Abstract
Beveloid gears, as a general form of involute gears, feature a variable modification coefficient along the gear axis, enabling transmissions with parallel, intersecting, and staggered axes. Due to their spiral involute tooth surface, beveloid gears can mesh with various types of involute gears in different working environments. This adaptability and the ability to achieve precision transmission through axial movement make beveloid gears advantageous in precise transmission fields where backlash requirements are stringent. However, research on the strength calculation and life prediction of beveloid gears is still immature. This paper focuses on parallel-axis beveloid spur gears, leveraging fractal contact theory, Hertz contact theory, cumulative damage theory, gear meshing principles, and fatigue life theory to study their related parameters, tooth surface equations, meshing efficiency, mathematical models, contact strength, fatigue life, and fatigue damage. The research results provide a theoretical basis for the practical application and development of beveloid gears.
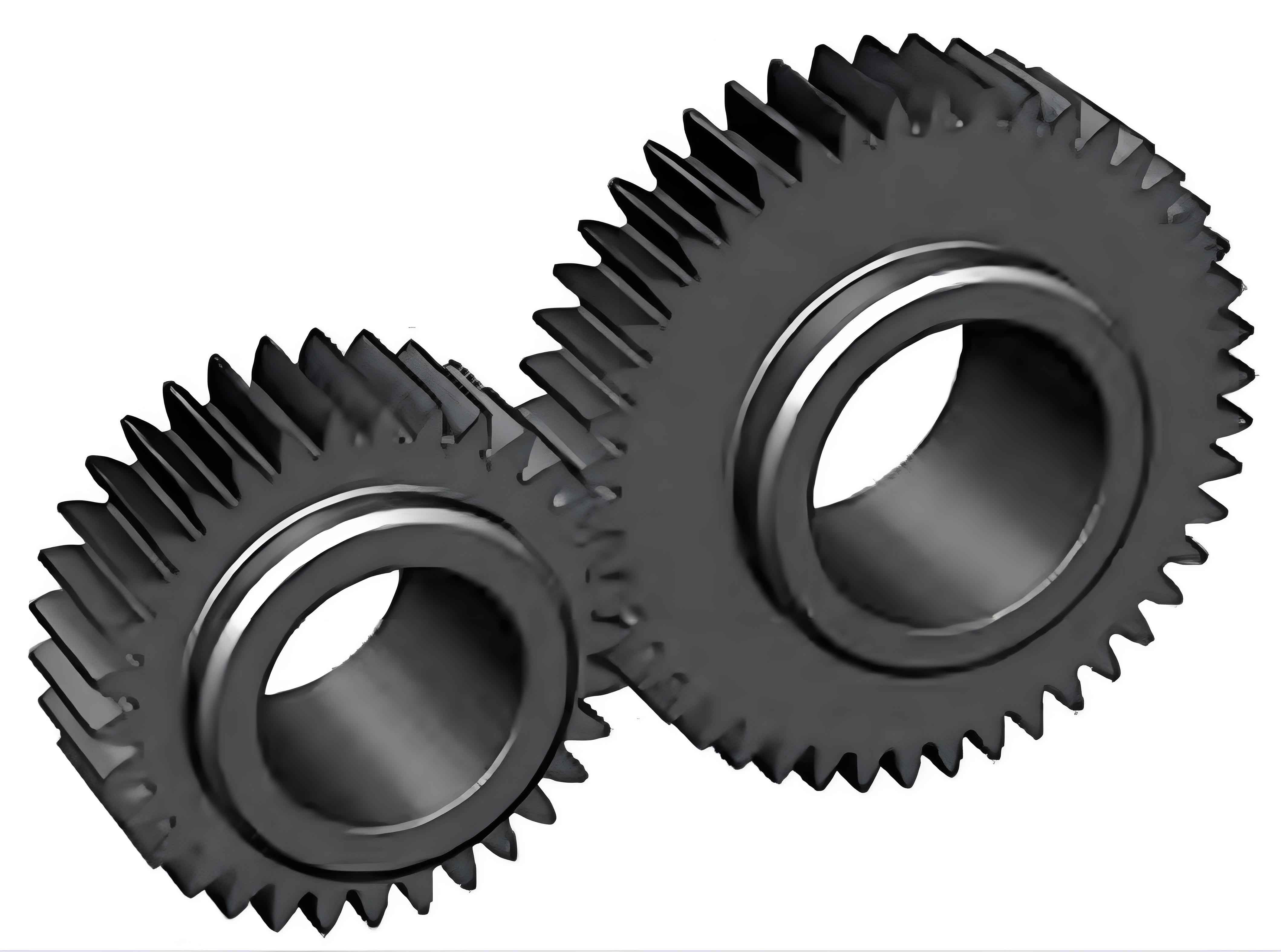
1. Introduction
1.1 Research Background and Significance
Gear transmission is one of the most widely used mechanical transmission methods, offering advantages such as wide power transmission range, high transmission accuracy, and constant instantaneous transmission ratio. It plays a crucial role in modern industry, finding applications in automobiles, engineering machinery, and shipbuilding. With the development of social economy and advancements in science and technology, China has set higher requirements for the mechanical manufacturing industry. As a key component in the manufacturing process, the performance of gear transmission systems directly impacts product quality and production efficiency. To better promote the rapid development of related industries, it is necessary to further optimize the design and manufacturing processes of gear systems.
Beveloid gears exhibit a linearly varying modification coefficient along the gear axis, theoretically allowing their axes to form any angle. Compared to bevel gears, beveloid gears can achieve transmission between any two shafts in space, and their grinding process is relatively simple and cost-effective. Beveloid gears come in three transmission types: intersecting-axis, staggered-axis, and parallel-axis. Parallel-axis beveloid gears can adjust the gear backlash without changing the center distance, enabling precise transmission with minimal backlash and reducing vibration and noise during operation.
Beveloid gears can mesh with most involute gears, such as spur gears, helical gears, and racks, satisfying different design requirements and compensating for the deficiencies in beveloid gear pair meshing. Moreover, beveloid gears are easier to manufacture and do not require specialized machinery. These advantages have led to their widespread application in robots and all-wheel-drive vehicles. In recent years, modern industrial production has placed high demands on gear transmissions, including long service life, smooth transmission, and high load-bearing capacity. To meet these demands, in addition to selecting high-hardness materials, improving gear processing accuracy, and refining heat treatment processes, it is also necessary to ensure that the designed gears meet operational requirements. To avoid plastic deformation, pitting, and other damages caused by insufficient contact strength, the allowable stress value must always exceed the gear contact stress. Therefore, conducting research on the basic theories, strength calculation theories, and life prediction of beveloid gear pairs is of great significance for optimizing their structural design, improving transmission performance, enhancing gear life, and increasing load-bearing capacity.
1.2 Research Status of Beveloid Gears
Beveloid gears, also known as conical gears, have a history dating back to the mid-20th century. Since Merrit and Beam proposed the theory of beveloid gears, scholars at home and abroad have conducted extensive research on their geometric design, manufacturing, and meshing theories. Purkiss defined the geometric characteristics of beveloid gear tooth profiles and processed beveloid gears using ordinary cylindrical gear cutting equipment by adjusting the relative motion between the cutter and the gear blank. In the 1980s, Mitome derived the tooth surface equation of beveloid gears based on gear meshing principles and designed a rack cutter specifically for beveloid gear processing. Lu Jiechi et al. built a microcomputer numerically controlled hobbing machine capable of processing beveloid gears by adding a single-board computer, drive power supply, and pulse generator to a Y31125E hobbing machine, using it to process three different types of beveloid gears. In the 1990s, Xu Feng et al. solved for the conditions to prevent undercutting of tooth roots, tooth tip thinning, and gear interference in intersecting-axis beveloid gears and analyzed the tooth profile errors caused by shaft intersection during meshing.
After the 21st century, Zhu et al. analyzed the sensitivity of the contact path direction (FPD angle) between the principal curvatures of tooth surfaces, meshing characteristics, and dynamic responses to assembly errors when installing intersecting-axis beveloid gears. Li et al. calculated the tooth profile errors and axial errors of beveloid gears through numerical analysis and established a model of non-involute beveloid gears based on the solution results. Cao proposed an adaptive design model for continuously generating beveloid gears on an ordinary gear grinding machine, established an analytical meshing model for the grinding contact trajectory, and analyzed the influence of worm and dresser parameters on grinding deviations. Wang Guangjian et al. applied beveloid gears to a new type of double-crank planetary reducer, optimized the calculation of the gear modification coefficient, conducted mechanical analysis of planetary gears and trunnion bearings, and obtained the influence of the trunnion bearing center distance on the load and the influence of the crankshaft axial dimension. Mao Hancheng et al. established a time-varying meshing stiffness calculation model for beveloid gears considering tooth profile modifications and compared and analyzed the gear time-varying meshing stiffness obtained through numerical and finite element methods. Wang Xin et al. applied beveloid gear pairs to RV reducers, enabling the reducer to automatically adjust the backlash to the optimal state, and analyzed the influence of tooth number, pitch cone angle, and meshing angle on transmission efficiency. Chen Yan et al. established a mathematical model for beveloid gear enveloping hourglass worm pairs, analyzed the variation of contact lines and contact areas with spiral angle, normal module, pressure angle, and transmission ratio, and the influence of these parameters on lubrication angle and entrainment speed. Mao et al. proposed a slice grouping method based on potential energy, considering tooth surface roughness, to calculate the meshing stiffness of gears and used the finite element method and slice grouping method to compare and analyze the variation of meshing stiffness under different parameters. He et al. realized parametric modeling of involute and non-involute beveloid gears, analyzed the dynamic contact characteristics of involute and non-involute helical gear pairs during meshing cycles, and studied the dynamic contact stress contour and single-tooth contact stress. Lin et al. developed a parametric modeling program for beveloid helical gears based on their tooth surface equations, established a solid model of the gear, and used the finite element method to analyze the dynamic contact stress, dynamic stress distribution, and dynamic transmission error of intersecting-axis beveloid gears.
In summary, scholars at home and abroad have conducted in-depth research on the tooth surface equations, geometric design, manufacturing, contact analysis, and dynamic simulation of beveloid gears. This research provides a theoretical basis for the parametric design of beveloid gears in this paper. However, in the existing analysis of beveloid gear contact characteristics, the finite element simulation method is commonly used, which has a long calculation period and results that are heavily influenced by subjective factors.
1.3 Research Status of Tooth Surface Contact Stress
Over the years, a relatively complete system of strength analysis theories and calculation methods for cylindrical gears has been established. Currently, common methods for calculating tooth surface contact stress include the Hertz contact model calculation method, fractal contact model calculation method, finite element calculation method, and experimental analysis method. However, in the study of beveloid gear contact strength, most research uses the finite element method for solutions. Research on the contact stress of beveloid gears based on analytical methods is rarely involved.
1.3.1 Research Status of Finite Element Contact
Ma Hui et al. established an analysis model for the meshing characteristics of gear pairs with tooth profile modifications considering drum-like modifications and analyzed the contact stress of the ideal contact state and the gear pair with drum-like modifications, verifying the accuracy of the mathematical model and optimizing the gear modification amount. Bharat et al. studied the contact stress of spur gears with different modules using the finite element method and compared the results with those obtained using the Hertz contact stress calculation formula. Peng Xianlong et al. established a face gear model with installation errors using the coordinates of discrete points on the gear tooth surface and analyzed the contact path, tooth surface contact stress, and load transmission error of the model. Putti et al. established two-dimensional finite element models of spur gears made of structural steel, gray cast iron, and aluminum under different combination conditions and compared the contact stresses obtained with those calculated using the Hertz contact model, verifying the feasibility of the two-dimensional finite element model. Perez et al. proposed a new finite element model for gear stress analysis, applying Hertz theory to arc bevel gear transmissions with local bearing contact, and validated the model by observing the convergence of contact stress and bending stress. Liu Xiaobai et al. analyzed the stress nephogram and contact pattern of arc bevel gear models and calculated the load transmission error curves of gear pairs under different working conditions. Chen et al. used the finite element method to solve the contact stress of non-parallel-axis beveloid gear pairs and analyzed the distribution of tooth surface contact stress and the influence of grinding wheels with different radii on the contact stress of gear pairs. Liu et al. established a mathematical model of a small-angle beveloid spur gear pair, including working tooth surfaces and transition tooth surfaces, based on the basic theory and generation mechanism of gears, calculated the stress distribution on the tooth surface, and conducted stress analysis on gear pairs with different design parameters.
The finite element calculation method is widely used in theoretical research. Different meshing conditions can be established using finite elements to accurately obtain gear stress, strain, meshing stiffness, etc., and the model can be topologically optimized. Although finite element simulation can solve complex parts and assemblies, the results obtained are closely related to mesh division and boundary condition settings, leading to unstable results. Additionally, finite element solutions require a significant amount of time and are inconvenient for practical applications.
1.3.2 Research Status of Hertz Contact
Hertz’s elastic contact theory is the most widely used stress analysis method. In the 1880s, Hertz studied the deformation and contact of elastic bodies under normal loads and verified the load distribution on the contact area through experiments. Zhang et al. derived the meshing equation for line-contact curved cylindrical gears under different assembly conditions, analyzed the variation of contact stress and bending stress in gears, and discussed the contact stress issues caused by edge contact. Hu Xiaxia et al. studied the contact model and contact stress of spur gears based on Hertz contact theory, simulated the formation process of the gear’s composite curvature curve through simulation analysis, and performed theoretical calculations and finite element simulations of the contact stress of spur gears. Liu et al. studied the tooth profile modification of cycloid pinwheel reducers based on non-Hertz elastic contact theory, proposed a non-Hertz flexibility matrix analysis method for tooth surface contact, and verified the analysis results of the non-Hertz flexibility matrix method (NHFMM) through photoelastic tests. Yan et al. proposed a method for dynamically adjusting tooth width to optimize the uneven load distribution of helical gears. By studying the dynamic tooth width modification, the dynamic load distribution on the tooth surface became more uniform, reducing the wobble phenomenon. Wang Yuda et al. simplified the tooth surface meshing into the contact of cylinders, analyzed the tooth surface curvature and load distribution coefficient during conjugation of this model, and used Hertz’s principle to solve the contact stress, elastic deformation, and transmission error of gears. Wei Jing et al. created a stress calculation model for planetary gear systems based on the modified Heywood formula and Hertz formula and analyzed the variation of dynamic contact stress under different poses of the transmission system. Li et al. established a calculation formula for the meshing contact stress of spiral bevel gears based on Hertz contact theory and compared the relative error rate of the angular velocity and the relative error rate of the tangential component of the contact force between simulation and theoretical calculations. Xiang et al. established calculation formulas and parameter sets for the contact force of conventional spiral bevel gears and logarithmic spiral bevel gears based on Hertz’s elastic contact theory, simulated the meshing angular velocity and tangential contact stress of the two types of spiral bevel gears, and analyzed the fluctuations in the meshing angular velocity and tangential contact force of the gears. Zhao Jun verified the tooth surface contact strength of staggered-axis beveloid helical gear pairs with small shaft angles in a marine gearbox using Hertz point contact theory and conjugate surface theory, validated the theoretical calculation results using a finite element model, and analyzed the dynamic meshing performance and fatigue life of the gear pair based on the finite element results. Rong Junsong analyzed the shear stress and equivalent stress of a beveloid gear planetary transmission system with different lubricant coatings using Hertz contact theory and solved for the most suitable oil film thickness for the microgravity environment. Sun et al. derived a formula for checking the contact strength of circular arc tooth trace cylindrical gears based on Hertz contact theory, used computer simulations to compare and analyze the contact strength between circular arc tooth trace cylindrical gears, spur gears, and helical gears, and conducted a case study on a circular arc tooth trace cylindrical gear reducer.
The Hertz contact stress calculation formula is the most commonly used method for gear strength verification. Currently, when calculating the theoretical contact stress of cylindrical spur gears and beveloid gears, the traditional Hertz formula is generally used. This method has high accuracy for ordinary spur gears. However, in the strength verification of beveloid gears, researchers typically rely on the parameters or small-end parameters of the mid-cross-section of the gear pair and use the traditional Hertz contact stress calculation formula for solutions. This method treats beveloid gears as cylindrical spur gears with special parameters and can only simply calculate the gear contact stress under different tooth numbers, modules, and pressure angles. It cannot calculate the gear contact stress under different pitch cone angles and tooth form angles, resulting in low calculation accuracy. Therefore, it is necessary to derive a contact stress calculation method applicable to beveloid gears.
1.3.3 Research Status of Fractal Contact
Fractal theory, as a new mathematical tool, provides a new approach for research in the field of gear transmission. Based on fractal theory, researchers have conducted extensive research on gear surface topography, normal stiffness, time-varying meshing stiffness, contact characteristics, and other aspects.
Fractal theory dates back to the 1950s when Mandelbrot proposed it while studying the British coastline. Majumdar et al. established the M-B fractal contact model based on the W-M function, which reflects the relationship between the load on micro-asperities and the real contact area at the microscopic level. Wang et al. assumed Hertzian contact of micro-asperities in the fractal contact model, analyzed the frictional temperature rise of rough surface micro-asperities, and determined the distribution density function of the temperature rise in the real contact area. Huang Kang et al. introduced a surface contact coefficient to establish a fractal contact model for two cylinders, comparing and analyzing the contact strength of this model and the Hertz contact model under different curvature radii. Ge Shirong et al. evaluated four methods for calculating the fractal dimension of rough surface profiles and proposed a theoretical method for calculating the fractal dimension using the covariance weighting method. Chen Qi et al. established a fractal contact model for calculating the contact stress of two elastic spheres, analyzing the relationship between the load borne by the spheres and the real contact area. Yang Rongsong et al. proposed a fractal contact model considering the friction coefficient, simulated the surface topography of cycloid pinwheels, and analyzed the changes in the real contact area and critical contact area of gears under different parameters. Wang Xiaopeng et al. established a fractal contact model for micro-pitted gears, studied the surface topography, normal contact stiffness, and normal load of micro-pitted gears, and explored the influence of microscopic elements on gear contact characteristics. Chen Yong et al. obtained the variation law of friction factors on the surface of automobile transmission gears with and without coatings using an SRV friction and wear tester, measured the surface topography characteristics of transmission gears after fatigue testing with and without coatings, and finally solved for the contact stress of transmission gears using fractal and finite element models. Yu et al. established a 3-DOF lateral-torsional dynamic model considering the rough surface topography of spur gears, solved for the expression of backlash and time-varying stiffness, and analyzed the dynamic response of the gear system relative to the fractal dimension and fractal roughness. Yang et al. considered the deformation characteristics of micro-asperities, tooth surface contact coefficients, and the influence of sliding friction to establish a fractal model for the normal contact stress of double-arc helical gears, studied the influence of fractal dimension, surface roughness amplitude, and friction coefficient on the fractal contact model, and compared and analyzed the tooth surface contact stress obtained from the fractal model, experimental measurements, and traditional formulas. Yu et al. proposed a point contact area distribution function and established a fractal contact mechanics model for the rough surface of elliptic bevel gears, studying the influence of different fractal parameters on the contact load and contact stiffness of the tooth surface. Li et al. established a gear-bearing system considering tooth surface friction, time-varying meshing stiffness, backlash, and other factors, solved for tooth surface wear based on fractal theory and Archard theory, solved for time-varying backlash and time-varying meshing stiffness based on the wear amount of rough topography, and analyzed the influence of different parameters on the dynamic characteristics of the gear-bearing system.
Hertz contact theory is mainly applied to smooth contact surfaces without relative sliding, reflecting the tooth surface contact stress only at the macro level. Due to the influence of factors such as processing technology and roughness on the contact surface, the contact surface is not smooth. The stress values obtained using Hertz contact theory have certain errors, and the Hertz contact model cannot solve the contact stress of gear pairs with the same curvature. Therefore, applying fractal theory to the analysis of gear contact strength is of positive significance.
In summary, scholars at home and abroad have used different methods to analyze the contact strength of gears. However, the analysis of the contact strength of beveloid gears mainly stays within the finite element method and the traditional Hertz contact model. The contact strength theory of beveloid gears still needs further research. Based on existing gear carrying capacity research theories and calculation methods, this paper considers the characteristics of the geometric structure of beveloid gears, derives the calculation method for the contact strength of parallel-axis beveloid spur gears, and explores the gear contact mechanism, providing a theoretical basis for the design and application of involute beveloid gears.
1.4 Research Status of Gear Fatigue Life
Fatigue life refers to the process in which a material experiences permanent cumulative damage at one or more locations after repeated cycles, eventually leading to crack formation or complete fracture at the damaged location. In the early 19th century, with the popularization of steam equipment, transmission component failures frequently occurred. Researchers conducted extensive research on the causes of fatigue failure and methods to improve fatigue strength. Since then, fatigue life analysis of gears has become an important research area in mechanical engineering.
Research on gear fatigue life has made significant progress over the years. Various methods and theories have been proposed to predict and analyze the fatigue life of gears. These include theoretical models, experimental studies, and numerical simulations. For instance, Liu et al. [60] developed a numerical model that considered factors such as lubrication conditions, tooth surface roughness, residual stresses, and material mechanical properties to analyze the contact stress distribution and fatigue life of gears. Cao et al. [61] proposed a new friction dynamics model for spiral bevel gears, which enabled the simulation of fatigue life considering complex gear contact geometries and actual machined surface roughness.
Researchers have also explored the effects of different parameters on gear fatigue life. For example, Hu et al. [62] compared the fatigue life of spur gears under elastohydrodynamic lubrication with that predicted by Hertz contact fatigue theory and standard methods. Wang et al. [63] analyzed the equivalent stress and contact pressure of a gear pair under multiple operating conditions and established a multi-condition combined fatigue analysis model to predict the strength and fatigue life of transmission gears under variable loads.
In addition, experimental studies have played a crucial role in validating and improving fatigue life prediction models. Zhou et al. [64] proposed a fatigue life calculation method based on scale parameters, shape parameters, and location parameters, and experimentally verified the method using a mechanical power flow closed gear test rig. Chen et al. [65] established a two-dimensional finite element model to analyze the contact fatigue of gears and studied the distribution of maximum contact pressure and grain boundary damage.
Recent studies have focused on the application of advanced numerical simulation techniques, such as finite element analysis (FEA), to predict gear fatigue life. You et al. [66] used white light interferometry to measure the rough surface of test gears and established a rough finite element model to analyze the effects of residual stress on contact stress, fatigue life distribution, and near-surface and subsurface contact fatigue.
However, research on the fatigue life of beveloid gears, a specific type of gear with variable tooth thickness, is still relatively scarce. The unique geometric characteristics and transmission properties of beveloid gears pose additional challenges for fatigue life analysis. Therefore, further research is needed to develop accurate and reliable fatigue life prediction models for beveloid gears, considering their specific design parameters and operating conditions.
In summary, fatigue life analysis of gears has been an active area of research for over two centuries, with significant advancements in theoretical models, experimental studies, and numerical simulations. However, there is still room for improvement, especially for gears with unique geometric features such as beveloid gears. Future research should focus on developing comprehensive fatigue life prediction models that account for the specific characteristics and operating conditions of these gears.