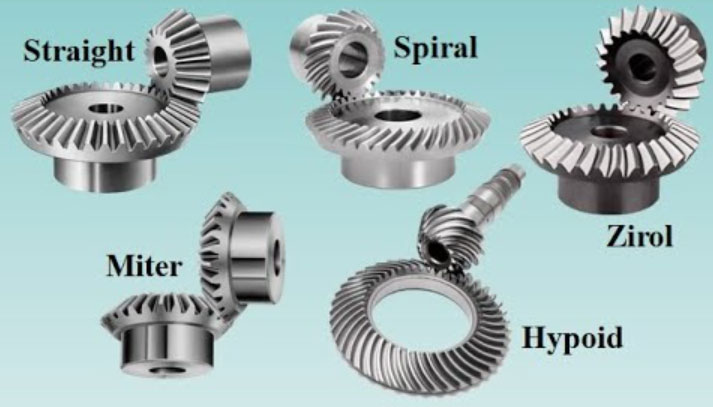
Bevel gear manufacturing techniques have evolved over time, incorporating innovative processes and best practices to ensure high-quality gears with precise tooth geometry and reliable performance. Let’s explore some of the key manufacturing techniques and best practices in bevel gear production:
1. Gear Design and Simulation:
Effective gear design and simulation software tools are utilized to develop optimal tooth profiles, gear geometry, and load-carrying capacity. Advanced computer-aided design (CAD) and computer-aided manufacturing (CAM) software are employed to model and simulate the gear manufacturing process, allowing for accurate analysis and optimization of gear performance.
2. Gear Cutting Methods: a. Milling:
Milling is a common method for producing bevel gears. It involves using a milling machine with a rotating cutter to remove material and form the gear teeth. Modern CNC (Computer Numerical Control) milling machines allow for precise control and repeatability in gear cutting. b. Hobbing: Hobbing is another widely used method for bevel gear manufacturing. It involves using a hobbing machine with a rotating hob cutter to generate the gear teeth by gradually cutting into the gear blank. Hobbing allows for high productivity and accuracy in gear production. c. Form Grinding: In some cases, bevel gears are produced through form grinding, which involves using a grinding wheel with the inverse shape of the gear teeth to grind the gear teeth into the workpiece. Form grinding ensures high precision and surface finish, especially for gears with complex tooth profiles.
3. Heat Treatment:
Heat treatment is a critical step in bevel gear manufacturing to enhance the hardness, durability, and strength of the gears. Processes such as carburizing, quenching, and tempering are commonly employed to achieve the desired hardness and mechanical properties. Heat treatment helps ensure that the gears can withstand the loads and operating conditions they will encounter.
4. Quality Control and Inspection:
Thorough quality control measures are implemented throughout the manufacturing process to ensure the production of high-quality bevel gears. Advanced inspection techniques such as coordinate measuring machines (CMM) and gear measuring instruments are used to verify the dimensional accuracy, tooth profile, surface finish, and other critical parameters of the gears. Non-destructive testing methods like magnetic particle inspection or ultrasonic testing may also be employed to detect any potential defects.
5. Lubrication and Surface Treatment:
Appropriate lubrication and surface treatment are crucial for bevel gears to reduce friction, wear, and noise, and improve their overall performance and longevity. Lubrication systems and surface treatments like coating or nitriding can be applied to enhance the gear’s surface hardness, reduce friction, and improve resistance to wear and corrosion.
6. Continuous Improvement and Quality Management:
Continuous improvement and quality management practices are essential in bevel gear manufacturing. Manufacturers invest in research and development to explore new materials, coatings, and production techniques. They also employ stringent quality management systems to ensure consistent quality, traceability, and adherence to industry standards.
By incorporating these manufacturing techniques and best practices, bevel gear manufacturers can produce high-quality gears with precise tooth geometry, excellent mechanical properties, and reliable performance. The combination of advanced design, modern machining processes, heat treatment, quality control, lubrication, and continuous improvement ensures the production of bevel gears that meet the stringent requirements of various industries and applications.