Gear hobbing offers several advantages that make it a preferred method for gear manufacturing. These advantages include efficiency, accuracy, versatility, and cost-effectiveness. Let’s delve into the key advantages of gear hobbing:
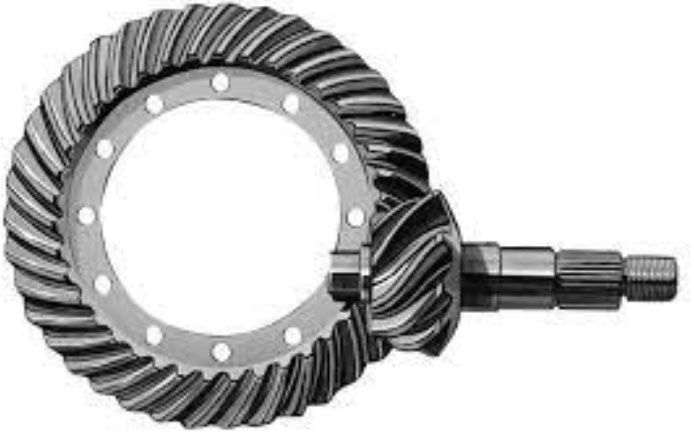
1. Efficiency in Mass Production:
Gear hobbing is a highly efficient process, particularly when producing a large quantity of gears with the same specifications. It allows for continuous cutting, minimizing downtime between gears, and facilitating high-volume production.
2. High Accuracy and Precision:
Gear hobbing provides excellent accuracy and precision in the produced gears. The use of CNC-controlled machines ensures consistent tooth profiles and dimensions, resulting in gears with tight tolerances and reliable performance.
3. Versatility in Gear Types:
Gear hobbing can manufacture various types of gears, such as spur gears, helical gears, worm gears, bevel gears, and more. It allows for the creation of gears with different tooth profiles and helix angles to suit specific application requirements.
4. Smooth Tooth Profiles:
Gears produced by hobbing have smooth tooth profiles due to the continuous cutting action of the hob. This results in gears with excellent meshing characteristics and reduced noise during operation.
5. Excellent Surface Finish:
Gear hobbing typically produces gears with a fine surface finish, reducing the need for additional finishing operations. This contributes to the overall efficiency of the gear manufacturing process.
6. Cost-Effectiveness:
For mass production, gear hobbing is cost-effective compared to other gear manufacturing methods. It offers a higher production rate, reduced tooling costs, and improved material utilization.
7. Consistent Gear Quality:
Gear hobbing ensures consistency and repeatability in gear production, reducing the risk of dimensional variations and ensuring consistent gear quality from one production batch to another.
8. Reduced Secondary Operations:
The gear hobbing process often produces gears with such high precision that secondary finishing operations may be minimal or unnecessary, saving time and cost in the production process.
9. High Load-Carrying Capacity:
Gears manufactured by hobbing exhibit excellent load-carrying capacity due to their accurate tooth geometry, making them suitable for heavy-duty applications.
10. Wide Range of Materials:
Gear hobbing can work with a wide range of materials, including various steels, alloys, and non-ferrous metals, allowing for the selection of the most suitable material for specific application requirements.
The efficiency and accuracy of gear hobbing, coupled with its versatility and ability to produce high-quality gears with various tooth profiles, make it an essential and widely used method in modern gear manufacturing. It meets the demands of various industries, including automotive, aerospace, machinery, robotics, and more, where precision and reliability are paramount in gear applications.