The load conditions of the gear assembly mainly include three aspects: the pre tightening torque applied on the tightening nut, the alternating load of the gear engagement and the friction produced by the gear shaft interference assembly. The following analysis is made on the influence of the pre tightening torque of the gear shaft end nut, the transmission power of the gear shaft, the interference between the gear shaft and the bearing mating surface and the friction factor on the force of the gear shaft shoulder. It can be seen from the figure that the contact stress of the gear shaft shoulder is the largest when the gear mesh axis and the top of the shaft shoulder are located. Therefore, when the contact stress of the gear shaft shoulder is affected by various main factors, the contact stress at this place is taken as the research object.
(1) Influence of preloading moment on stress σ C of gear shoulder
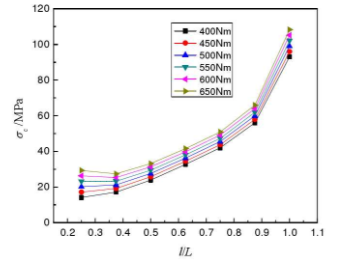
The change rule of the contact stress σ C of the gear shaft shoulder under different pre tightening torque of the nut is shown in the figure:
The preload of the gear shaft is achieved by applying the preload torque to the nut at the shaft end, so the preload torque is used to represent the preload of the gear shaft. It can be seen from the figure that the contact stress of the gear shoulder gradually increases from the bottom to the top of the gear shoulder; at the same shoulder height, the contact stress of each node of the gear shoulder also increases with the increase of the preloading moment. When the preloading moment is 400N · m, the contact stress at the top of the shoulder is 93.01mpa, while when the preloading moment is 650n · m, the contact stress at the top of the gear shoulder is 108.21mpa. It can be seen that the contact stress of the preloading moment on the gear shaft shoulder is obvious.
(2) The influence of interference on the force σ C of gear shoulder
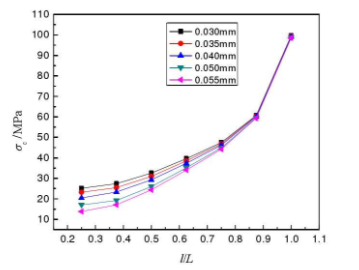
As shown in the figure, the change rule of the contact stress of the gear shaft shoulder under different interference is shown. In the case of a certain amount of interference, the contact stress of the gear shaft shoulder increases gradually from the bottom to the top of the shaft shoulder: when the interference is 0.030mm, the contact stress is 25.16mpa and 99.67mpa when the relative height of the shaft shoulder is 0.25 and 1 respectively; when the interference is 0.055mm, the contact stress is 13.77mpa and 98.61mpa when the relative height of the shaft shoulder is 0.25 and 1 respectively. Therefore, the influence of the interference on the contact stress of the shoulder is obvious: when the height of the shoulder is low, the contact stress of the shoulder decreases with the increase of the interference; while when the height of the shoulder is low, the contact stress of the shoulder hardly changes with the change of the interference.
(3) The influence of transmission power on the stress σ C of gear shoulder
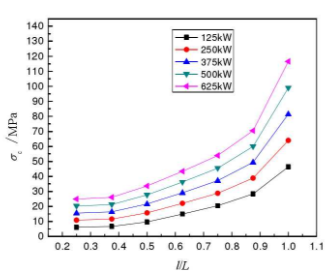
Transmission power is one of the important external loads on the gear assembly. In the study of the influence of transmission power on the fretting wear of the shaft shoulder, the influence of transmission power on the contact stress of the shaft shoulder is mainly analyzed. Simultaneous interpreting the actual working conditions of gear components, the different transfer power is selected to analyze the variation law of the force and deformation of the gear shaft shoulder. Simultaneous interpreting of the contact stress curves of the gear shaft under different transmission power is shown.
It can be seen from the figure that the contact stress of the gear shaft shoulder increases gradually from the bottom to the top of the shaft shoulder when the transmission power is 500kW, when the relative height of the gear shaft shoulder is 0.25, the contact stress is 20.21 MPa, and when the relative height of the gear shaft shoulder is 1, the contact stress is 99 MPa; at the same height of the gear shoulder, the contact stress of the gear shoulder increases with the increase of the transmission power: when the transmission torque is 125KW, the contact stress at the top of the gear shoulder is 46.38mpa; when the transmission torque is 625kw, the contact stress at the top of the gear shoulder is 116.54mpa. It can be seen that during the operation of the gear shaft, the greater the transmission power is, the greater the meshing force of the gear is, and the greater the bending deformation of the gear shaft is.
(4) The effect of friction factor on the force σ C of gear shoulder
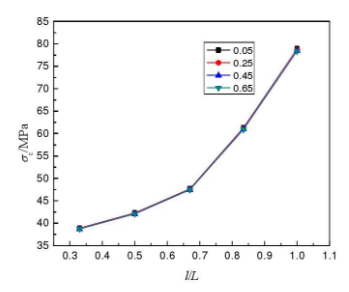
In order to get the influence of the friction coefficient between the gear shaft and the bearing on the contact stress of the gear shaft shoulder, the change rule of the contact stress of the gear shaft shoulder under the action of different friction coefficient is compared by the numerical simulation method, as shown in the figure.
It can be seen from the figure that when the friction coefficient between the gear shaft and the bearing is fixed, the contact stress of the gear shaft shoulder increases gradually from the bottom to the top of the shaft shoulder: when the friction coefficient is 0.25, the contact stress of the gear shaft shoulder increases from 38.79mpa at the bottom to 78.64mpa at the top of the shaft shoulder. At the same shoulder height, the contact stress of the shoulder decreases with the increase of the friction factor, but the degree of reduction is not obvious: when the friction factor is 0.05, the contact stress of the top of the shoulder is 78.96mpa; when the friction factor is 0.45, the contact stress of the top of the shoulder is 78.47mpa. It can be seen that the influence of friction coefficient on the change of contact stress of shaft shoulder is not obvious.