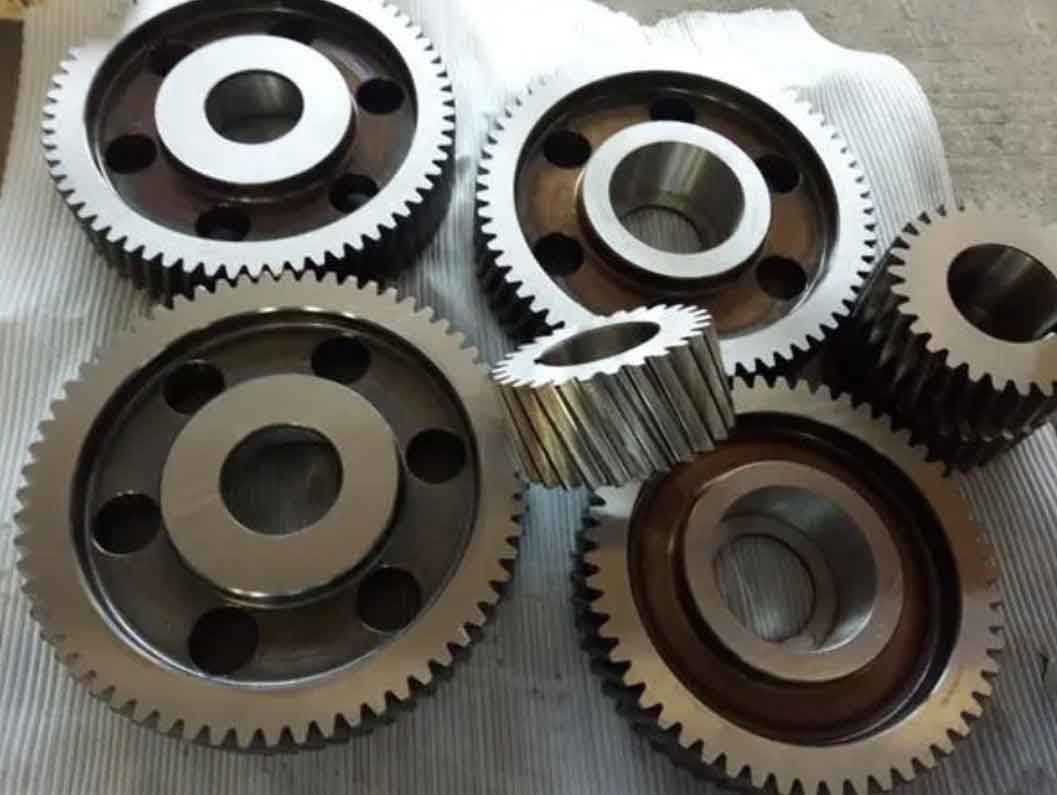
Spur gears are a staple in robotics due to their simplicity, efficiency, and ease of manufacture. Their role in robotic applications often focuses on transmitting motion and power efficiently between parallel shafts within a compact space. Analyzing the efficiency of spur gears in robotics involves looking at several factors, including gear design, material selection, load handling, and the specific requirements of robotic operations. Here’s a detailed breakdown:
1. Mechanical Efficiency
- High Power Transmission: Spur gears are known for their ability to transmit a significant amount of power without slipping. This is crucial in robotics, where precise control over movement and power is necessary.
- Efficiency Rate: Typically, spur gears can achieve mechanical efficiencies up to 98-99% under optimal conditions. This high efficiency is due to the straightforward contact between spur gear teeth, which minimizes energy losses from slippage or misalignment.
2. Design Optimization
- Tooth Profile: The involute tooth profile common in spur gears provides consistent, smooth transfer of motion and power with minimal loss. The uniformity of tooth engagement reduces peak stresses and distributes load evenly, enhancing durability and performance.
- Material Choices: Lightweight materials such as aluminum or advanced polymers can be used to reduce the overall weight of the robot, thereby increasing efficiency. For higher load applications, hardened steels or titanium alloys might be used to handle the increased stresses without compromising spur gear integrity.
- Gear Ratios: Selecting optimal spur gear ratios in robotic systems is crucial to maintain balance between torque output and speed, directly impacting the robotic system’s overall efficiency.
3. Thermal Management
- Heat Generation: Under high loads or high-speed conditions, spur gears can generate significant heat, which may reduce efficiency if not properly managed.
- Cooling Techniques: Implementing passive or active cooling systems in spur gear assembly can help dissipate heat more effectively, maintaining operational efficiency even under strenuous conditions.
4. Lubrication
- Lubricant Selection: Using the appropriate lubricant not only reduces friction and wear but also improves the energy efficiency of spur gear system. Synthetic lubricants, for example, can perform better under a wide range of temperatures and loads.
- Maintenance: Regular lubrication and maintenance ensure that spur gears operate smoothly without excess energy losses due to friction or wear.
5. Noise and Vibration
- Impact on Efficiency: Noise and vibration indicate inefficiencies within spur gear system, such as misalignment, wear, or improper tooth engagement. Addressing these issues not only improves operational noise levels but also enhances mechanical efficiency.
- Damping Solutions: Implementing vibration damping techniques and using materials that naturally absorb sound and vibration can help maintain the efficiency of spur gears by reducing the energy lost to these factors.
6. Integration and System Design
- Compact Design: Spur gears are favored in robotics for their ability to fit into compact spaces without sacrificing performance. Efficient integration into the robotic system without unnecessary bulk or complexity can significantly enhance overall system efficiency.
- Modularity: The use of modular spur gear systems allows for easier upgrades and replacements, ensuring that the most efficient spur gear configurations are used as technology advances.
7. Application-Specific Considerations
- Load and Speed Requirements: The specific demands of the robotic application (e.g., heavy lifting vs. high precision tasks) dictate the design and material selection for spur gears, impacting their efficiency in those specific contexts.
- Environment: Operating environments with dust, debris, or corrosive elements require spur gears made from materials or with coatings that can withstand such conditions without degradation.
Conclusion
In robotics, the efficiency of spur gears is crucial not only for energy conservation but also for the precision and reliability of the robot’s operations. By optimizing gear design, material selection, lubrication, and thermal management, the efficiency of spur gears can be maximized, thereby enhancing the performance and longevity of robotic systems.