1.Actual meshing line length of tooth profile
In the transmission process of helical gear, the meshing line of tooth profile is tangent to the two basic circles of driving wheel and driven wheel, as shown in the figure is the end face meshing diagram of helical gear.
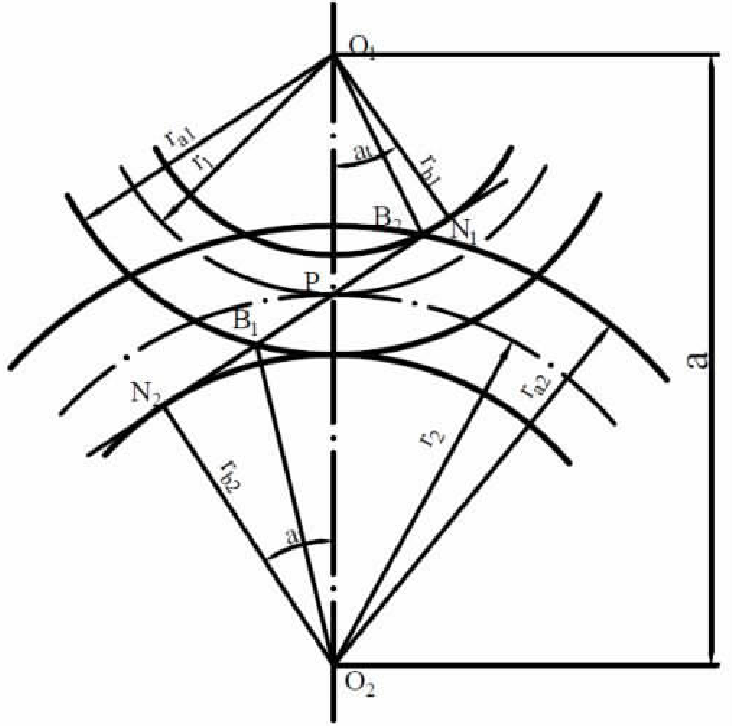
According to the geometric relationship of meshing, the actual length of meshing line is as follows:
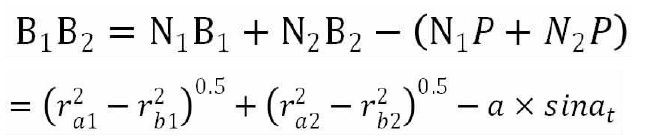
Where:
Ra1 — top circle radius of sun gear, mm;
RB1 — base circle radius of sun wheel, mm;
Ra2 — top circle radius of planet gear, mm;
Rb2 — base circle radius of planetary gear, mm;
At — end pressure angle, mm.
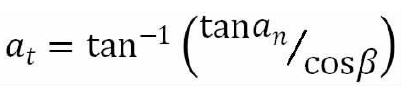
Where:
An — normal pressure angle, RAD;
β – helix angle, rad.
2.Calculation of helical gear coincidence
In the process of gear transmission, the gear coincidence degree represents the average value of the number of teeth engaged in actual meshing during the meshing process. Under the same load condition, the more the number of teeth engaged in meshing, the greater the load allocated to each pair of teeth, which is conducive to improving the stability and bearing capacity of gear transmission.
The coincidence degree of helical gear is different from that of spur gear. When calculating spur gear, only the end face coincidence degree is considered. However, helical gear not only has face coincidence degree, but also axial contact degree calculation. The sum of the two is the total coincidence degree of helical gear.
The base circle pitch of helical gear is as follows:
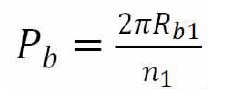
The coincidence degree of end face is as follows:
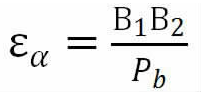
The axial coincidence degree is as follows:
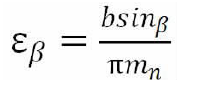
Where: Mn — normal modulus.
The total coincidence degree is as follows:
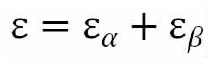
The total coincidence degree of helical gear means the average value of the number of teeth engaged in actual meshing within a pitch time of gear rotation. The value is often not an integer, which indicates that the number of gear pairs is between a minimum value and a maximum value in the process of gear rotation. In order to realize the normal transmission of the gear, the coincidence degree must be greater than or equal to 1, that is, when the last pair of teeth is not out of engagement, the next pair of teeth has entered into meshing. The larger the total contact degree of helical gear is, the smaller the load evenly distributed on a single tooth.