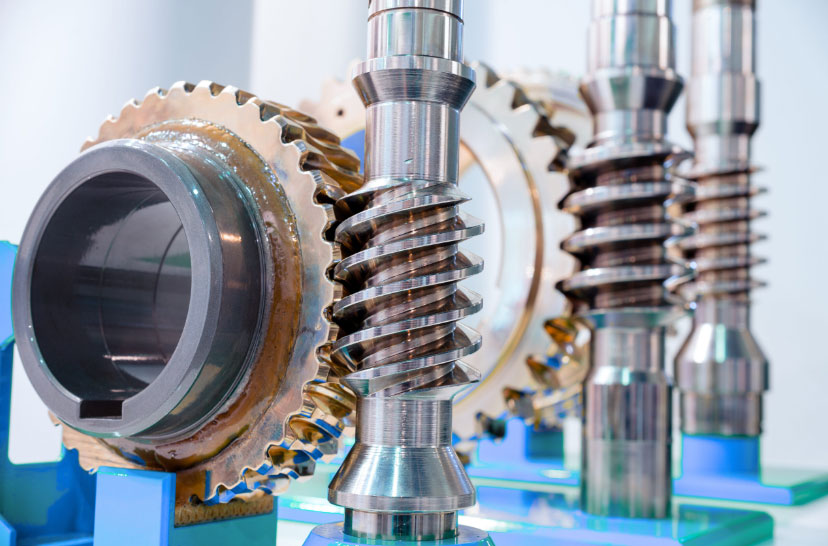
Analyzing tooth profiles is a crucial step in designing custom worm gears for optimal performance. The tooth profile of a worm gear affects several important factors, including load-carrying capacity, efficiency, backlash, and smoothness of motion. Engineers use various methods and considerations to analyze tooth profiles and achieve the desired performance characteristics. Here are some key aspects of tooth profile analysis for custom worm gear performance:
1. Involute Profile:
The involute tooth profile is commonly used in worm gears due to its desirable characteristics, such as smooth engagement and uniform load distribution along the tooth flank. The involute profile ensures gradual contact between gear teeth, reducing impact forces during meshing and minimizing noise and vibration.
2. Pressure Angle:
The pressure angle is the angle between the line of action and the line perpendicular to the gear tooth surface. The pressure angle influences the contact ratio, gear efficiency, and load capacity. A higher pressure angle can result in a larger contact area and higher load-carrying capacity, but it may lead to increased sliding friction and lower efficiency.
3. Helix Angle:
The helix angle is the angle between the gear axis and the worm’s helix. The helix angle affects the axial thrust and efficiency of the worm gear. A higher helix angle increases the axial thrust, which may necessitate additional thrust bearings in the gear system.
4. Lead Angle:
The lead angle is the angle between the helix and the gear axis. It determines the gear ratio and influences the contact ratio and efficiency. A larger lead angle generally results in a higher gear ratio and more contact between teeth, increasing load capacity but also potentially increasing sliding friction.
5. Backlash and Clearance:
Analyzing tooth profiles helps to optimize backlash and clearance in custom worm gears. Minimizing backlash is essential for accurate positioning and motion control, while providing adequate clearance prevents interference between gear teeth and ensures smooth meshing.
6. Contact Ratio:
The contact ratio is the number of pairs of teeth in contact at any given moment. A higher contact ratio distributes the load over multiple teeth, reducing tooth stresses and enhancing gear durability and load-carrying capacity.
7. Tooth Fillets and Root Radii:
Properly designed fillets and root radii help reduce stress concentrations and increase the strength of the gear teeth, leading to improved gear performance and longevity.
8. Finite Element Analysis (FEA):
FEA simulations are used to analyze tooth profiles’ stress distribution and deformation under different load conditions. FEA allows engineers to optimize the tooth profile for maximum strength and efficiency.
9. Lubrication and Wear Analysis:
Analyzing tooth profiles also considers the lubrication regime and wear patterns to ensure efficient power transmission and extended gear life.
By analyzing tooth profiles using these methods and considerations, engineers can design custom worm gears with optimized performance characteristics, such as high load-carrying capacity, efficiency, minimal backlash, and smooth motion, meeting the specific requirements of various applications with precision and reliability.