Analyzing the efficiency of hypoid gear drives involves considering various factors that influence their overall performance. Here are some key factors to consider when assessing the efficiency of hypoid gear drives and potential optimization strategies:
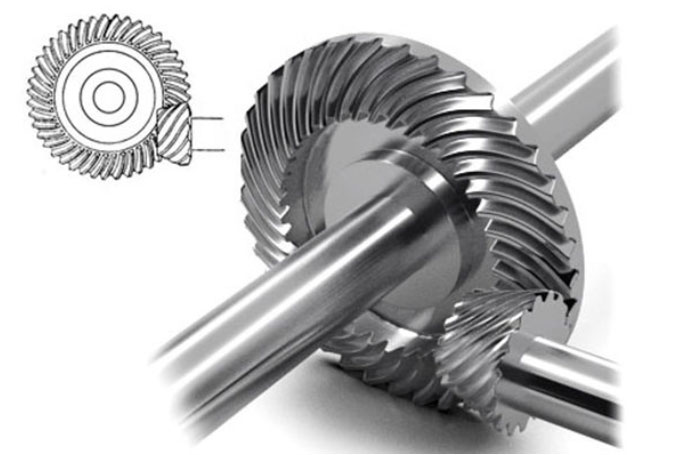
- Gear Design: The design of the hypoid gears plays a significant role in their efficiency. Optimizing the tooth geometry, such as pressure angle and tooth profile, can improve the meshing characteristics and reduce frictional losses. Advanced gear design software and simulation tools can be used to analyze and optimize the gear design for improved efficiency.
- Lubrication: Proper lubrication is crucial for reducing friction and maximizing efficiency in hypoid gear drives. Selecting the right lubricant with appropriate viscosity and additives helps minimize frictional losses and ensure smooth gear operation. Regular maintenance and monitoring of lubrication conditions are essential to maintain optimal efficiency.
- Surface Finish and Coatings: The surface finish of the gear teeth affects friction and efficiency. Finer surface finishes, achieved through grinding or lapping processes, reduce friction and improve efficiency. Applying low-friction coatings or treatments to the gear surfaces can further enhance efficiency by reducing friction and wear.
- Gear Tooth Alignment: Proper alignment of hypoid gears is critical for efficient power transmission. Accurate positioning and alignment of the gears help ensure proper tooth contact and minimize sliding friction. Precision manufacturing techniques and careful assembly practices are necessary to achieve optimal gear tooth alignment.
- Gear Material Selection: Choosing the right materials for hypoid gears can impact their efficiency. Materials with low friction coefficients, high strength, and good wear resistance are desirable. Selecting materials with the appropriate hardness and surface treatment can minimize frictional losses and extend gear life.
- Operating Conditions: The operating conditions of the gear drive, such as speed, load, and temperature, can affect its efficiency. Optimizing these operating parameters within the gear drive’s design limits can help maximize efficiency. For example, operating at lower speeds or reducing excessive loading can minimize losses and improve efficiency.
- Noise Reduction Measures: Noise generation in hypoid gear drives is often accompanied by energy losses. Implementing noise reduction techniques, such as optimizing tooth contact patterns, surface treatments, and gear housing design, can indirectly contribute to improved efficiency.
To optimize the efficiency of hypoid gear drives, it is crucial to analyze these factors holistically and implement appropriate measures at each stage, from design to operation and maintenance. Collaboration between gear designers, manufacturers, and end-users is key to identifying potential areas for optimization and continuously improving the efficiency of hypoid gear drives in specific applications.