In the study of gear tooth surface pitting fault, the main shapes of pitting corrosion are rectangular pitting, elliptical pitting and circular pitting. In this paper, the gear pitting model is circular pitting, and the single circular pitting fault tooth is shown in the red dotted line in Fig. 2-3. The location and size of pitting on tooth surface can be expressed by three variables: (μ, τ, δ), where μ is the distance from the center of pitting to the root of tooth; τ is the radius of circular pitting; and δ is the depth of pitting. In order to facilitate the derivation of the equation, a straight line is used to approximate the fillet curve of the tooth root.
For pitting fault teeth, the parameters ℎ, ℎ x, ax, IX are different from those of healthy gears. In addition, the contact width of tooth surface is not L. When the distance between the tooth section and the tooth root is x, the formula is defined as follows:
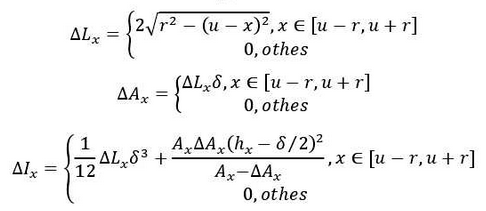
The bending stiffness of the gear with pitting corrosion can be obtained by combining the equations and simplifying the equations
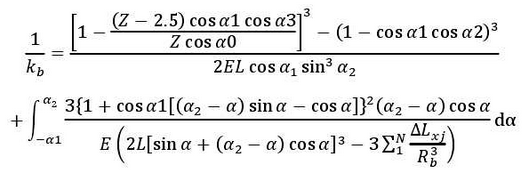
Similarly, the shear stiffness and axial compression stiffness of pitting failure gear can be expressed as follows:
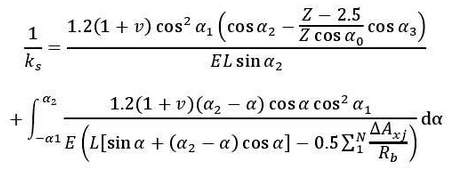
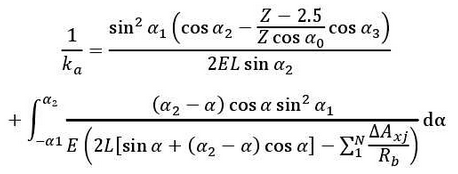
For the pitting fault gear, the actual contact width of tooth surface is l − {LX instead of L. Accordingly, the Hertz contact stiffness of the gear pair with circular tooth surface pitting can be expressed as follows:
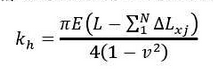
In the formula: n is the number of pitting corrosion on the tooth surface. The above equation can be used to calculate the meshing stiffness of gears under the condition of pitting corrosion at any given rotation angle.