The involute planetary gear reducer with small tooth difference has been developed recently, and its application range is gradually expanding, such as hoisting and transportation machinery, light industrial machinery, etc. The reducer is characterized by compact structure, small volume, light weight and large deceleration. The gear pair for the reducer is an internal gear pair composed of an external gear and an internal gear. The number of teeth of the outer gear is one or two teeth or three or four teeth less than the number of teeth of the inner gear. Because the difference between the number of teeth of the two gears is very small, it is called less tooth difference.
1.Transmission principle and structure
The transmission schematic diagram of the single eccentric planetary reducer with small tooth difference. The internal gear 2 and the external gear 1 form a pair of internal engagement with small tooth difference. When the high-speed eccentric shaft 3 rotates, the outer gear 1 (i.e. the planetary gear) is forced to rotate in the inner gear. At the same time, there is only a small number of teeth difference between the internal and external gears, so when the external gear rotates for one revolution, a small amount of self rotation movement occurs. This low-speed rotation movement is transmitted to low-speed shaft 5 for output through a so-called “parallel shaft coupling” 4, i.e. output mechanism. When the transmission power is large, the double eccentric high-speed shaft is often used, and the two rows of star wheels mesh with the internal gear at the same time at a distance of 180 ° . In the reducer, the low-speed rotation motion of the two planetary wheels is transmitted to the low-speed shaft for output through the pin shaft.
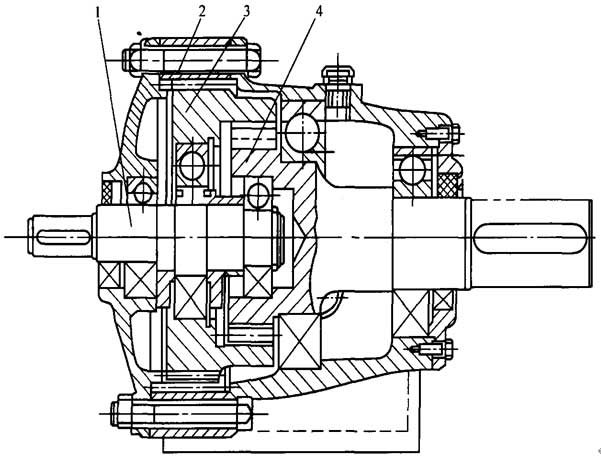
At present, the commonly used output mechanisms are floating cross disc, pin shaft type , cross slider type and zero tooth difference type , etc. From the perspective of transmission principle, they are all the same, but with different structural forms; from the perspective of assembly, pin shaft reducer is more troublesome, and other types are more convenient.
2.Assembly position of pin hole (equally divided hole) and tooth of pin shaft output mechanism
When only one planetary gear is used, it is unnecessary to consider the position relationship between the hole and the tooth during assembly. When two planetary gears are used, the teeth and holes of the planetary gear must be in a certain position, so that the planetary gear and the pin shaft mechanism can be installed into the internal gear from the axial direction, and the two rows of planetary gears can achieve synchronous operation. Generally, when machining planetary gears, take the finished pin hole as the reference, and align the center line of a tooth with the center line of a pin hole. Mark the two gears after machining.
Because the two planetary gears are meshed with the internal gears at the position of 180 ° staggered with each other, the assembly positions of the two planetary gears are different for different tooth number difference and odd, even and internal gears during assembly:
(1) The internal gear has even number of teeth, and the number difference z2-z1 = 1, 3, 5 (z2 and Z1 are the number of teeth of internal gear and planetary gear respectively), that is to say, when the number of teeth of planetary gear is odd, the tooth shape of internal gear at 0 ° and 180 ° is the same (the same is tooth or slot), while the tooth shape of planetary gear at corresponding position is opposite. Therefore, it is necessary to stagger the positioning marks of the two planetary gears by 180 ° and then install them into the internal gear.
(2) The number of teeth of internal gear is any number (odd or even), and the difference of teeth z2-z1 = 2, 4, 6 At this time, the number of teeth of the planetary gear and the internal gear are both odd or even. When assembling, put the positioning marks on the two planetary gears in the same direction to mesh with the internal gear.
(3) The internal gear has odd number of teeth, and the number difference z2-z1 = 1, 3, 5 , that is, when the number of teeth of the planetary gear is even, at the position 180 ° apart, the tooth shape of the internal gear is opposite to that at 0 °, while the tooth shape of the planetary gear is the same (Fig. 6-30).
When installing the second planetary gear, it is necessary to find out another pin hole . It is required that the number of teeth between the center line of this hole and the center line of hole a (marked pin hole) is an integer plus 1 / 2 teeth. During installation, turn hole B to the 0 ° direction, i.e. stagger the marked holes on the two planetary gears by a certain number of holes, and then install the inner gear.
3.Problems to be paid attention to when assembling the reducer with small tooth difference
In addition to the assembly problems related to the manufacturer, during the disassembly and installation, attention shall be paid to ensure that there is appropriate axial clearance (generally no less than 0.5mm) between the planes with relative motion such as planetary wheel, cross floating plate, low-speed shaft, etc.
Generally, the assembly sequence is to assemble the machine base into a group, the eccentric shaft, planetary gear and other running components into a group, and then place the running parts vertically, and finally put on the inner ring gear and end cover and other parts, so that the assembly is more convenient.