In the gear transmission mechanism of complex power equipment, the gear shaft and the bearing are assembled by interference, so the gear shaft and the shaft bear the same torque so that they can operate at the same speed. However, the gear shaft is affected by the periodic gear meshing force in the operation process, which causes the micro torsional vibration between the gear shoulder and the bearing. In order to simplify the complex problem, it is assumed that the bearing is stationary relative to the gear shaft, and the gear shaft shoulder is micro torsional vibration relative to the bearing, and the torque load it receives is the torque increment generated during the operation of the gear shaft. The gear shaft is simplified as an elastic part with mass m, moment of inertia I and diameter D. the torque increment of the gear shaft is Δ TT, as shown in the figure.
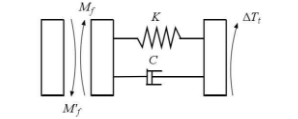
At the same time, there is friction between the gear shoulder and the bearing inner race, resulting in friction moment MF as shown in Figure 2. It is assumed that the rotation direction of the gear shaft is always clockwise. Therefore, the fretting friction between the gear shoulder and the bearing inner race mainly depends on the opposite angle θ between the gear shaft and the bearing inner race.
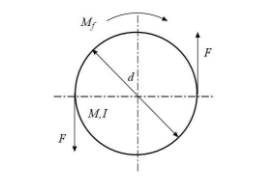
In order to study the problem conveniently, the simplified physical model as shown in Figure 1 is used to explain the physical essence of the micro torsional vibration phenomenon of the gear shaft shoulder. It is assumed that the bearing is stationary relative to the gear shaft, and the gear shaft rotates clockwise relative to the bearing under the alternating load of gear mesh. Suppose that the transmission between two objects is a spring, its torsional stiffness is k, and the viscous torsional damping between the friction surface and the transmission is set to C. When the gear shaft slowly pushes the bearing to the right, the spring is compressed and energy is stored at the same time. The spring driving torque and static friction torque act on the gear shaft together. In many friction systems, friction moment is divided into static friction moment and dynamic friction moment. In this friction system, it is assumed that the two friction moments composed of the maximum static friction and the dynamic friction are not equal, and usually the maximum static friction moment is greater than the dynamic friction moment.
As the gear shaft continues to move, the amount of spring compression increases, and the spring resistance torque of the gear shaft also increases. When the external force on the gear shaft is enough to overcome the maximum static friction moment, the gear shaft starts to rotate clockwise. At this time, because of the speed, the static friction moment will quickly convert into the dynamic friction moment, so the friction moment will rapidly decline. Then, due to the friction resistance moment, inertia moment and rotational damping moment of the bearing, the relative speed of the gear shaft decreases gradually, and the gear shaft slows down until it stops. After that, the gear shaft moves in the opposite direction under the action of the opposite moment.
As the alternating load of gear mesh causes the transmission torque of gear shaft to fluctuate, it is assumed that the fluctuation of transmission torque is the torque increment Δ TT of gear shaft relative to bearing. If the torsional stiffness and damping of the gear shaft have the process of repeated energy storage and release, the gear shaft will do the reciprocating motion of repeated acceleration and deceleration relative to the bearing. In this way, the “adhesion sliding” and “sliding adhesion” repeatedly make the gear shaft shoulder present a micro torsional vibration phenomenon relative to the bearing, which is the motion mechanism of the micro torsional vibration of the gear shaft shoulder.
When the relative speed between the gear shaft and the bearing is zero, this state is defined as the relative static state of the gear shaft and the bearing; when the gear shaft is meshed by the gear, it will produce small rotation relative to the bearing, and this state is defined as the relative motion state of the gear shaft and the bearing.