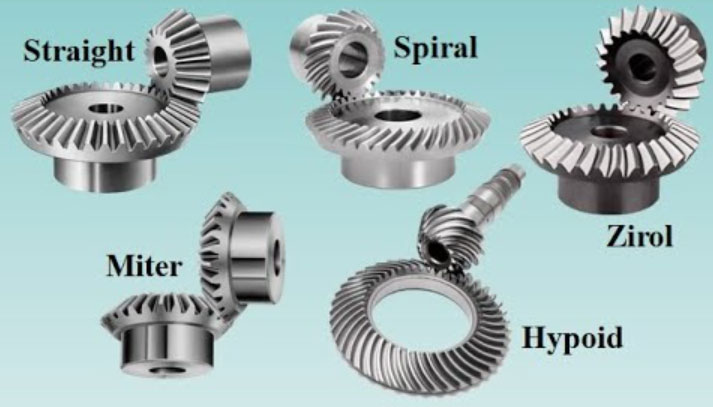
Bevel gears are engineered to strike a balance between strength and precision in gear systems. They are designed to efficiently transmit power and motion while maintaining accurate tooth engagement and reliable operation. Let’s explore how bevel gears achieve this balance between strength and precision:
1. Tooth Profile and Geometry:
The tooth profile and geometry of bevel gears are carefully designed to optimize both strength and precision. The shape of the tooth, including the involute profile and tooth thickness, is engineered to ensure maximum load-carrying capacity and minimize stress concentrations. The tooth geometry is precisely calculated to achieve proper contact and minimize backlash, ensuring accurate motion control.
2. Materials and Heat Treatment:
Bevel gears are manufactured using high-quality materials and undergo heat treatment processes to enhance their strength and durability. Materials such as alloy steels, carbon steels, and stainless steels with specific mechanical properties are selected to withstand the loads and operating conditions. Heat treatment processes like carburizing, quenching, and tempering further enhance the gear’s hardness, strength, and wear resistance.
3. Tooth Surface Quality and Finishing:
The surface quality and finishing of bevel gears play a crucial role in balancing strength and precision. Proper grinding, honing, or lapping techniques are employed to achieve the desired surface finish and tooth accuracy. Smooth tooth surfaces reduce friction, wear, and noise, while ensuring precise tooth engagement and accurate motion transmission.
4. Precision Machining and Gear Cutting Methods:
Bevel gears are machined with precision using advanced manufacturing techniques. CNC (Computer Numerical Control) machining ensures accurate and repeatable tooth profiles, resulting in precise tooth engagement and consistent performance. Gear cutting methods such as milling, hobbing, or grinding are employed with precision to achieve the desired tooth geometry and surface finish.
5. Lubrication and Maintenance:
Proper lubrication and maintenance are essential to ensure the balance between strength and precision in bevel gears. Adequate lubrication reduces friction, wear, and heat generation, preserving the gear’s strength and precision over time. Regular maintenance, including inspections, lubricant replacement, and addressing any signs of wear or damage, helps maintain the gear’s performance and extend its lifespan.
6. Design Optimization and Simulation:
Bevel gear designs undergo optimization and simulation processes to achieve the desired balance between strength and precision. Computer-aided design (CAD) software and simulation tools analyze the gear’s performance under various load conditions, allowing for design refinements and validation. This iterative process ensures that the gear design meets the required strength and precision criteria.
By carefully considering the tooth profile, materials, manufacturing processes, lubrication, and maintenance, bevel gears are engineered to achieve the optimal balance between strength and precision. Their ability to efficiently transmit power, provide precise motion control, and withstand demanding loads is a testament to the successful integration of strength and precision in gear systems. This balance enables bevel gears to excel in a wide range of applications, including automotive, aerospace, marine, industrial machinery, and robotics.