The potential energy obtained by the comprehensive energy method is: Hertz contact potential energy, bending potential energy, shear deformation potential energy, radial compression deformation potential energy and matrix flexible deformation potential energy, which forms the total potential energy for engagement of a pair of involute spur gear pairs.
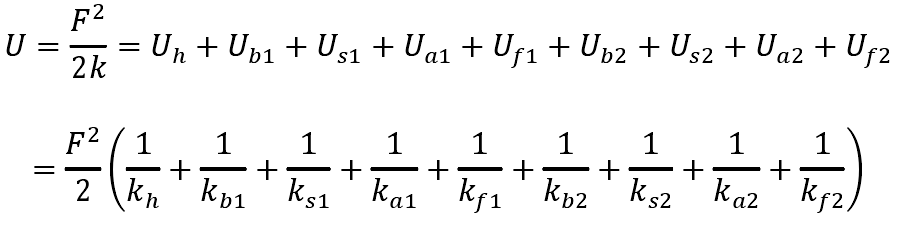
Where indicates the meshing stiffness of the gear, the subscribed numbers 1 and 2 indicate the driving and driven wheels respectively, and S1 indicates the shear stiffness of the driving wheels.
Then the time-varying meshing stiffness of the gear vice-president can be calculated by the formula as follows:

The formula is to calculate the total time-varying meshing stiffness when a pair of teeth engage in meshing. When two pairs of teeth engage in meshing at the same time, the effective meshing stiffness of the gear vice-president is calculated as follows:

In formula: I = 1 means the first pair of teeth engages; I = 2 means the second pair of teeth engages.
A pair of standard involute spur gear pairs is selected as the research object and the time-varying meshing stiffness of the gear pairs is calculated by MATLAB programming.
Time-varying meshing stiffness of single-tooth pair of gears is shown in Figure 1. The combined stiffness of the meshing points of two meshing gears near the rodent and rodent points is small, and that of the meshing points near the indexing circle is large.
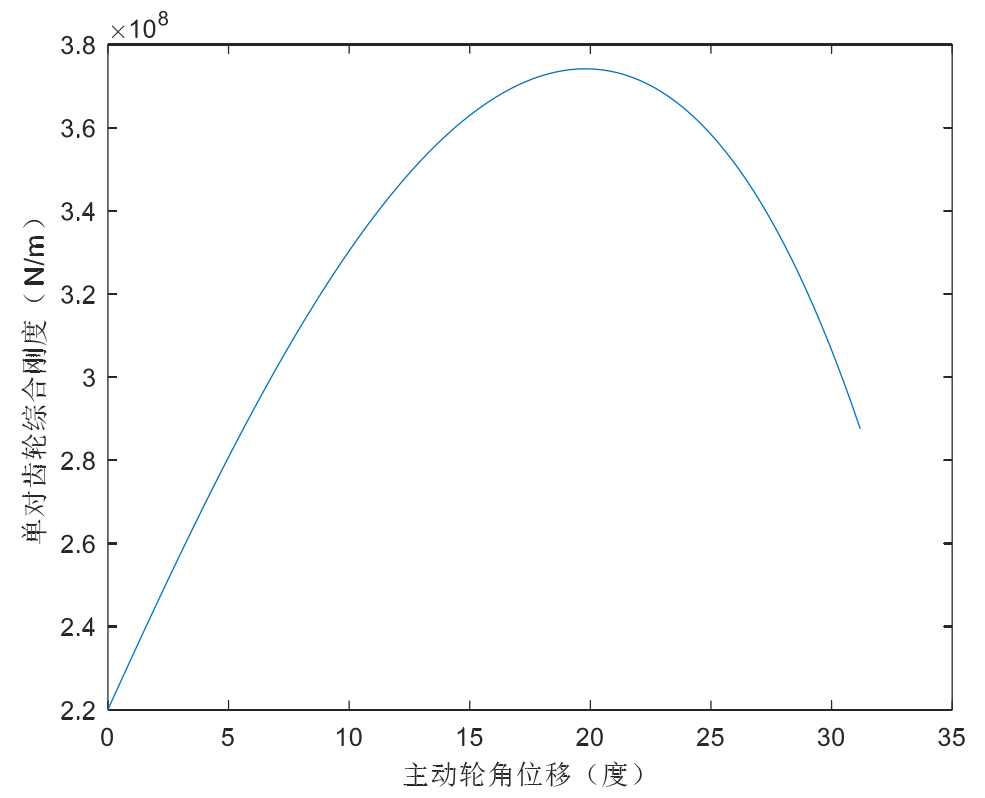
The total time-varying meshing stiffness of gear pair in meshing process is shown in Figure 2. Due to the change of gear pair coincidence degree at all times, the gear pair will engage alternately with single/double teeth during meshing process. The comprehensive stiffness is divided into single-tooth meshing area and double-tooth meshing area; section A-B and E-FSection C-D is single-tooth meshing area, where a pair of teeth engage at the same time, and the elastic deformation of the teeth is small and the comprehensive meshing stiffness is large. At this time, a pair of teeth engage in meshing, the elastic deformation of the teeth is large and the comprehensive meshing stiffness is small. The comprehensive meshing stiffness of the teeth appears a significant step at the junction of the single-tooth meshing area and the double-tooth meshing area.The alternating engagement characteristics of single and double teeth of gear pair cause sudden change of load acting on the gear teeth and generate dynamic excitation of the transmission process of gear pair.
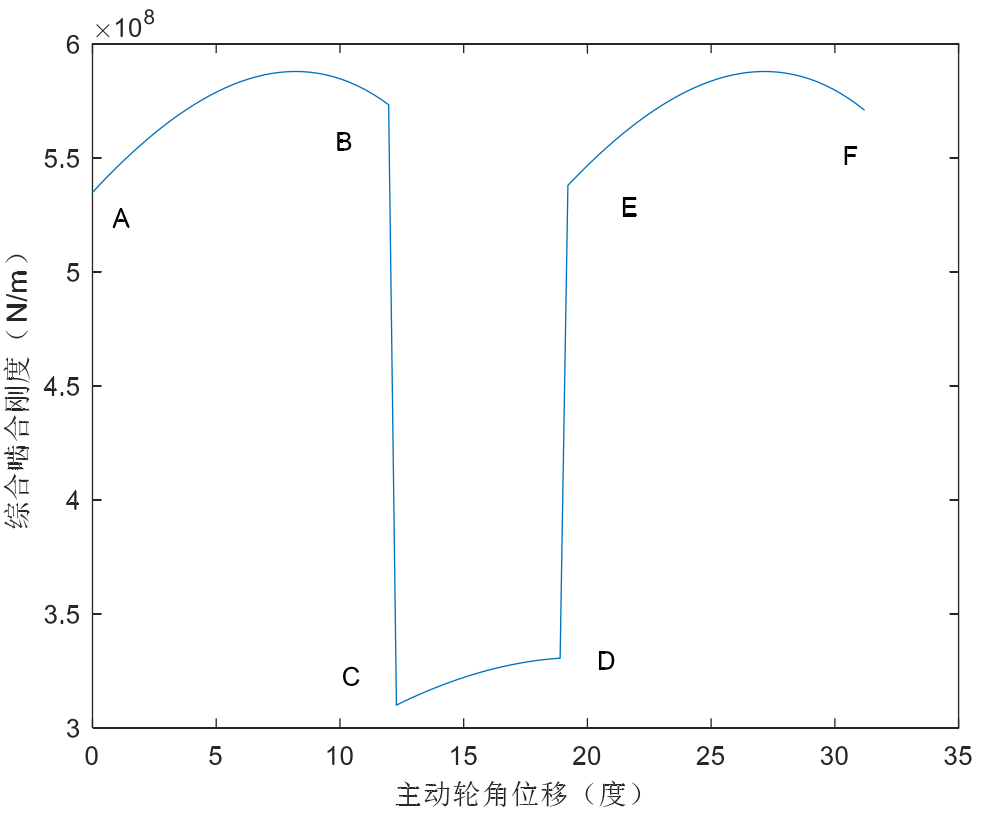
Figure 3 is the calculated comprehensive time-varying stiffness of gear pair. Comparing with the results in Figure 2, it can be found that the variation rule of time-varying meshing stiffness is consistent. Although the meshing stiffness values are not identical due to different gear pair parameters, the stiffness magnitude is the same, thus ensuring the correctness of the method for solving the time-varying meshing stiffness of gear pairs in this paper.
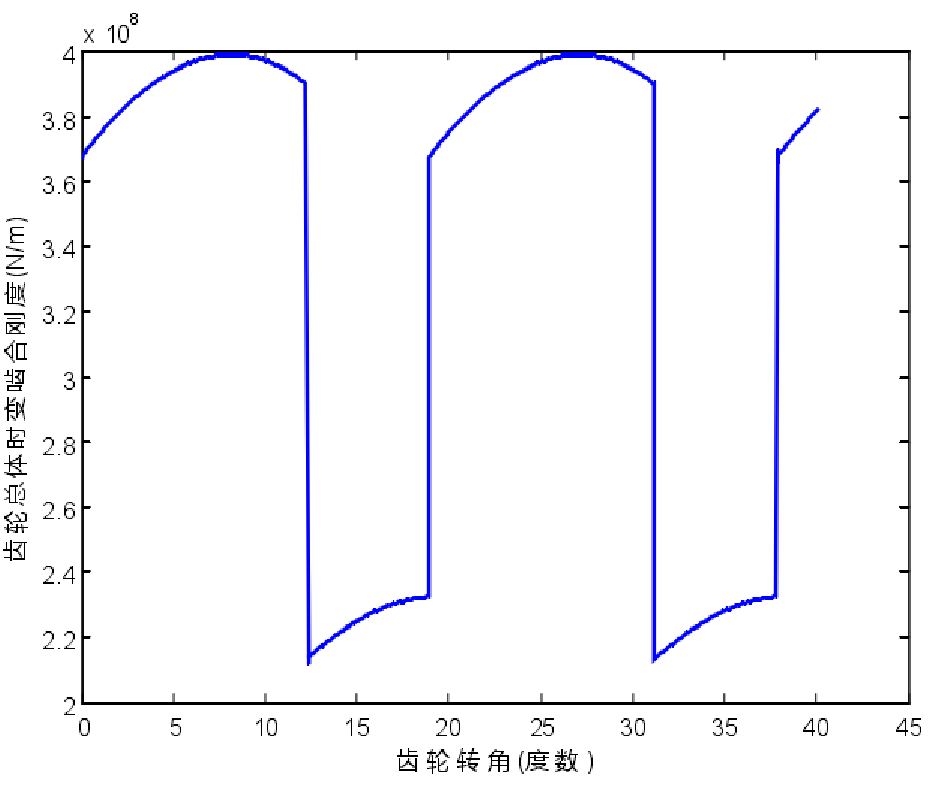