(1) Through analysis, it can be seen that there is no mechanism to determine the size of helical gear drum shape, but the design principles of helical gear drum shape teeth are consistent, the two teeth are clutching, and there is no edge point contact under the maximum inclination.
The data show that one view holds that the contact deformation is the main factor affecting the drum shape, while the influence of the meshing angle is ignored. The other view holds that the size of the helical gear meshing angle is the key factor determining the drum shape, and the contact deformation is rarely considered to have a greater impact on the helical gear drum shape. However, the contact deformation and meshing angle exist simultaneously in the actual meshing process of two helical gears. Only when both contact deformation and meshing inclination are considered, the drum shape can be determined, which is close to the ideal drum shape. To ensure the maximum meshing skewness of helical gears without intersection, the edge phenomenon can be avoided.
In this case, it must be ensured that the load per unit tooth width can be reduced to the greatest extent when the inclination angle is 0 or close to 0. The starting point of helical gear drum shape measurement is that the contact of helical gear with elastic deformation body is affected after loading. Therefore, the drum shape is studied on this basis.
(2) In general, select the middle of the tooth width as the center of the drum, as shown in Figure 1.
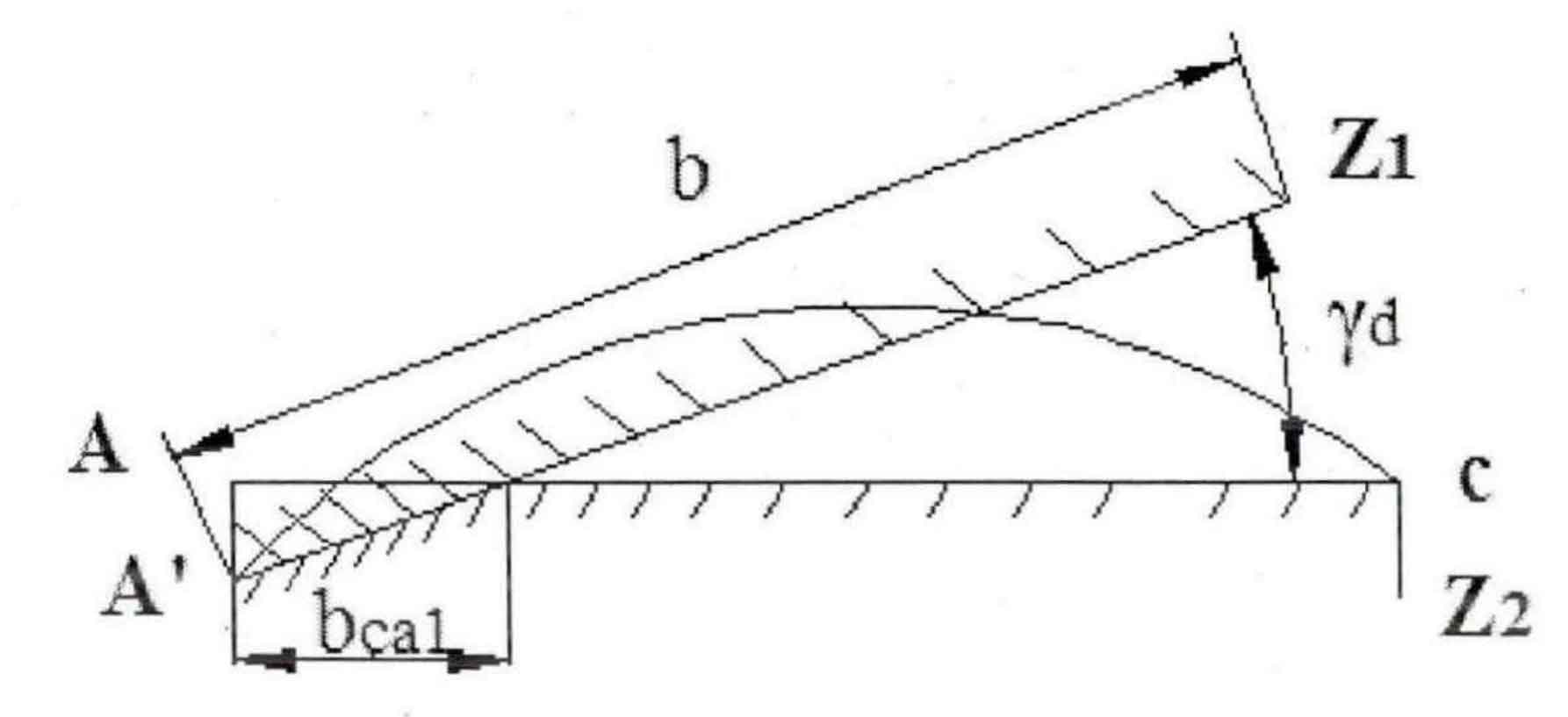
After considering the influence of many factors, and for the convenience of machining, the center position of the tooth width is selected as the center of the drum shape. According to the analysis results of helical gear and shaft elastic deformation, the tooth width geometry is also the most suitable location for the drum center, and the drum amount of the two helical gears is 0.013mm. Draw the drum gear according to the above drum shape, as shown in Figure 2.
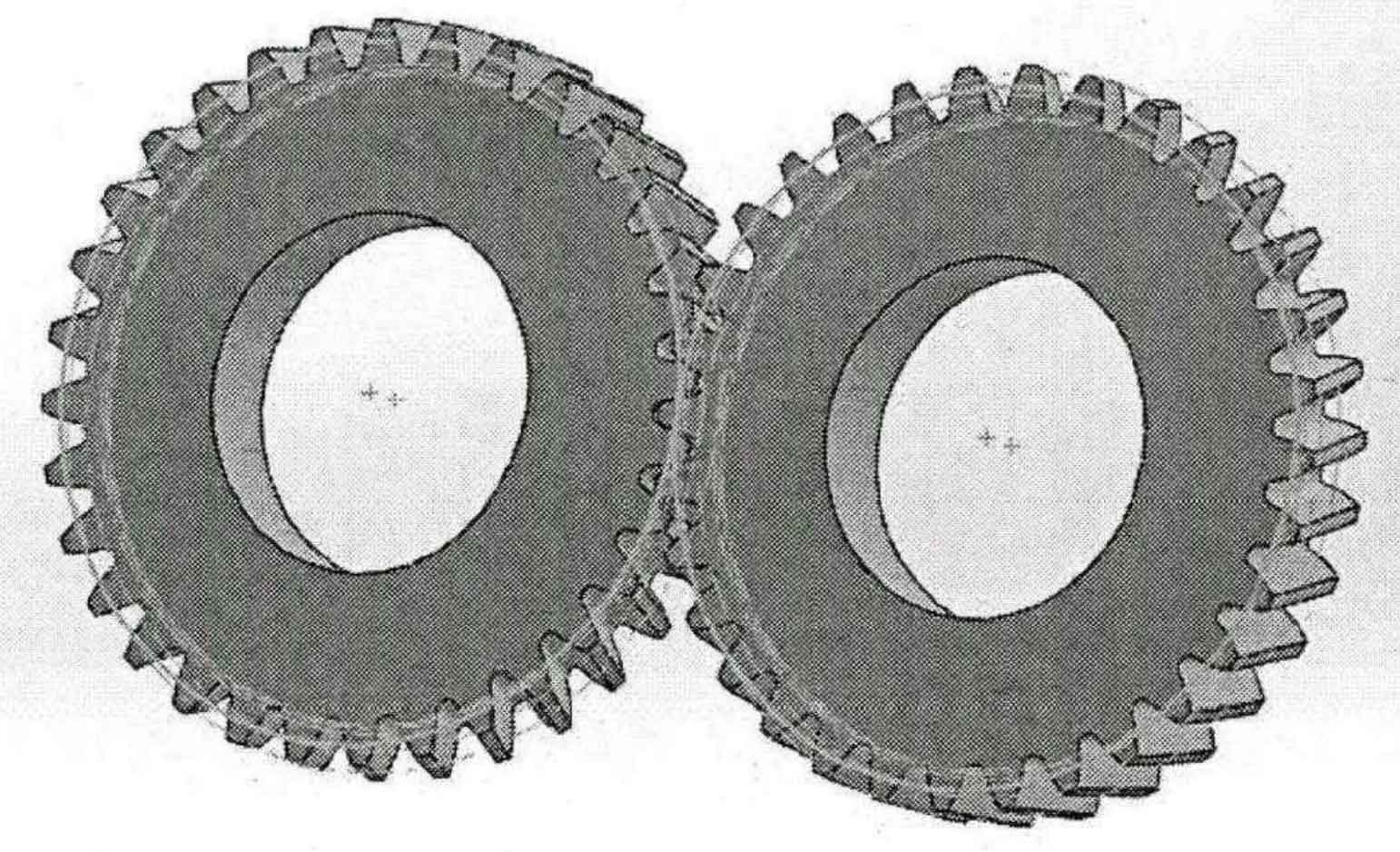