Mode (including natural frequency and mode) is the inherent property of multi degree of freedom system. It describes the natural vibration characteristics of the system from two aspects of time history and spatial deformation mode, which determines the response characteristics of the system to various dynamic excitations. There are many transmission elements in shearer’s cutting part. Under the combined action of internal and external excitation, the vibration and deformation of shearer’s cutting part are more complex. The analysis of its natural vibration characteristics is helpful to understand the dynamic response of the system.
At present, the analysis of natural vibration characteristics of gearbox is mainly focused on single component of gearbox, which can not well simulate the actual characteristics of gearbox assembly conditions. In order to deeply understand the natural vibration characteristics of shearer’s cutting part, the natural vibration characteristics of rocker box and multi-stage gear transmission are studied respectively, and then the natural vibration characteristics after coupling are studied.
The finite element model of the rocker box is established, and the Craig Bampton modal transformation program is written in MATLAB to obtain the condensation model of the rocker box. In the polycondensation model, the center of the shaft / bearing hole on the rocker box is taken as the interface node for coupling with multi-stage gear transmission. Firstly, the natural frequency and vibration mode of the finite element model of the rocker box are obtained in the finite element software ABAQUS, and then the natural frequency and vibration mode of the condensed model of the rocker box are obtained in MATLAB. The above work, on the one hand, can get the natural vibration characteristics of rocker box, on the other hand, can verify the correctness of condensation operation.
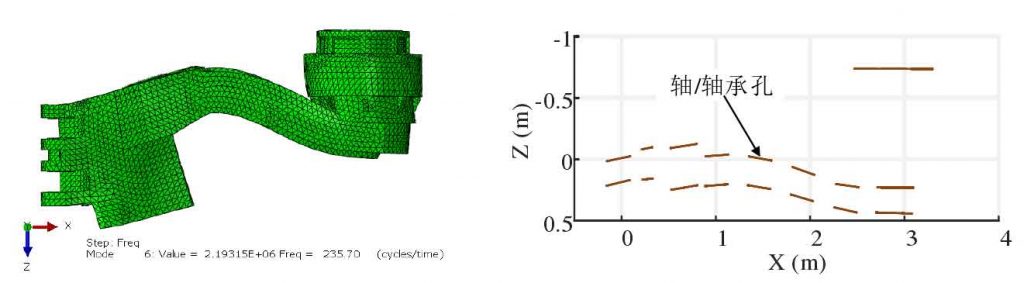
The first 30 natural frequencies of the rocker box calculated by the finite element model and the condensation model are compared. The maximum absolute error is 24.63 Hz (the 23rd order), and the maximum relative error is 2.70% (the 23rd order). According to section 2.2.2, the condensed model of rocker box has 162 degrees of freedom, so 162 modes can be calculated. Among them, all natural frequencies have no multiple roots. As shown in the figure, the modal shapes calculated by the finite element model and the condensed model are compared. Here, only two arbitrary modes are given. The brown circle in the figure indicates the shaft / bearing hole on the rocker box, and its vibration mode is consistent with the calculation results of the finite element model. From the angle of natural frequency and vibration mode, the natural vibration characteristics of the rocker box calculated by the finite element model and the condensation model are compared, which proves that the modal transformation in MATLAB is correct.