The FH hypoid gear is still used as an example, and the basic parameters of the gear used in the simulation are the same, so we will not repeat it here.
According to the preset design parameters of tooth surface modification, the concave surface of the small wheel and the convex surface of the large wheel are the working surface, while the convex surface of the small wheel and the concave surface of the large wheel are the non working surfaces.
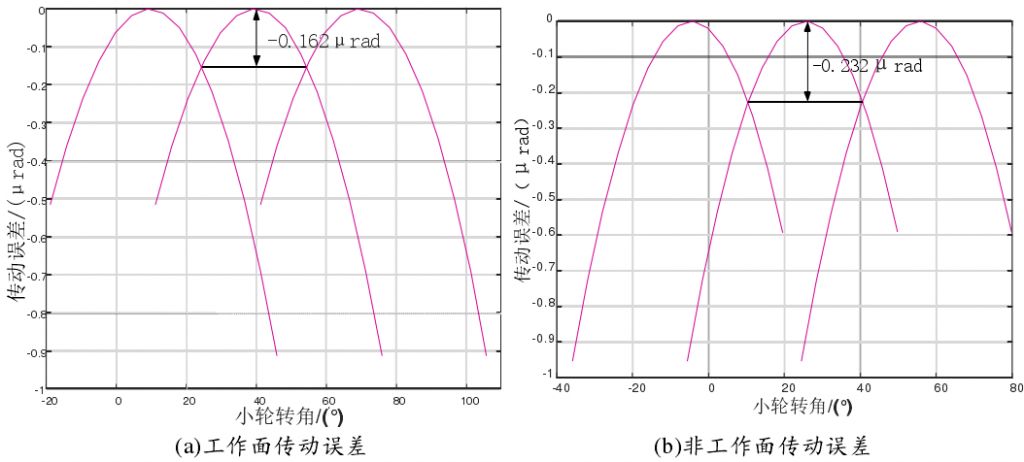
After calculation, the transmission error of the target tooth surface is shown in Fig. 1 and the contact mark is shown in Fig. 2

The maximum errors of working face and non working face in the transmission process are -0.162 μ rad and -0.232 μ rad respectively, which are 8% and 7.2% different from the preset maximum transmission error, and the results basically meet the expectation. Now through the tooth surface error matrix, the adjustment amount of the processing parameters of the small wheel and the result of the adjustment amount of the processing parameters of the small wheel are obtained.
A method of ease off active design for paired tooth surfaces is proposed. Firstly, according to the generating principle, the transmission relationship without transmission error is replaced by the preset transmission error curve by the gear angle, and the auxiliary tooth surface of the pinion can be obtained. The tooth surface conforms to the preset transmission error law with second order parabola. After that, the contact area can be controlled to meet the preset requirements. Finally, the tooth surface error is obtained by subtracting the theoretical tooth surface parameters from the target tooth surface parameters of the small gear, and the tooth surface error matrix equation is solved to obtain the adjustment amount of the processing parameters of the pinion. Finally, through the analysis of an example, it is concluded that the method meets the expected setting parameters, which provides a theoretical basis for the active control of tooth surface performance in the design stage.