The time-varying meshing stiffness of spur gears is one of the main factors that cause impact and noise in spur gear systems. As a natural characteristic of spur gear systems, natural frequency is closely related to the vibration of spur gear systems. Therefore, accurate calculation of meshing stiffness and natural frequency is the basis for the analysis of spur gear vibration characteristics.
Due to the elastic deformation of the gear teeth, there is a difference between the actual rotation angle of the driving wheel (the same as the driven wheel) and the theoretical rotation angle, which is converted into displacement along the meshing line, which is called spur gear transmission error. Therefore, the transmission error can be expressed as:

In the formula: △ ε Indicates the transmission error of the spur gear; Rb1 represents the base circle radius of the driving wheel; θ 1a represents the actual rotation angle of the driving wheel; θ 1b represents the theoretical rotation angle of the driving wheel.
In the case of small angular displacement, there is a coupling relationship between the torsion and lateral displacement of spur gears. Since the normal meshing force acts in the direction of the meshing line along the base circle, the torsional meshing stiffness of the spur gear can be converted into a linear meshing stiffness, which Km can be expressed as:
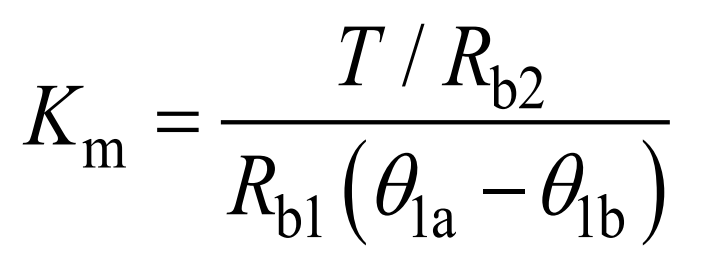
In the formula, T represents the load torque; Rb2 represents the base circle radius of the driven wheel.
The natural frequency f0 has the following relationship with the stiffness Km and the equivalent mass me:
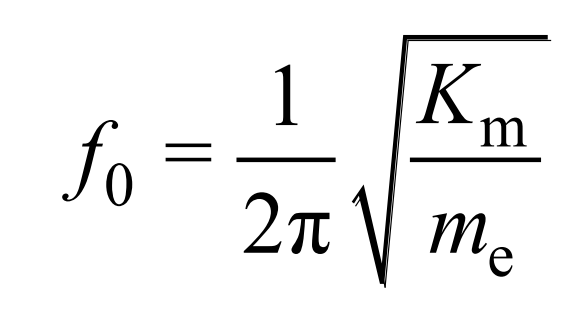
In the formula, me can be expressed as:
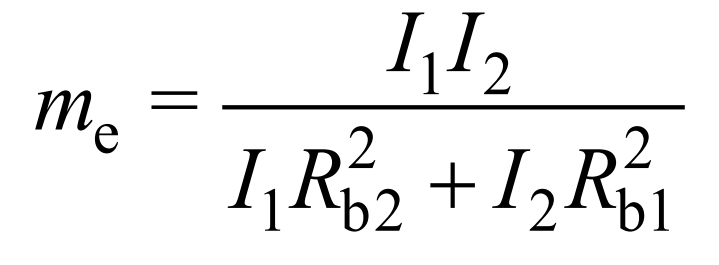
In the formula, I1 represents the rotational inertia of the driving wheel; I2 represents the rotational inertia of the driven wheel.