Straight, spiral, and hypoid bevel gears are commonly used in various applications due to their unique characteristics and advantages. Let’s explore the applications and advantages of each type of bevel gear:
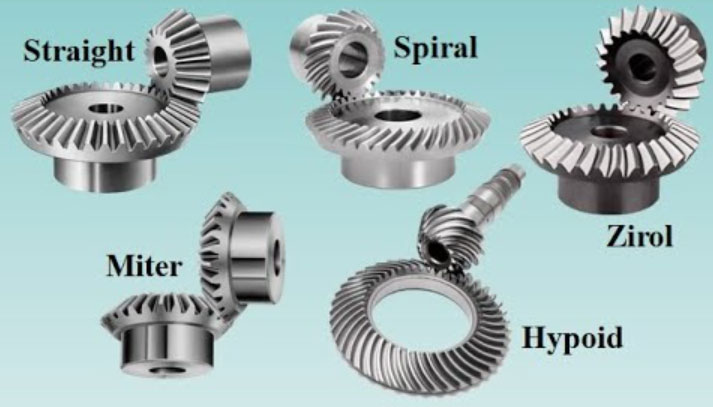
1.Straight Bevel Gears:
Applications:
- Automobiles: Straight bevel gears are often used in the differential gear system of rear-wheel-drive vehicles. They transmit power between the drive shaft and the rear wheels.
- Industrial Machinery: Straight bevel gears find applications in various industrial machinery, including machine tools, printing presses, and agricultural equipment.
Advantages:
- Simplified Design: Straight bevel gears have a simple design with straight teeth, making them easier to manufacture and assemble.
- Cost-Effective: Straight bevel gears are generally more cost-effective to produce compared to spiral and hypoid bevel gears.
- Efficient Power Transmission: Straight bevel gears have low sliding friction and can efficiently transmit power over short distances.
2.Spiral Bevel Gears:
Applications:
- Automotive Industry: Spiral bevel gears are commonly used in automotive differentials, transfer cases, and axle drives. They provide smooth power transmission, high torque capacity, and improved vehicle handling.
- Aerospace Industry: Spiral bevel gears are utilized in helicopter transmissions, aircraft landing gear systems, and other aerospace applications that require high precision, reliability, and load-carrying capacity.
- Industrial Machinery: Spiral bevel gears find applications in heavy-duty industrial machinery, such as mining equipment, steel mills, and power generation systems.
Advantages:
- Smooth Operation: Spiral bevel gears offer gradual tooth engagement, resulting in smoother and quieter operation compared to straight bevel gears.
- High Load Capacity: The spiral tooth profile distributes the load more evenly across the gear teeth, enabling higher torque transmission and load-carrying capacity.
- Misalignment Tolerance: Spiral bevel gears can accommodate small misalignments between the gear axes, reducing the risk of tooth damage and improving gear performance.
3.Hypoid Bevel Gears:
Applications:
- Automotive Industry: Hypoid bevel gears are commonly used in automotive applications, particularly in front-wheel-drive and all-wheel-drive vehicles. They are utilized in the final drive system to transmit power from the engine to the wheels.
- Power Tools and Appliances: Hypoid bevel gears are found in power tools, appliances, and heavy-duty machinery that require high torque and compact design.
Advantages:
- Compact Design: Hypoid bevel gears have a non-intersecting axis design, allowing for a more compact gearbox configuration.
- High Torque Transmission: The offset nature of the hypoid gear design allows for increased torque transmission compared to spiral bevel gears.
- Efficiency: Hypoid gears exhibit lower friction and improved efficiency compared to worm gears, making them suitable for applications that require high torque and efficiency.
It’s important to note that each type of bevel gear has specific design considerations and performance characteristics, and the selection of the gear type depends on the application requirements, load conditions, efficiency targets, and other factors. Consulting with gear specialists and considering the specific needs of the application is crucial for choosing the appropriate bevel gear type.