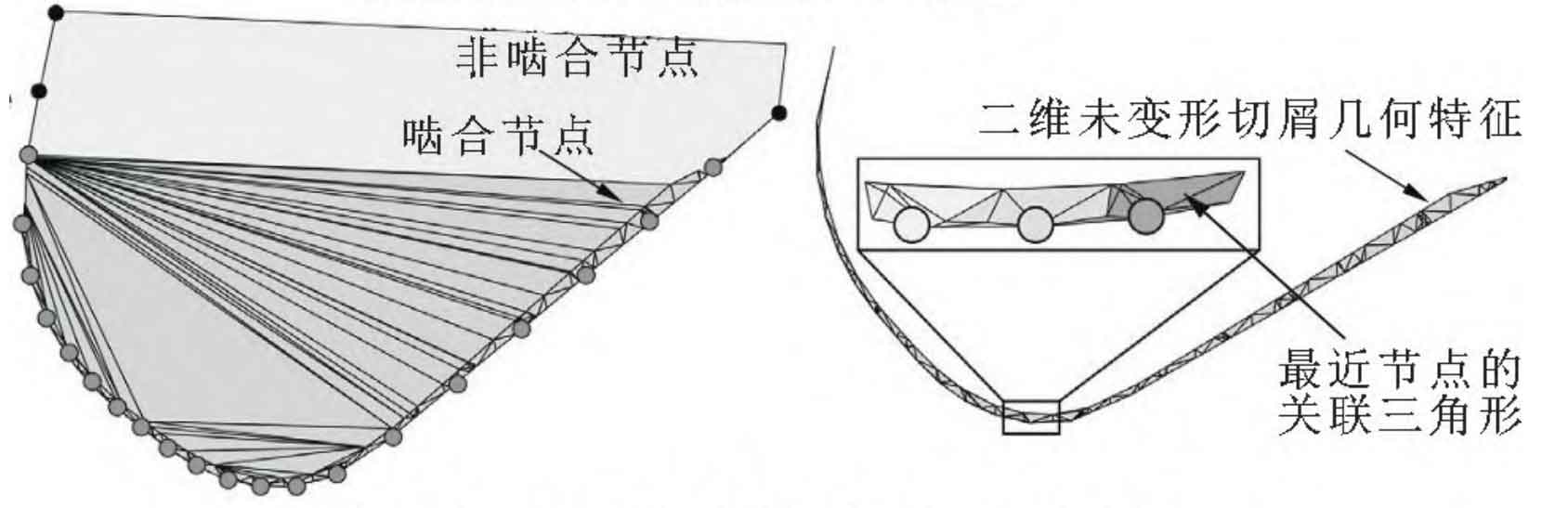
As shown in Figure 1, the triangles that form the two-dimensional undeformed chip are assigned to the nearest mesh node along the cutting edge. Add the areas of the combined triangles to calculate the cutting area a associated with the local mesh node. Using the oblique cutting model, the force distribution Ft in the local tangent direction, the force distribution Ff in the feed direction and the force distribution Fr in the radial direction of each meshing node can be calculated by the following formula:
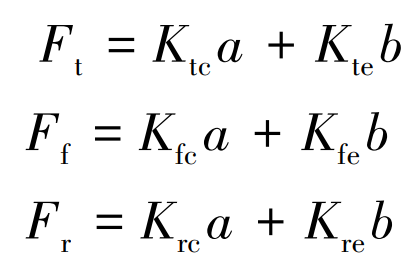
Where: Ktc, Kfc and Krc are cutting force coefficients; Kte, Kfe and Kre are edge stress coefficients; B is the edge width related to the meshing node.
The calculation method of cutting speed vector vc is as follows:

Where: Pi is the ith meshing node on the cutting edge; ω C is the tool angular velocity vector; ω G is the angular velocity vector of cylindrical gear; RPi, c is the coordinate of point Pi in TCS; RPi, g is the coordinate of point Pi in WCS; Vf is the vector representation of the axial feed rate.
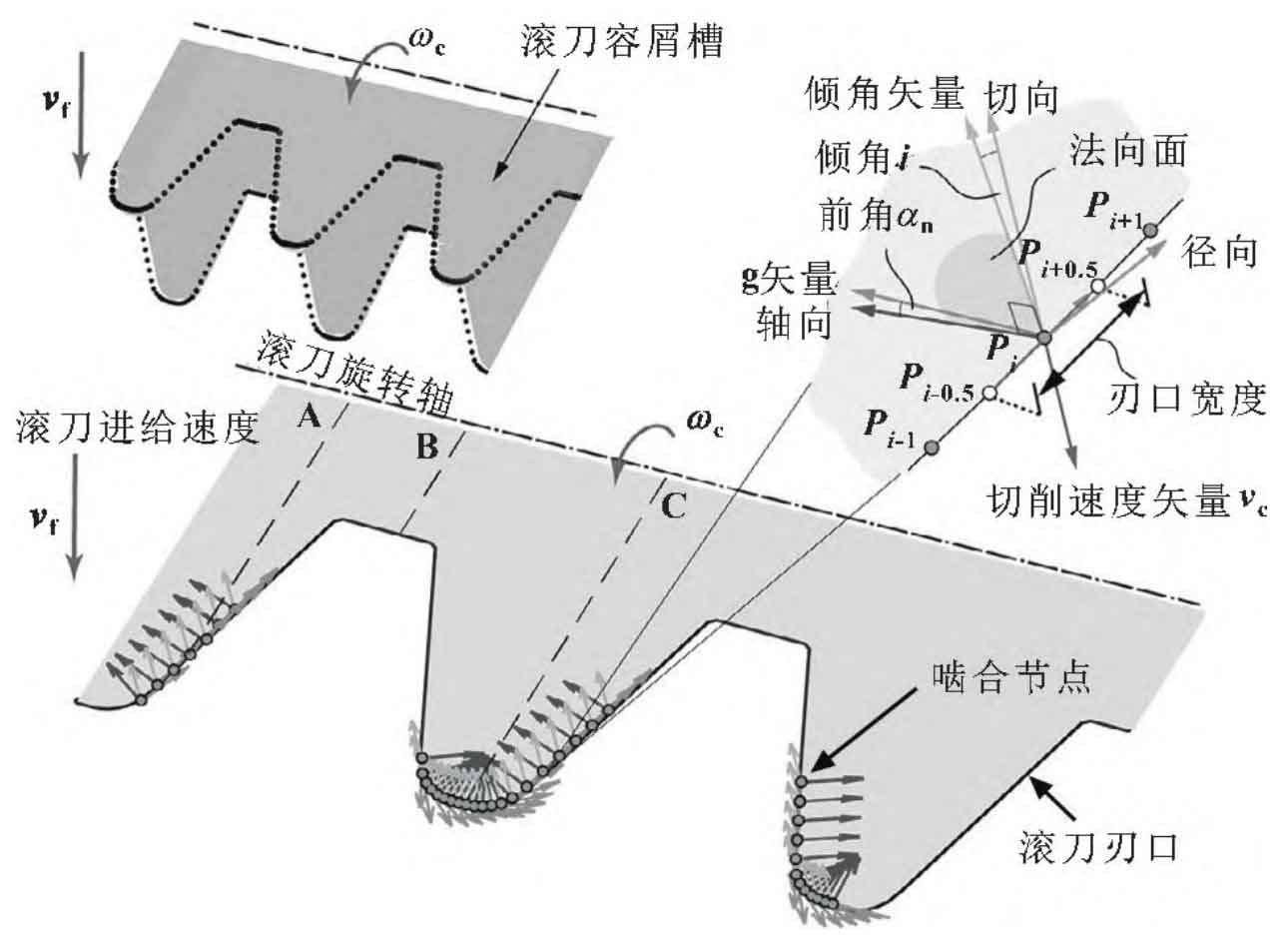
After calculating the cutting speed vector vc at Pi, the unit vector of tangential, feed and radial cylindrical gear cutting force and the local front angle can be determined α N and inclination angle i. The calculation method of cylindrical gear cutting force is shown in Figure 2. The tangential, feed and radial unit vectors help to determine the direction of the scalar cylindrical gear cutting force formula on each meshing node, so that the force distribution on all meshing nodes is vectorized at each time step.