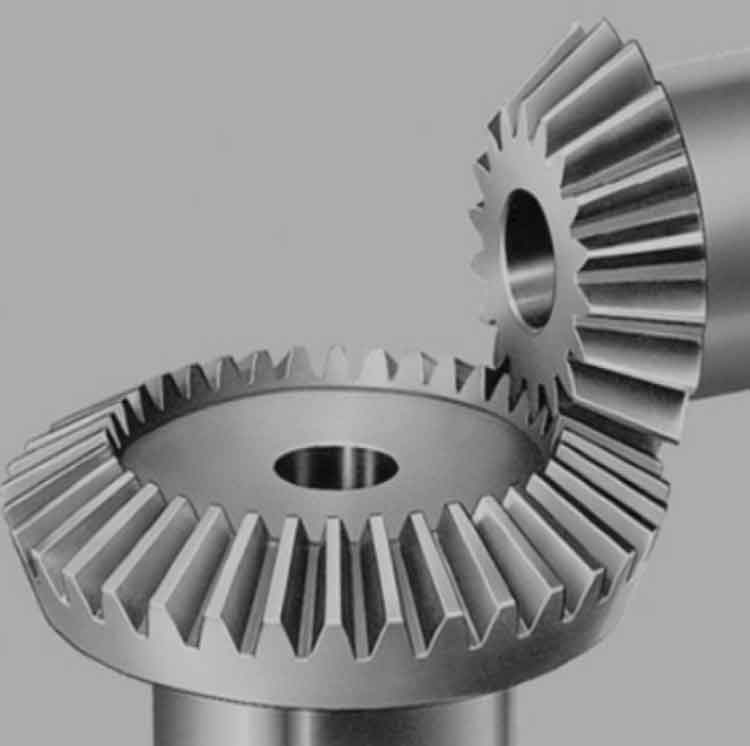
- Computer-Aided Design and Manufacturing (CAD/CAM): The integration of CAD/CAM systems has revolutionized gear design and production. These software tools allow engineers to create highly precise gear geometries and simulate their performance under different operating conditions. By optimizing the gear design in a virtual environment, manufacturers can achieve better accuracy and minimize potential errors during the manufacturing process.
- High-precision machining equipment: The availability of advanced machining equipment, such as multi-axis CNC (Computer Numerical Control) machines, has greatly enhanced the precision of bevel gear manufacturing. These machines offer high repeatability and allow for complex machining operations with tight tolerances. Additionally, the use of innovative cutting tools, including carbide and ceramic inserts, has improved the surface finish and dimensional accuracy of gears.
- Improved gear cutting methods: Traditional methods like face milling and hobbing have been refined and augmented with newer techniques. For instance, advanced gear shaping and gear grinding methods have gained prominence. Gear shaping involves generating gear teeth using specialized cutting tools, resulting in accurate tooth profiles and reduced noise levels. Gear grinding, on the other hand, employs abrasive wheels to achieve high surface finish and precise tooth dimensions.
- Heat treatment advancements: Heat treatment plays a crucial role in enhancing the strength and durability of gears. Advancements in heat treatment processes, such as carburizing, quenching, and tempering, have led to improved hardness, wear resistance, and case depth control in straight bevel gears. Modern techniques like induction hardening and laser hardening offer localized heat treatment, allowing manufacturers to optimize the gear’s mechanical properties.
- Advanced metrology and quality control: Quality control measures have become more sophisticated with the introduction of advanced metrology equipment. Coordinate measuring machines (CMMs), optical profilometers, and 3D scanners enable precise measurement and inspection of gear geometries, tooth profiles, and surface finish. This helps manufacturers detect and correct any deviations from the desired specifications, ensuring high-quality bevel gears.
- Material advancements: The development of new materials, such as advanced alloys and composites, has expanded the possibilities for bevel gear manufacturing. These materials offer improved strength-to-weight ratios, higher wear resistance, and reduced friction, resulting in enhanced gear performance and longevity.
- Simulation and virtual prototyping: Computer simulations and virtual prototyping have become invaluable tools in the design and development of bevel gears. Finite Element Analysis (FEA) and other simulation techniques allow engineers to assess gear performance, optimize designs, and predict potential failures before physical prototypes are produced. This reduces the time and cost associated with iterative testing and enables manufacturers to deliver high-precision gears.
Advancements in straight bevel gear manufacturing have significantly improved precision and quality through the integration of CAD/CAM systems, high-precision machining equipment, improved cutting methods, heat treatment innovations, advanced metrology, material advancements, and virtual prototyping. These developments have paved the way for more reliable, efficient, and durable bevel gears used in a wide range of applications, including automotive, aerospace, industrial machinery, and more.