When the parameters of the motion law of the machine tool are determined, the motion equations can be formed by the formula:
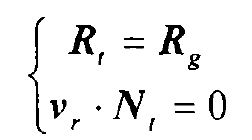
The calculation of tooth surface coordinates usually first specifies the position of the coordinate point along the direction of tooth length and tooth height, and then calculates the rotation angle of the point in the Cartesian coordinate system.
After the serial number of the mesh node of the tooth surface is specified as shown in the figure, the rrecoery z can be determined. When the rolling ratio of the machine tool is I, the angular speed of the production wheel is ω 02mm 1, which can be known from the machining theory of spiral bevel gears.

Taking the cutter head parameters t, θ 1, the cutter head rotation angle θ t and the workpiece parameter θ as unknown parameters, the tooth surface coordinates can be obtained by solving the equations. The coordinate values of the tooth surface can be found in the appendix.
The system of equations is a system of non-linear equations, which can be solved by Broden algorithm, that is, quasi-Newton algorithm. Here, VC++ language and Matlab software are used for mixed programming.