Bevel gears and miter gears are both used to transmit motion between intersecting shafts. They are most commonly used in applications where the angle between the two shafts needs to remain constant. Though these gears are similar in their basic function, there are key differences in their design features, applications, and capabilities. Here is a comparative analysis of their characteristics:
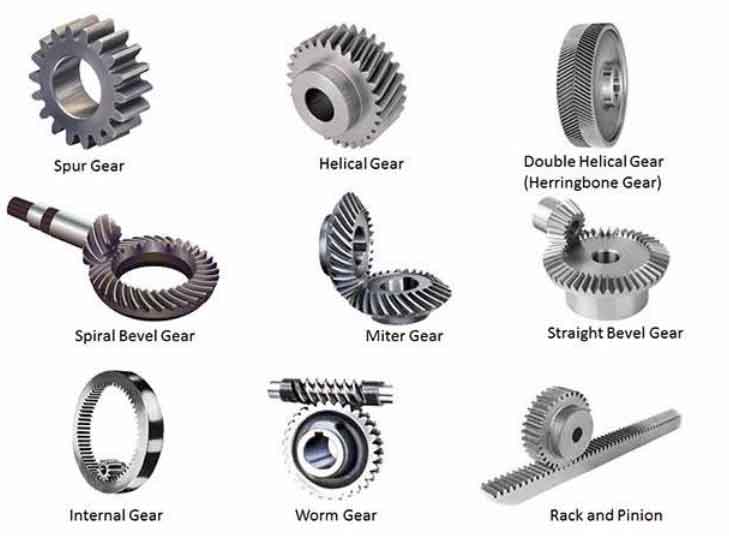
- Design:
- Bevel Gears: Bevel gears are cone-shaped gears designed for transmitting motion between intersecting shafts. They can have various tooth profiles and angles depending on the intended application. Their angle can be anywhere between 1° and 180°, but the most common is 90°.
- Miter Gears: Miter gears are a specialized type of bevel gear with a 1:1 gear ratio and 90° angle between the shafts. The teeth on miter gears are generally cut at a 45° angle. Due to their equal gear ratio and mating gears being identical, miter gears are often regarded as a specific subset of bevel gears.
- Gear Ratio:
- Bevel Gears: Bevel gears can have varying gear ratios depending on their tooth count and dimensions. This makes them versatile for a wide range of applications where different speeds and torque levels are required.
- Miter Gears: Miter gears always have a 1:1 gear ratio, meaning the shaft speed and torque are maintained at the same levels when transmitted from one shaft to another. This limits their use in applications where equal speeds and torque are required.
- Applications:
- Bevel Gears: Bevel gears are used in a variety of applications such as automotive differentials, power tools, helicopter transmissions, and industrial machinery. They are chosen for their versatility in terms of gear ratios and the ability to transmit motion between shafts at different angles.
- Miter Gears: Miter gears are commonly used in simpler applications, such as clock mechanisms, power transmission in small appliances, and light-duty machinery, where equal speeds and torque are required between the interacting shafts.
- Costs and Manufacturing:
- Bevel Gears: Given the varied tooth profiles and angles, manufacturing bevel gears can be more complex and expensive, especially when custom designs are required or the gears need to handle higher loads and stresses.
- Miter Gears: As miter gears are specific to a 1:1 gear ratio and 90° angle, their manufacturing process is standardized and less complex. This can result in lower costs and faster production times.
- Efficiency:
- Bevel Gears: Bevel gears exhibit varying levels of efficiency depending on their design, tooth geometry, and the materials used. Specialized tooth profiles can be designed to increase their efficiency.
- Miter Gears: Miter gears’ efficiency tends to be comparable to typical bevel gears. However, due to their 1:1 gear ratio, they may not be the most efficient choice in situations where different gear ratios would be more effective.
In conclusion, the primary difference between bevel gears and miter gears lies in their gear ratio, design complexity, and the range of applications they are used in. Bevel gears offer more versatility when it comes to varying gear ratios and angles between shafts, while miter gears are limited to a 1:1 gear ratio and 90° angle. Choosing between these gears depends on the specific requirements of an application in terms of speed, torque, and shaft orientation.